This article originally appeared in the March 2018 issue of Resource Recycling magazine. Subscribe today for access to all print content.
Paper cups symbolize a number of elements of modern culture – our on-the-go mentality, our need for convenience, our love of caffeine – but they have not always evoked the notion of materials recovery. An estimated 643,000 tons of paper beverage cups are used annually in the U.S. and Canada, and far too many of them end up in landfills.
However, efforts by some industry stakeholders could be shifting that narrative. A number of paper mills, materials recovery facilities (MRFs), manufacturers and others are leading the charge to increase the recycling of the paper vessels so many of us regularly have close at hand.
And the current initiatives are driven by more than just an attitude among companies to “go green.” With traditional recovered fiber standbys like newspaper and sorted office paper (SOP) now making up a significantly smaller portion of the recycling stream as society shifts to digital communication, consumers of recovered paper are being forced to dig further into the material mix to fulfill their feedstock needs. Paper cups have emerged as an opportunity in this realm.
“If we had focused solely on SOP and copy paper, we would be out of business right now,” said Mark Bond of Sustana, a paper company with a manufacturing operation in Wisconsin that takes in significant tonnages of recovered paper cups. “If MRFs can process this material, then it is a value-add for them too.”
Handling a unique material makeup
The paper cup of old typically sported a clay bottom with a wax coating to strengthen the cup and avoid leakage. Decades ago, most paper cup manufacturers phased out the wax coating and clay bottom and began to use a very thin layer of plastic to coat the paper.
Today, the majority of cups are coated with polyethylene (PE), and a smaller number are coated with polylactic acid (PLA). The poly coating provides insulation, prevents the cup from leaking or absorbing liquid, and maintains the integrity of the cup’s structure in compliance with manufacturers’ safety and quality standards.
This poly layer can make paper cups more challenging to recycle, and there are ongoing efforts to develop the next generation of coatings for paper cups. In the meantime, some paper mills are finding innovative ways to separate the poly coating from the paper to recover the fiber.
One example is Sustana’s Fox River Fiber facility in De Pere, Wisc., built in 1992. Today, the mill’s 55 employees produce approximately 450 tons of de-inked recycled pulp per day.
The Fox River Fiber site uses SOP as a raw material, in addition to printer waste, milk and juice cartons, and silicone-coated release liners like the ones used as backing for self-adhesive labels. The facility receives approximately 1.3 million pounds of post-consumer paper daily from suppliers within a 350-mile radius.
The process of recycling paper cups and other coated papers in Sustana’s feedstock is called batch pulping and involves several stages. The raw materials are broken down in the pulper, and water is added to dilute the pulp slurry and remove bits of plastic or wire from the fibers. After that, the pulp is sent through a high-density cleaner to remove staples, paper clips, glass and other contaminants.
From there, the slurry passes through a series of screens with openings barely wider than a strand of hair, which eliminate approximately 95 percent of pulp contaminants. The slurry then undergoes a series of additional cleaning steps to further remove contaminants. After cleaning and washing, any sticky adhesives and remaining inks are removed.
The result is a fiber that can be used for printing, writing, and tissue papers – and even FDA-grade paper cups and packaging.
Onward and cup-ward
Though the steps laid out above represent extra work for paper companies, those firms are being pushed to shift their operations as the materials stream itself goes through signigicant transformation.
In recent years, the fiber stream has been impacted by decreasing newspaper circulation and increasing use of corrugated boxes (as e-commerce continues to grow). More recently, the sector has also been affected by the much-discussed decrease in paper scrap exports to China as that country implements import restrictions.
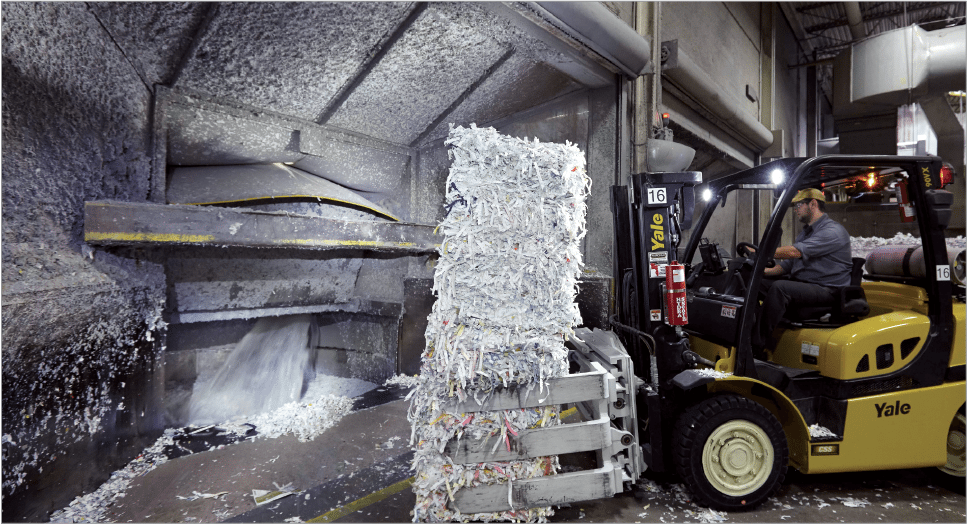
Sustana’s Fox River Fiber operation in Wisconsin receives more than 1 million pounds of post-consumer fiber daily that it integrates into its paper manufacturing process.
Due to those factors, paper cups – with their long, white virgin fiber – are increasingly attractive to mills that are equipped to process them.
“We have tested paper cups thoroughly, and we know we can handle them and other poly-coated material,” said Jay Hunsberger, vice president of sales and marketing at Sustana. “There is valuable fiber in this material that can be used for other products.”
John Mulcahy, vice president of sustainability and compliance for Georgia-Pacific Professional, agrees. “There is value in investing in facilities to dig deeper in the waste stream and recovering more types of fiber,” he said, “including foodservice packaging like cups.”
The Foodservice Packaging Institute (FPI), an industry trade association, has been working to get paper cups and other foodservice items recycled in different localities. One example is in Wisconsin, where the group is looking to help municipalities across the state expand the materials accepted in residential programs and then get cups and other paper products moved to the Georgia-Pacific mill in Green Bay, the Fox River Fiber plant in De Pere and other end users.
Mulcahy sees an opportunity for the paper industry to evolve. “Our approach is not a focus on individual cities so much as to increase mill capabilities to process different grades and be more efficient in the broader market,” he noted.
Trying out methodologies
For mills not designed or optimized to process poly-coated paper, trials are necessary to determine whether and how the fiber can be effectively recovered. And tests focused on various types of poly-coated paper have been taking place over the last few years.
In addition to batch pulping, which is employed by Sustana, mills have also successfully processed cups in a continuous pulping operation. For example, WestRock’s recycled paper mill in Saint Paul, Minn. recently conducted a successful poly-coated cup stock recycling trial. The mill traditionally utilizes a combination of residential mixed paper and old corrugated containers to produce 100 percent recycled content paperboard and medium.
In the trial, single-sided and double-sided poly-coated cup and paperboard stock were added to the furnish entering the pulper. Quantities tested were based on the amount of poly-coated packaging that would be available for recycling from the surrounding communities.
“We found that the inclusion of the poly-coated paper had no perceivable impact on our process or finished product quality,” said Bob Carpenter, general manager of WestRock’s Saint Paul mill.
The ability to recover cups as part of a poly-coat bale (like Fox River Fiber) or a mixed paper bale (like WestRock’s Saint Paul mill) helps to provide options for different communities, depending on the collection and sortation systems employed at the MRF and the commodities produced. The range of mill and trial scenarios suggests that some mills may also be interested in exploring recovery through other commodities.
Graphic Packaging International (GPI), one of the world’s largest manufacturers of folding cartons, unbleached paperboard and coated recycled board, conducted benchtop pulping simulation tests with Western Michigan University and mill trials with various foodservice packaging, including paper cups, at a GPI mill in Kalamazoo, Mich. The testing and trials demonstrated effective fiber separation from the poly and no productivity or quality issues in recycling of these grades.
“Every mill has different capabilities and different criteria for the fiber they have coming in, and they manage their recovered fiber to meet the performance requirements of the recycled products that they manufacture,” said Andrew Johnson, GPI’s vice president of government affairs and sustainability. “As an industry, we are part of this value chain, and we have a responsibility to work together to innovate, educate and solve issues to create opportunities.”
Source of revenue for one county
Communities, of course, will also play a part in how paper cup recycling evolves because cities generally make the decision about whether or not to add materials to residential programs. They also handle outreach to residents.
One Michigan county serves as an example of how communities can fit in.
The Department of Public Works in Emmet County, Mich. operates a cost-effective, self-funded dual-stream program. The county also runs a MRF that processed 11,521 tons of recyclables from Emmet County and four other counties in the region in 2017.
In 2010, Emmet County’s Department of Public Works made upgrades to the MRF, with support from the Carton Council, to begin accepting cartons and added paper cups shortly after. Interestingly, residents are instructed to sort these items with containers, not with the paper segment of the dual stream. The thinking is that keeping the paper cups with containers will limit the amount of potential liquid contact with collected fiber.
However, the county trains staff to positively sort paper cups on both the container and fiber lines to maximize recovery. Emmet County’s paper cup and carton recycling has increased from 74,461 pounds in 2014 to 95,338 pounds in 2017. That material is marketed to mills like Great Lakes Tissue, located in Cheboygan, Mich.
“We were exploring ways to increase recycling of more items to their highest and best use,” said Elisa Seltzer, director of the county’s Department of Public Works. “It is a small percentage of our recycling stream, but it is one of the higher revenue sources.”
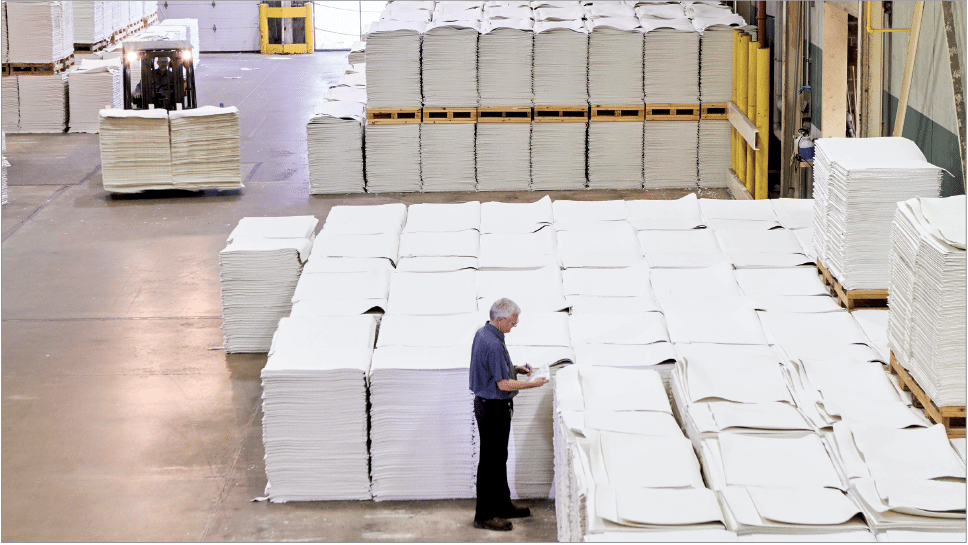
A number of different mill operators are experimenting with different methodologies to use recovered paper cups as feedstock.
Education is a central component of the county’s recycling system. The program website aims to provide clear messaging about what is recyclable. About eight months ago, Emmet County added a search function to its website that allows residents to look up an item to determine whether it can be recycled. Program leaders have seen dozens of searches for paper cups since that change.
Seltzer emphasized the impact of presenting recycling information visually, “At first, we didn’t add the paper cups to the graphics on the website,” she noted. “That caused confusion for our residents.” The county subsequently added a paper cup graphic to the website and found that it helped to steadily increase paper cup recovery.
Paper cups are also accepted in various single-stream programs across the country, including those in San Francisco, Washington, D.C. and Chattanooga, Tenn. Education around these additions has been essential for communities to make sure residents understand that cups should be clean and empty before recycling.
Forward focus for fiber
Many more cities and counties have the potential to add paper cups, where the infrastructure exists. Meanwhile, trials will continue at paper mills to understand the impact and opportunity of recycling cups and other poly-coated items.
Interest in collecting and processing these new materials will only increase as more corporate customers, environmental groups and consumers call for cup recycling. In addition, visible commitments by major brands and industry organizations to support these efforts will accelerate the future of paper cup and packaging recycling.
Marissa Segundo is a communication consultant at RRS and can be reached at [email protected]. Catherine Goodall is a senior consultant at RRS and can be reached at [email protected]. RRS serves as a consultant partner to the Foodservice Packaging Institute.