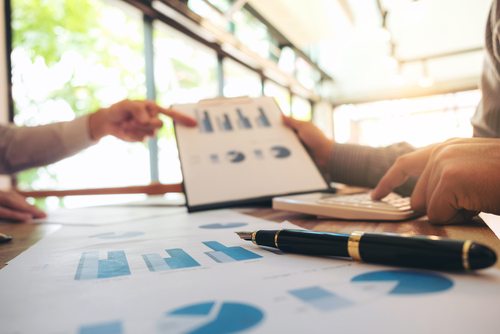
Freedomz/Shutterstock
Over the last few years, materials recovery facilities have introduced next-generation optical sorters and AI waste analytics systems to learn more about their material. As a result, their facility managers are now awash in data.
After all, U.S. recycling centers process more than 70 million tons of municipal solid waste each year. And they now have granular data on that waste – right down to its material, mass, financial value, food grade, brand and even potential emissions.
This flood of information is presenting the opportunity for a radical shift in how recycling facilities operate and optimize their processes. However, the pure amount of data can also be overwhelming for facility operators. Data is crucial, but data without any context or understanding is essentially just noise. Many facility operators who now have access to this data can feel like they are drowning in it and unable to find the needle they are looking for in the haystack.
Therefore, it’s increasingly important to know what data to look for, how to interpret it and where to apply actionable insights across facilities. While the influx of detailed waste data offers a wealth of opportunities to boost material recovery rates, maximize recyclate purity and improve operational efficiency, understanding how to leverage it for the most significant business advantage is key.
Let’s explore three strategies for turning waste data into actionable insights that drive immediate impacts on facility managers and their facilities.
Pinpointing the cause of blockages to eliminate downtime
Mechanical failures and poor process control are some of the main reasons why MRFs don’t reach optimal production capacity. Typically, these challenges lead to blockages or stoppages that result in facility downtime – and ultimately less revenue.
Data can be a powerful tool for facility managers and process engineers who are trying to reduce avoidable downtime. Continuous data monitoring allows facility managers to visualize and precisely diagnose downtime. By analyzing downtime logs, facility staff can uncover trends in material composition and throughput volume that often coincide with operational stoppages.
For example, composition data may reveal that the volume of paper often spikes before a blockage. Operators can use that insight to isolate paper-sorting machinery for inspection. This type of data-assisted, proactive maintenance is crucial in avoiding costly downtime and extending the life of machinery, ensuring that the recycling process remains efficient and uninterrupted.
Transitioning from weekly sampling to real-time purity data
Recovery facilities often struggle to maximize profits without an accurate understanding of product purity. Underestimating the true purity average of waste can prevent MRFs from selling their material at premium prices.
Unfortunately, no matter how rigorous facility operators are, manual purity sampling often falls short of providing absolute certainty. Waste stream composition can change minute-by-minute, causing the proportion of target material – and by extension, the stream’s purity – to fluctuate just as frequently.
By accessing purity data in real-time, facility managers can spot and adapt to trends faster rather than waiting on intermittent manual samples. Even a small drop in purity — from 99% to 95% — can jeopardize customer contracts. We recently saw a case where a facility faced such a drop but leveraged real-time data to resolve the issue in minutes instead of days. They ultimately saved £50,000 (about $65,000) by avoiding the need to reprocess 40 tons of aluminum cans.
Continuous monitoring also makes it possible to assess the quality of infeed material. Every recovery facility receives materials from multiple suppliers or municipalities, with each one committing to certain composition specifications. Rather than relying on hand sampling to confirm material quality, facility managers can review the whole batch coming into the facility with autonomously collected infeed data. If the quality is not up to par, an MRF can ask to be compensated for the difference in quality, seek to renegotiate contracts or even start to look for other suppliers.
Stabilizing throughput to minimize residue losses
Stabilizing the throughput volume of material not only maintains consistent product quality and reduces downtime but also minimizes the valuable resources lost to the residue line. A data spike in the volume of material is often correlated with a data spike in residue. Therefore, while it’s vital for MRFs to maximize the amount of material running through their facility, they should aim to do so at a rate that can maintain without peaks and valleys in throughput volume.
To maintain this steady line, facility managers also need to examine the different shifts in their workforce. Many large MRFs in major urban centers run 24 hours a day, requiring several different operational shifts. Segmenting data by day and night shifts can reveal whether spikes or periods of low belt usage are linked to shift changes and employee performance rather than material or equipment issues.
Of course, facility managers also need to analyze the types of materials that frequently end up in the residue line to minimize residue losses. Greyparrot data from last year indicates that 37% of global residue line material is recoverable paper and cardboard, while 26% is recyclable plastic. In one severe case, a UK-based MRF we observed discovered that only 7% of its residue line was genuinely non-recyclable, with the remaining 93% being recoverable!
The volume of plastic in particular represents a major opportunity: Materials like RPET are often in high demand. High-value residue losses make a strong business case for investing in more effective sorting technology. Data gathered pre- and post-sorting can make it clear whether there is a need to introduce machinery like robotic sorting arms to fill gaps that optical and manual sorters are missing.
After all, effective recycling isn’t just about processing as much material as possible; it’s about recovering as much recyclables and value as possible. Training staff to address these issues or investing in better sorting technology can significantly increase recovery rates, ensuring more valuable materials are diverted from landfills. Furthermore, any investment can be guided by actual waste composition data, so there is concrete evidence to support the need for any expensive infrastructure changes.
Empowering MRFs with data-driven transformations
The recent surge in data availability offers recycling facility managers a powerful tool for optimizing operations and achieving profitability goals. By using this data strategically — whether to refine sorting processes, improve recovery rates or ensure regulatory compliance — facilities can transform challenges into opportunities.
Moreover, the insights gained from data extend beyond individual facility improvements. They can inform policy decisions, drive innovation in recycling technologies and contribute to the development of a more circular economy. In other words, as the recycling industry continues to evolve, those who effectively harness data can be at the forefront of driving positive change.
Gaspard Duthilleul is the chief operating officer of Greyparrot. An engineer by training, he has steered high-stakes projects across Europe, Asia and the U.S. over the last decade. In his current role, he leads Greyparrot’s operational strategy, with a focus on scaling impact and utilizing waste analytics to drive a more sustainable approach to resources.
The views and opinions expressed are those of the authors and do not imply endorsement by Resource Recycling, Inc. If you have a subject you wish to cover in an op-ed, please send a short proposal to [email protected] for consideration.
A version of this story appeared in Resource Recycling on Sept. 4.