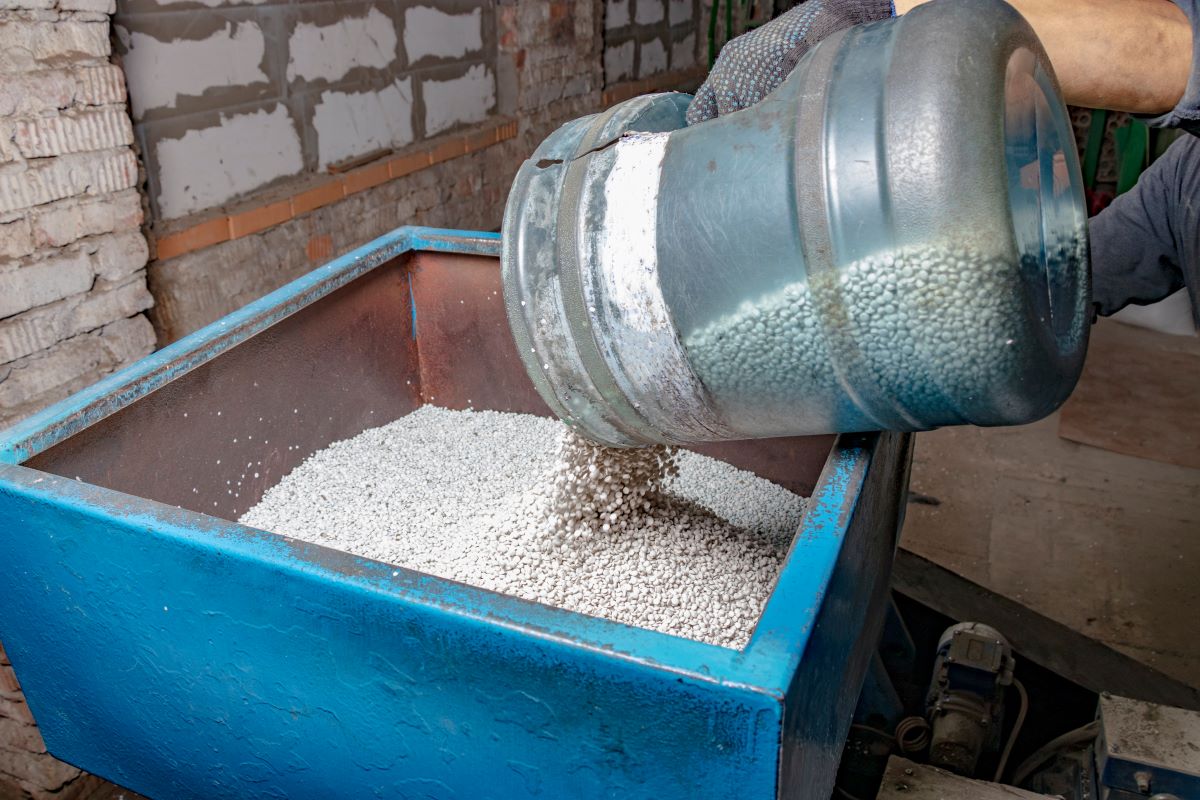
With more capacity coming online, EFS-Plastics will be able to handle more B-grade LDPE film bales and potentially transition to contractual supply arrangements. | Vikentiy Elizarov/Shutterstock
As EFS-Plastics nears completion on its third LDPE film processing line in Pennsylvania, the company is changing the way it approaches film bales, a company executive said in an interview.
The expansion in Hazleton is waiting for a new extruder to arrive due to a slight delay, said Hendrik Dullinger, vice president of business development at EFS-Plastics. But the new capacity should be fully online by the end of September and will include a series of optical sorters.
With the new capacity, EFS will be able to process more B-grade film bales containing more color film, he said, and will continue its focus on domestic sourcing. But bale quality is far from the only shifting dynamic for EFS’s procurement strategy, he added.
“Prices have been climbing for all materials, so we’re leaning into this market in more detail, trying to secure more direct sources,” Dullinger said, adding that EFS is ramping up baling capacity in pursuit of contractual arrangements.
“With the increasing use of PCR, we’re hoping we can move away from spot buying and toward long-term supply agreements,” he said.
EFS’s experience is typical in the nascent baled plastics markets, where informal handshake agreements have been the norm for 20 years or more. But as required volumes increase and become more consistent, both buyers and sellers may seek safeguards from pricing volatility and supply disruptions.
Domestic spot buying levels for A-grade bales tend to fall within a narrow range of 1-2 cents per pound. However, B-grade bale pricing tends to vary more widely, due to inconsistent quality and trust concerns. Prices may also depend on competition from export markets, particularly in Southeast Asia. But sellers have said that domestic interest in B-grade film is growing, as more processors include equipment to handle it.
Dullinger concurred, noting an increase in competition for available bales as overall domestic processing capacity expands. As a result, EFS has seen a general decline of quality in B-grade bales as haulers target commercial customers.
“More people are collecting it but need to invest more time in training,” he said. “You can see that the sources are again varying in consistency, as they get new streams in that cause decline in cross-grades.”
In theory, B-grade bales consist of about 80% clear LDPE, versus 95-99% clear LDPE film in A-grade bales, and are priced accordingly.
In Canada, C-grade bales have even been seen at negative price levels, where a MRF pays someone to haul them away. These bales can be useful in export markets, which use manual sorting to improve bale quality. Sellers have said this is a direct result of a federal plastic bag ban.
Although some legislation meant to address plastic waste and other environmental issues can depress commodity prices and actually discourage recycling by destroying demand for PCR — for example, Canada’s federal plastic bag ban – other policies lend support for EFS’s growth.
“The reason we expanded in the first place was the growing demand in the U.S. and Canada, with the first sustainability goals coming up in 2025,” Dullinger said.
Alberta facility ramp-up
An expansion at the EFS site Lethbridge site in Alberta, Canada, is expected to be operational by Q1 2025, Dullinger said, adding that equipment should land in Q4 2024.
EFS is installing a hot wash system and extruder to the 70,000-square-foot facility, which opened in early 2022 and has focused on breaking and sorting 1-7 bales, also known as mixed rigids.
“It’s been a secondary facility feeding Hazleton but now will also be mechanically recycling material into pellets on the West Coast for the first time,” he said.
The plant will produce HDPE, PP, PET thermoforms and flake, and EFS will pursue an FDA letter of no objection in the first few months after startup.
The Alberta site was one of the first sorting facilities for thermoforms, he said, and EFS prioritized thermoform recovery rates when researching equipment.
“We don’t know the integration rates yet, but we would hope to supply a quality PET thermoform that can move the needle with this Alberta system,” Dullinger added. “While we produce PET, the system is equally well equipped to process PE and PP.”
Maintaining an agile strategy
As brand owners have begun realizing their voluntary PCR targets for 2025 will remain out of reach, and focus shifts to reducing their overall carbon footprint, EFS faces a turning point in its growth strategy.
If companies are moving away from maximizing their PCR content, “does it make sense to go into food-grade applications or to shift into durable goods?” Dullinger asked. EFS has historically performed secondary processing for 1-7 bales, which go into non-food applications.
“Now everyone is shifting to sorting at the MRF level, so the question is what direction are we going,” he said. “We can certainly extend operations to food-grade. We believe in very versatile recycling operations, so if someone says what they want to do, we can shift our focus to that.”