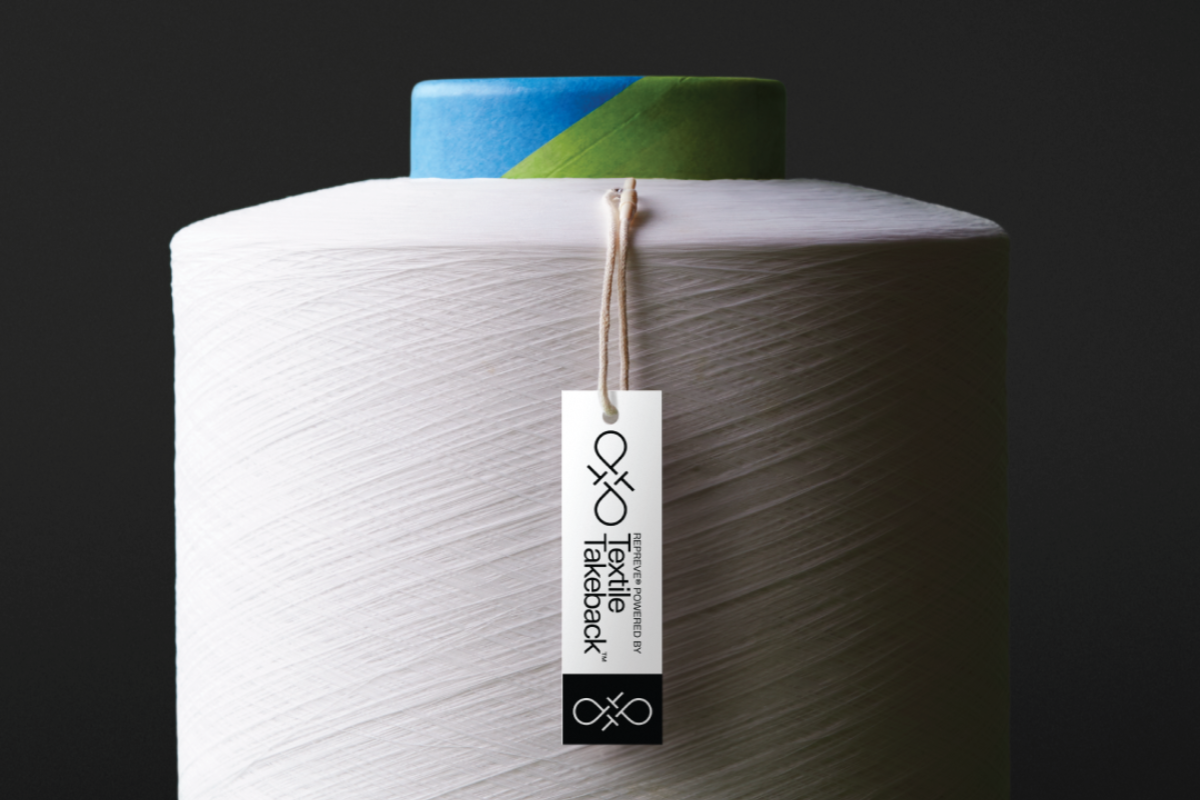
Despite gains made in recycled content, textile manufacturing faces unique challenges, a Unifi executive said during a recent APR podcast. | Photo Courtesy of Unifi
Editor’s Note: Mark your calendar for the 2026 Textile Recovery Summit, Feb. 23-25 in Chula Vista, California.
An executive from U.S. textile manufacturer Unifi explored the challenges facing textile recycling and gave a glimpse of what to expect from Unifi during a recent podcast from the Association of Plastic Recyclers.
Headquartered in North Carolina, Unifi is one of only a handful of domestic companies making textiles, and in recent years it has seen recycled PET end markets shift from carpeting and apparel uses to packaging applications requiring high-quality resin — and lots of it.
Although PET bottles are easily and frequently recycled, one significant hurdle for the industry is bringing textile-to-textile recycling to scale, in a way that’s both economically viable and globally accessible, said Meredith Boyd, executive vice president and chief product officer at Unifi. (PET is typically called polyester when referring to textile applications.)
Unifi plans to continue to invest in building a “truly circular economy and empowering that for brands, retailers and ultimately the consumer,” by seeking out more strategic partnerships and fueling innovation “to make sure it’s a reality and can be available globally at scale, and now,” Boyd said — echoing the Textile Takeback process tagline — so all erstwhile waste products can be used.
However, the infrastructure for collecting, sorting and processing textile waste has not yet reached the level of packaging waste, and this requires greater collaboration across industries, she said during the APR podcast. APR owns Resource Recycling, Inc., publisher of Plastics Recycling Update.
Looking ahead, Unifi will continue to grow in new markets, “emphasizing our ability to go into packaging materials, nonwovens applications, other areas,” Boyd said, adding that Unifi’s bottle processing facility in North Carolina opened in 2016, and produces hot-washed PET flake.
Boyd’s comments echo CEO Eddie Ingle, who said during a May 2025 investor call that he saw several promising end markets for recycled polyester and nylon, including automotive applications, home furnishings, carpet and military applications, as well as packaging, “where we sell a lot of our pre-resin,” meaning RPET flake.
Despite brand owners backing off from voluntary PCR commitments, Ingle said, “what we’re seeing is they’re not dropping their sustainability targets. They’re just trying to move them out primarily because it’s just hard to become more sustainable. And I think there’s a greater realization of that.”
In April 2024, the company received a letter of no objection (LNO) from the U.S. Food and Drug Administration for RPET use with most food temperatures, ranging from frozen storage to above 150 degrees Fahrenheit. The company’s previous LNO from 2017 was for uses limited to room temperature or below.
Using transparency, traceability to change minds
Another challenge is to shift the consumer mindset of “seeing waste not as the end but as a beginning,” Boyd said. Unifi looks to provide transparency through traceability, she said, pointing to the company’s U Trust system as one way Unifi is working to earn public trust and gain consumer buy-in to recycling processes.
Other metrics like the updated lifecycle analysis (LCA) featured in the 2024 sustainability snapshot provide further validation of the environmental benefits recycled content provides, she said. For example, Unifi’s Repreve fibers use 47-84% less energy and 48-85% fewer fossil fuels than virgin polyester, with the ThermaLoop padding on the low end and Takeback Staple Fiber at the top of those ranges.
The company also will continue to leverage the diversity of feedstocks into new products in its Repreve lineup, Boyd said, adding that she joined Unifi in 2007, as the company was shifting focus from synthetic yarn products made from polyester and nylon to the Repreve recycled platform.
Amid that transition, the initial focus was on post-industrial yarn waste, and only a small amount on post-consumer packaging, like PET bottles, she said. But in the ensuing years, the amount of post-consumer plastics that can be used to make Repreve has grown.
In its most recent sustainability snapshot, Unifi reported it had recycled 42 billion plastic bottles as of fiscal 2024, which ended June 30 of that year, and that “we anticipate meeting our 50 billion target by December 2025.”
Repreve fiber represented 32% of fiscal 2024 revenue, with a target of 50% of revenue by fiscal 2030. However, in a May 2025 investor call, Executive Chairman Al Carey said, “I wouldn’t make any promises on this, but more than 50% of our business in Central America recently has been Repreve. So this bodes well for the future.”
In March, Unifi received the first APR Recycling Technology Innovation Award for its leadership in sustainable fibers.
“What we see as our role at Unifi and through our Repreve platform is to help brands and retailers really take responsibility for the products they’re creating, for the impact of those products, and even for their own supply chain waste,” Boyd said. “And by ensuring we can recycle all of these different waste materials, we’re meeting that need with these brands and retailers.”
With that in mind, Unifi recently recognized dozens of companies as champions of sustainability for using Repreve recycled fiber, including the Billion Bottle Circle designation for Nike, Polartec, Target, Texhong and Walmart.
In the end, Unifi will continue to emphasize performance technologies, Boyd said. “It’s not just about performance or having a sustainable offering, it’s about both.”