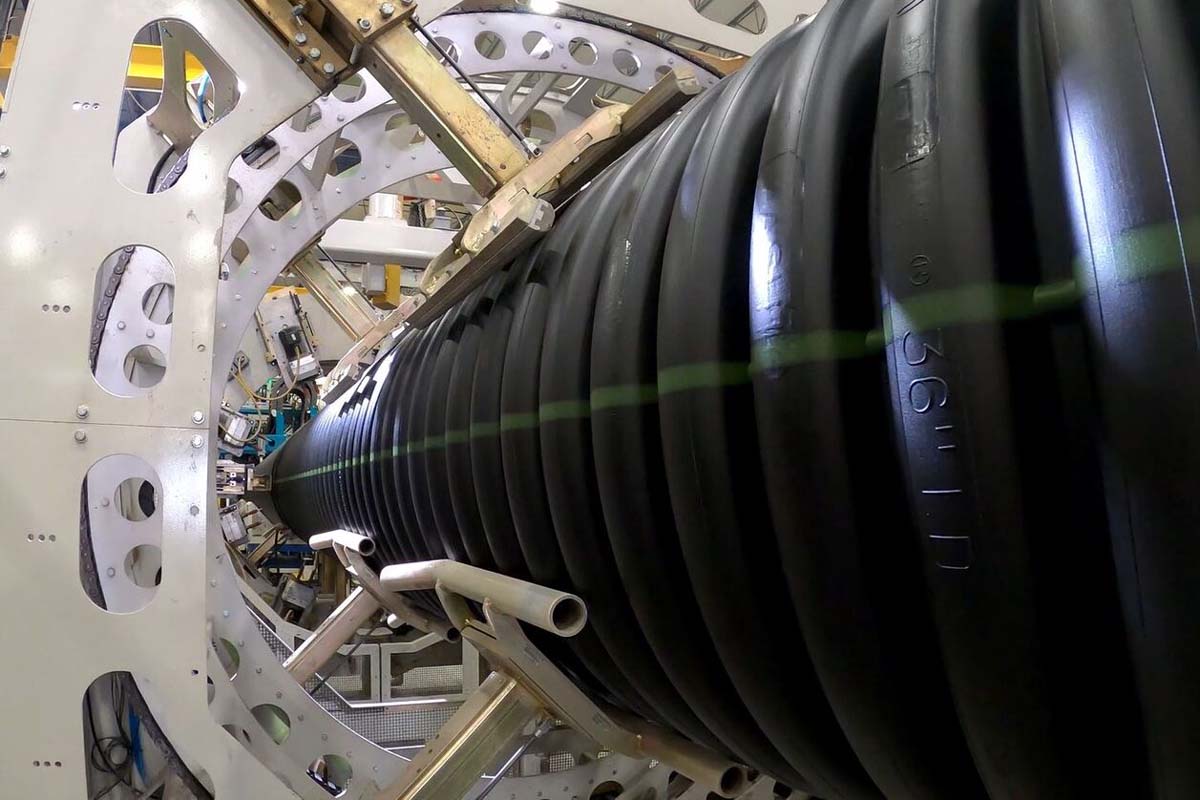
Advanced Drainage Systems expects to spend $250 million to $301 million on capital expenditures this year. | Courtesy of ADS
Several plastics reclaimers and recycled resin end users recently shared details about their operations in earnings calls. From capital project spending at ADS to chemical recycling expansions at LyondellBasell, here’s a roundup of recycling operations news.
ADS
Advanced Drainage Systems expects to spend $250 million to $301 million on capital expenditures for the full year, including debottlenecking its recycling operations and completing its engineering and technology center in Ohio, executives said during a quarterly investor call.
ADS, one of the largest plastics recycling companies in the U.S., recently hit 50% recycled resin use, and the company reported purchasing 540 million pounds of recycled plastics in its 2024 fiscal year.
Dow
Michigan-based chemical and polymer producer Dow expects to close its acquisition of mechanical recycling firm Circulus in Q3 2024, executives said during a recent quarterly earnings call. The deal includes two facilities with a combined capacity of 50,000 metric tons of recycled materials annually.
And in the second half of 2024, Dow plans to begin marketing products using offtake from both its Valoregen mechanical and Mura chemical recycling facilities, according to CEO Jim Fitterling.
LyondellBasell
Texas-based LyondellBasell still plans to shut down its only refinery – located in the Houston area – by the end of Q1 2025, and to site its second chemical recycling investment there, executives said during a recent quarterly earnings call.
The company has yet to take a final investment decision at the Houston site, but CEO Peter Vanacker said he hopes to make “a first milestone decision on that still this year.” The company’s first industrial-scale chemical recycling plant is under construction in Wesseling, Germany, with completion expected at the end of 2024. LyondellBasell previously started up a smaller pilot plant in Ferrara, Italy, in 2020.
Vanacker also said a second project on renewable hydrocarbons from such waste as used cooking oil – which, like plastics, can be broken down to the molecular level to make feedstock for virgin-quality polymers – could leverage equipment at the Houston refinery site.
PureCycle
For Q3 2024, PureCycle has shifted its focus toward increasing production and sales for its purified PP plant in Ironton, Ohio.
The company spent much of Q2 conducting planned maintenance and restarting, but aims to reach a feed rate of 10,000 pounds per hour, and production of 200,000 pounds a day and 1 million pounds a week, CEO Dustin Olson reported in a recent quarterly update.
The company is leaning into compounding as a growth strategy, and has developed relationships with multiple compounders, Olson said.
“By adding the compounding step to our operation, we should be able to accelerate the product development process for customer applications, open more market channels and should also create enhanced market economics for Ironton,” he said, adding that compounding capacity exceeds demand, which presents a good opportunity for PureCycle.
As the Ironton plant gains reliability – “it’s not perfect yet,” Olson said – PureCycle will be able to work with the compounders to customize resin to suit client needs.
“You have to make it easier for the customer to buy your materials, and that’s what compounding does,” he said, adding that compounding enables customers to get the desired mix of recycled content, whether 10% or 100%.
In June, PureCycle’s PureFive resin received an expanded Letter of No Objection from the U.S. Food and Drug Administration. The LNO allows the company to employ a wider range of feedstock for FDA applications, including curbside materials that are sorted for food-grade.
With the expanded feedstock slate, Olson said PureCycle is working to find the right balance between insourcing and outsourcing, which becomes a question of allocating capital versus incurring an expense.
Using third-party operators to sort bales to 95% PP costs 14-20 cents per pound on average, and implementing PureCycle-owned flake sortation to 97% PP costs an average of 12-15 cents per pound, according to a company presentation.