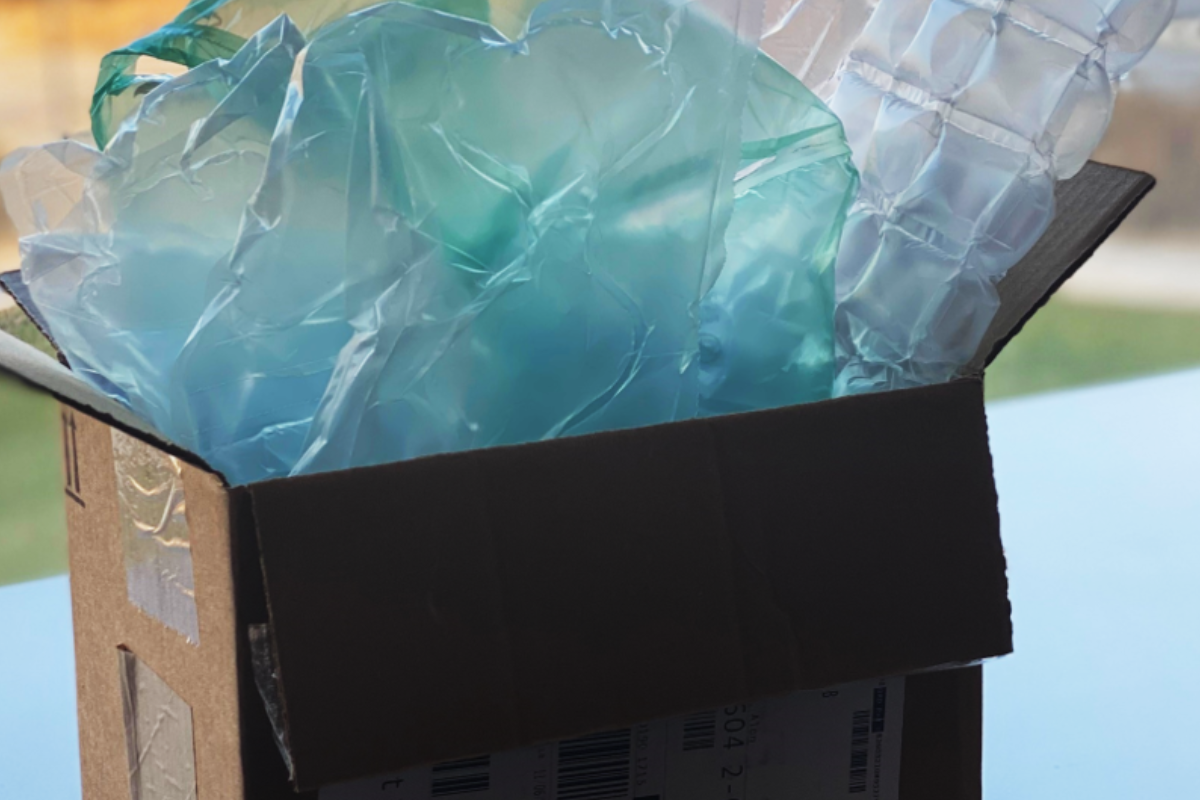
Aeternal Upcycling’s hydrogenolysis technology originates from work that co-founder Ryan Hackler conducted at the Argonne National Laboratory. | Courtesy of Aeternal Upcycling
When Ryan Hackler was 8 years old, the Olympic Pipeline exploded in a park not far from where he lived in Bellingham, Wash., killing three young people and devastating about 26 acres near the heart of the city.
The 1999 incident led him in later years to ponder the juxtaposition between the necessity of petrochemicals in society versus the environmental issues they present. Hackler said it drove his fascination with using chemistry as a means to create positive change.
Today, Hackler is co-founder and CEO of a startup company that’s aiming to use chemistry to recycle post-consumer plastics into valuable wax and oil products that represent a fraction of the greenhouse gas emissions that their virgin counterparts do. His company, Aeternal Upcycling, has recently received some major financial support.
Most recently, the U.S. Department of Energy announced that his company will receive $1.5 million to establish a pilot plant. The grant was one of several plastic-related grants awarded by the Reducing Embodied Energy and Decreasing Emissions (REMADE) Institute.
Earlier this month, Aeternal was one of 10 startups selected to join mHUB, a technology business accelerator program in Chicago. Aeternal was specifically selected to participate in its six-month 2024 Climate and Energy Tech Accelerator. According to a press release, his company received $105,000 in cash investment.
Additionally, Aeternal recently received the 2023 Nicor Gas Multicultural Innovator Award, which is provided through a partnership of Evergreen Climate Innovations, a nonprofit investment fund supporting upcoming technologies that benefit the climate, and Nicor Gas, a natural gas supplier that’s a subsidiary of Southern Company Gas. That award included a $25,000 equity and inclusion grant, which goes to startups with minority founders or CEOs (Hackler is Latino), as well as 12 months of mentorship and connections with investors and customers across the Evergreen Climate Innovations and Nicor Gas networks, according to a press release.
Lubricants with less carbon footprint
Based in Chicago, Aeternal Upcycling’s hydrogenolysis technology stems from work Hackler did while he was a postdoctoral researcher at Argonne National Laboratory, a U.S. Department of Energy-owned lab in the Chicago area. Last year, Hackler joined a two-year fellowship program at Argonne called Chain Reaction Innovations, which is intended to help entrepreneurs commercialize clean energy technologies.
Also last year, he and Robert Kennedy, who also studied at Argonne and Northwestern University, founded Aeternal Upcycling to further develop and commercialize the technology.
The hydrogenolysis process works by putting shredded or pelletized plastic into a reactor with hydrogen gas and a platinum-base catalyst. The outputs consist of waxes, lubricant base molecules and jet fuels, he said.
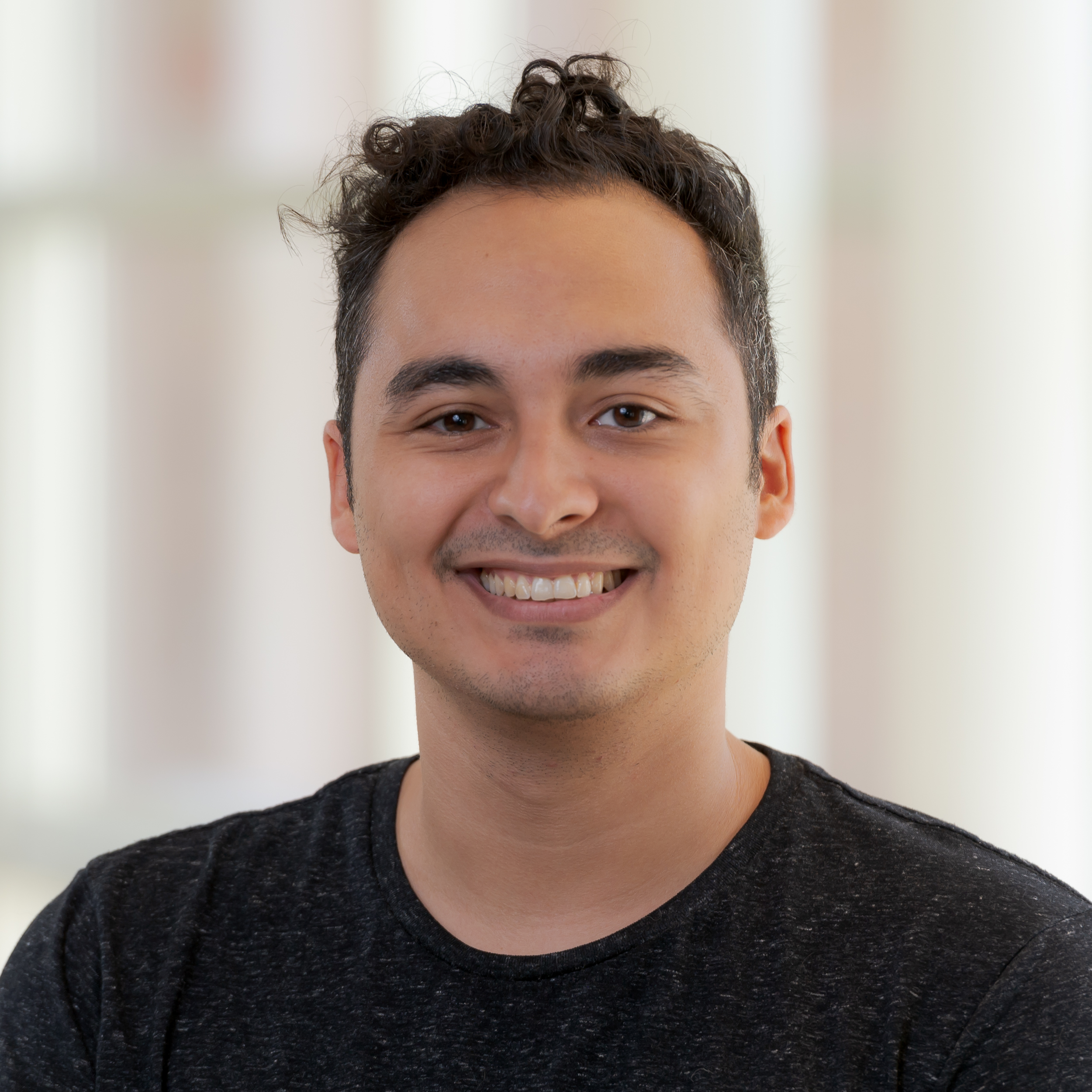
Ryan Hackler
The process is similar to pyrolysis but different in a few ways, Hackler explained. For example, it operates at lower temperatures than pyrolysis, and it doesn’t fully depolymerize the plastics. And the hydrogenolysis process has higher selectivity, meaning it generates more product and less unwanted byproducts, such as gases.
He said that, in the best-case scenario in which the feedstock plastic has no fillers, hydrogenolysis can reliably produce 80% or higher conversion to product, with the remainder being light gases such as methane, ethane, propane, butane and others.
In terms of waxes, Aeternal is aiming to produce food-safe coatings, candle waxes and cosmetic waxes. Another end product is lubricants to replace Group 3 and Group 4 mineral oils used in machinery such as engines, wind turbines and electric vehicles, he said. A life cycle analysis has shown Aeternal produces about 0.25 kilograms of carbon dioxide to produce 1 kilogram of its oil, compared to 1 kilogram of CO2 for 1 kilogram of Group 3 mineral oil and 2.2 kilograms to produce 1 kilogram of Group 4 synthetic oils.
Growing the business
Hackler said Argonne National Laboratory also ran an analysis of the economic viability of commercializing the technology. It found that, extrapolating the current lab scale up to commercial scale, the technology could bring a cost of about $600 per ton of product manufactured, he said. That number is for plastic-derived chemicals, regardless of whether it’s waxes or lubricant oils.
The end products have a value of anywhere from $1,500 to $4,000 per ton, with the lower end representing the market price for paraffin wax and the upper range representing high-end synthetic oils and other specialized chemicals.
“It’s really convenient for us that there’s a significant margin,” he said.
The company currently consists of just Hackler and Kennedy, but they hope to start hiring employees in 2024. In January, they’ll open up for pre-seed fundraising, Hackler said.
The $25,000 award will help the company develop, including by building out the system engineering and protecting the intellectual property the two have developed since their Argonne days. They’re also in early discussions to license the IP developed – and thus owned by – Argonne National Lab.