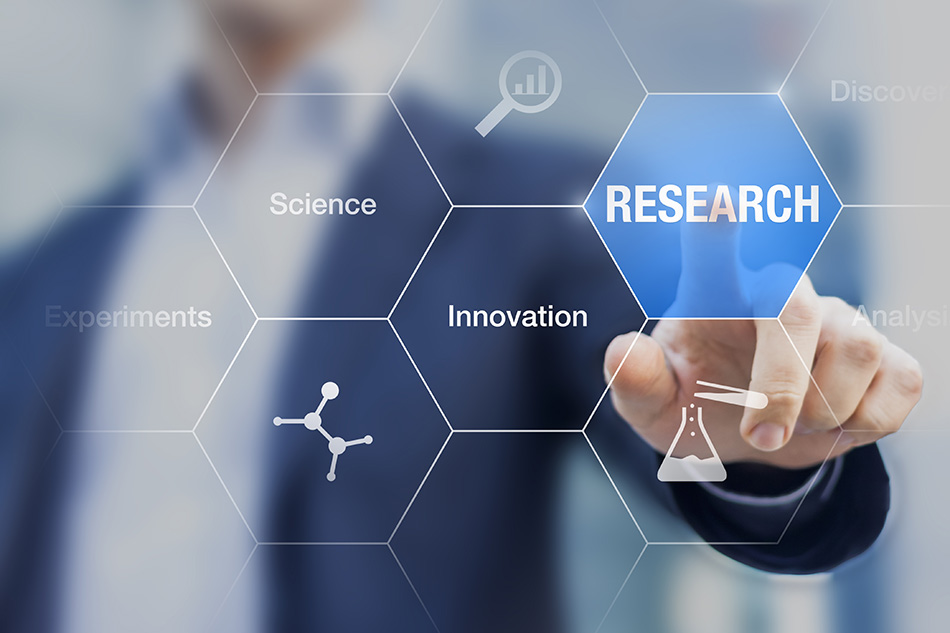
Various recycling-related research projects will receive grant funding from the REMADE Institute. | NicoElNino/Shutterstock
This article has been corrected.
A number of recycling companies and industry associations are involved in research projects that recently received federal funding.
The REMADE Institute, a Rochester, N.Y.-based public-private organization, announced it has awarded grants totaling $5.9 million to 12 research projects. The efforts focus on ways to improve the recycling of paper, plastics, electronics, tires and aluminum, as well as strategies to support remanufacturing of heavy equipment.
A number of organizations, including the Institute of Scrap Recycling Industries (ISRI), WestRock, Graphic Packaging, Niagara Bottling and Lehigh Technologies, are involved in the projects.
Formed in 2017, the Reducing Embodied-Energy and Decreasing Emissions (REMADE) Institute is now helping to fund 31 research projects. The following are a few details of the newly funded projects:
Paper recycling
- Improved deinking flotation: Virginia Tech is working on technology to better separate contaminants, including inks, from recovered paper, so mills can produce brighter fibers from post-consumer sources. The ultimate goal is to allow them to boost their consumption of recovered fiber.
- Paper and paperboard modeling: Northwestern University, Yale University and ISRI are working together in a systems analysis project. They will model and test the U.S. fiber recycling industry, specifically looking at paper and paperboard. The project will provide a virtual testbed that explores resilience to changes in scrap quantities, quality, markets and prices, as well as consider future changes in recycling capacities and technologies.
- Studying fiber recovery approaches: The Massachusetts Institute of Technology (MIT), American Forest & Paper Association (AF&PA), WestRock and Graphic Packaging are working together to analyze economic and environmental implications of changes in the recovery of fibers. They’ll use a dynamic modeling framework that integrates material-flow analysis, life-cycle inventories and technical cost modeling to inform ideas for cost-effective fiber recovery approaches.
Plastics recycling
- Reinforced polymer composites: Oklahoma State University, Niagara Bottling (private-label bottled water company) and Shaw Industries (carpet product manufacturer) are working together to boost the recycling of bottles and carpeting by combining both materials in reinforced recycled polymer composites. Those composites could then be used to make repairable plastic pallets and acoustic panels.
Electronics recycling
- Leaching technologies: The University of Utah and electronics recycling company Sunnking are working to adapt relatively low-cost and low-energy leaching processes to directly recover copper and precious metals from e-scrap, while also allowing the plastics to be recovered. Leaching using chemicals is an alternative to using high-temperature smelting to recover precious metals from scrap electronics.
- Solvent-based approach: The University of Massachusetts-Lowell, Sunnking and ISRI are involved in a project demonstrating the potential of a solvent-based process to recover mixed metals and plastics from e-scrap.
Rubber recycling
- Tire-to-tire recycling: Michelin, Northwestern University and Nike are working on a project to boost the use of post-consumer rubber in new tires. The goal is to increase the amount of micronized rubber powder from recovered tires used in the production of composite polymer materials (CPM), which is a mix of virgin and recycled rubber used to make new tires.
- Rubber in the road: Iowa State University (ISU), Michelin and Lehigh Technologies (a subsidiary of Michelin) are working to better utilize ground rubber from tires in pavement. The project uses an ISU technology that matches the density of ground tire rubber with asphalt by using simple compounding techniques. The result is improved storage stability and a better asphalt.
Aluminum recycling
- Aerospace aluminum research: The University of Illinois at Urbana-Champaign and Eck Industries are working together to develop a process for recycling wrought aluminum scrap into a castable high-second secondary aluminum alloy. The target feedstock is aerospace aluminum scrap. The goal is to overcome issues such as hot tearing and micro segregation that currently limit the industry’s ability to recycle the material.
Heavy equipment manufacturing
- High-speed laser cladding: The Rochester Institute of Technology (RIT), Caterpillar Inc. and Synergy Additive Manufacturing are working on using high-speed laser cladding for the remanufacturing of high-strength equipment components, such as vehicle crankshafts and camshafts. The goal is to increase the reuse rate in manufacturing.
- Design for end-of-life: ISU and John Deere are working to create a data-driven tool to help engineers better design components in industrial and agricultural equipment. The goal is to make those components material-efficient and designed for end-of-life management.
- Remanufacturing rules: RIT, Caterpillar and the Remanufacturing Industries Council (RIC) are working to create a set of pragmatic “design for remanufacturing” rules. The rules would allow design engineers to design components with an eye toward remanufacturing.
This was the second round of grants for the REMADE Institute. The first round was announced in July 2018. Partially funded by the U.S. Department of Energy, the REMADE Institute is led by RIT. A partnership of industry, academia and national labs, the institute’s goal is to reduce energy usage and greenhouse gas emissions in manufacturing.
This article has been corrected to indicate that Oklahoma State University, not Ohio State University, is involved in the reinforced polymer composite project.
More stories about research
- UMass alumni go small with trash-sorting robot pilot
- Closed Loop suggests small-format recycling improvements
- Surveys examine gaps in consumer recycling education