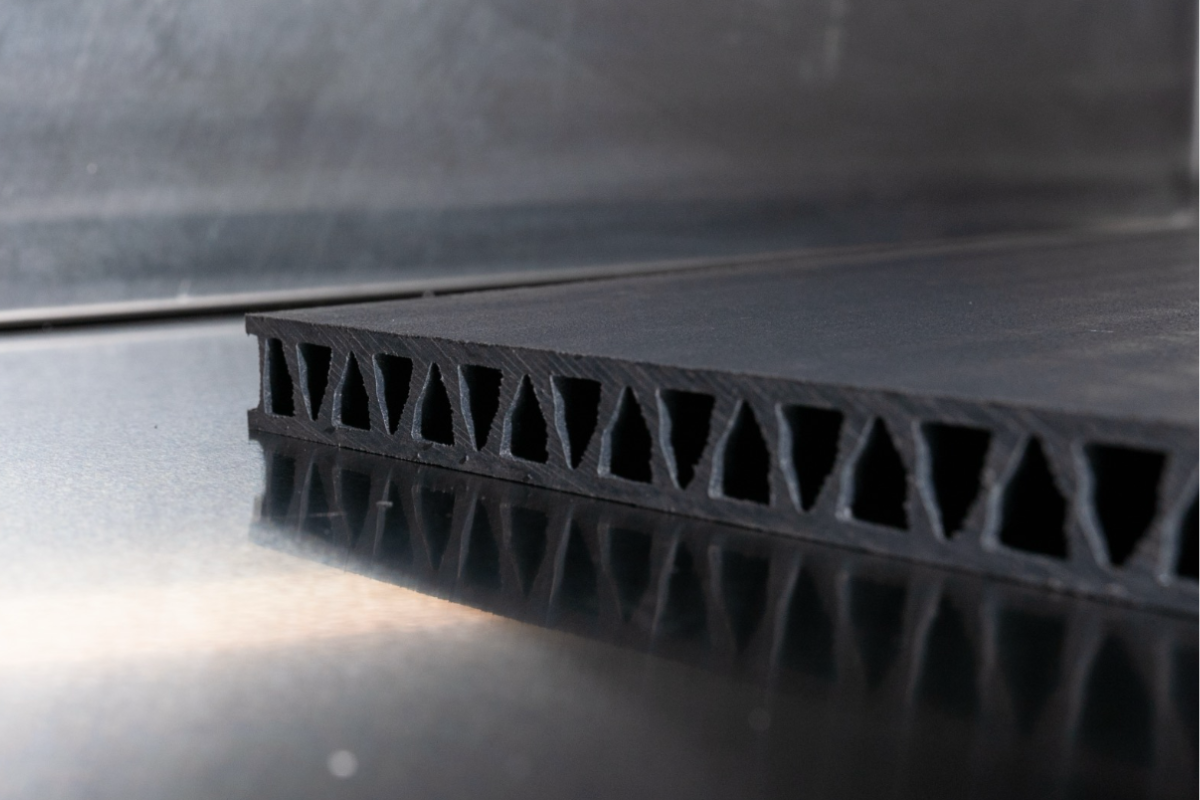
The recycled-content plastic plywood material is billed as a stronger, waterproof option to replace traditional plywood. | Photo courtesy of Supersede
Phoenix, Arizona-based Supersede started up last fall with a goal to use recycled plastic to create a plywood-alternative board specifically for marine use. The company has started with post-industrial PP as a feedstock and is experimenting with post-consumer resin as it gears up for an expansion.
Launched in October 2024, Supersede currently operates a single facility in Phoenix, sourcing post-industrial PP regionally and occasionally nationally from manufacturers, brokers and other suppliers. The company is targeting material that hasn’t yet been reprocessed, often bringing in full product scrap. At its plant, the company grinds the plastic, mixes in additives, pelletizes it and puts the pellets into an extruder. Out the back end of the extruder comes a plastic sheet of plywood-replacement board.
The company’s first facility can produce 150,000 4-by-8-foot sheets of the plywood product per year, and the company is currently developing a second facility in the Midwest with double the capacity of the first. That facility’s location has not yet been released.
By January 2026, the company has a goal to hit 25 million pounds per year of recycled plastic capacity.
“We started this business with a really altruistic view on how to make an impact, and at the end of the day, what is really resonating is it’s just a better-performing product,” said Sean Petterson, CEO of Supersede. “So we’re going to scale it based on that.”
Petterson, an entrepreneur with a background in the manufacturing sector, explained plywood has been degrading in quality in recent decades, both through changes in the types and quantities of chemicals used in the material and through the younger age of trees providing the lumber.
The idea of using thermoform plastic took hold for the material’s structural characteristics, particularly the fact that it’s 100% waterproof. It became a natural fit for marine use, where it can help avoid structural failures from rot and mold, Petterson said, which are more common with traditional plywood.
“In the process of trying to develop a means to replace it, we wanted to look at waste streams,” he said.
The company settled on a post-industrial PP sourced directly from manufacturers who generate production scrap. Post-industrial was chosen because it’s a cleaner stream of material than post-consumer, and the level of contamination within most post-consumer streams would not mesh with the marine board’s requirements.
“When we’re designing something that’s going to be a structural element, we need it to be highly specific,” he said.
Still, the company is fine-tuning its process to handle some small amounts of contamination, like what the company encounters when bringing in production scrap. Depending on the product, the PIR stream might include contaminants like clips or handles of a different polymer, for example. So the PP might have small amounts of nylon or PET mixed in. Supersede is able to manage and distribute that contamination during the regranulation process.
“We’re really focusing on finding that type of application, where we can ingest a certain level of contamination, because obviously there is a broader market for a pure, 100% PP,” he said.
Petterson noted Supersede is looking at incorporating PCR in future products beyond the current marine board, where the structural attributes might not require such stringent feedstock quality.
The company has been testing PCR, particularly using mixed plastics, Petterson said. Supersede has been testing and blending those mixed materials and then evaluating how the formulation affects the board product in test runs.
“Our goal here is to ingest as much low-melt plastic as we can, I think that’s the main thing that we need with our extrusion process,” he said.