This article originally appeared in the Fall 2018 issue of Plastics Recycling Update. Subscribe today for access to all print content.
Agricultural plastics have long been low in the ranks of desired material for plastics recycling operators.
Given their mission, ag plastics are of course dirty, and the mulch films used for row-crop field production are perhaps the dirtiest. Yet the use of this plastic in agriculture is growing because mulch films save water, increase harvest yield and reduce the amount of herbicides used in vegetable and fruit production.
As the number of farms using “plasticulture” increases, so does the number of farmers hoping to find a better option than disposing of this material in the landfill. Can they be recycled? Yes. Is it easy? No. But if we truly want to achieve a system where raw materials aren’t just used once and thrown away, we need to explore how recycling challenges, such as ag plastics recovery, can be cost-effectively addressed.
Pulling film from the fields
Waste Reduction Partners (WRP) in North Carolina is one of many groups trying to find a better end-of-life solution for agricultural mulch films. WRP is a government technical assistance program that recruits retired engineers and scientists to help North Carolina businesses with waste reduction strategies.
In 2011, the North Carolina Department of Agriculture and the North Carolina Department of Environmental Quality tasked WRP with finding better options to recycle agricultural plastics in the state. A number of North Carolina plastic recyclers were already processing nursery pots, trays and flats, which has allowed WRP to link nurseries in the state with recycling solutions fairly easily.
It has been harder to develop materials diversion options for vegetable and fruit farmers. Recycling mulch film from vegetable production is a difficult undertaking in large part due to the fact that dirt can make up 50 percent (by weight) of a material load. Nevertheless, progress on this material is critical. If a solution can be found for mulch film, other agricultural films, such as bale wraps, silage covers, and greenhouse films, can use the same methods and processes. And non-agricultural film products, such as boat and RV covers, will also follow suit.
During 2017, the researchers involved in WRP’s ag plastics project were focused on farm mulch retrieval methods. WRP received a grant from the North Carolina Tobacco Trust Fund to evaluate equipment that could pull mulch film from the field in a cleaner, more efficient manner. The project evaluated three mulch film retrieval equipment models (of the eight known to be in the market).
The team ran trials at three different farms that had grown tomatoes, peppers and pumpkins. Methods were developed to reduce or eliminate the entrapment of vegetation and soil in the retrieved bundle of plastic. Industrial engineering techniques were used to record time and manpower, and the results were then incorporated into costing formulas and calculations that compared the use of machinery with the use of manual labor.
The project showed substantial reductions in time and expense for the farmers when lifting machines were utilized. The research showed that farmers saved about $125 per acre per year using appropriate equipment and processes.
The team also evaluated compaction equipment that could be used in the field. A tractor-mounted baler was trialed, and although it worked well, the team hopes to evaluate a trailer-mounted baler that is readily moveable from farm to farm.
From mulch back to usable plastics
The retrieved mulch films from the 2017 trials were then used to better understand techniques, processes and equipment that could be used for recycling the plastic.
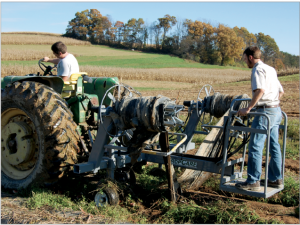
By utilizing film-lifting equipment, farmers can save $125 per year per acre in labor and other costs.
Shredding is the obvious first step, and a single-shaft machine with large screen openings worked well for that operation. Representatives from shredding equipment manufacturer Weima America helped in selecting the correct machine configuration and running trials. The tests succeeded in producing a cleaner product even at this early stage. For example, an evaluation by the Polymers Center of Excellence in Charlotte, N.C. showed a 7 percent reduction of ash content just from shredding alone (when compared with film evaluated direct from the farm).
The next processing step to consider was washing. Typically, dirty plastics are sent to a wash tank for cleaning. However, with an initial dirt contamination rate of 40 to 50 percent, the plastics in question would have created water so dirty it could not be discharged to a sewer or streams. To address this, a recycler would need to invest in very costly waste water treatment capability, and that added expense would greatly reduce the profitability of the recovery operation.
The project team was approached by Broadview Group International, which has developed a dry impact machine for cleaning carpet plastic fibers and has a capacity of 4,000 pounds pounds per hour. The shredded material was sent through this device and the resultant plastic flakes were shown to have 5.5 percent ash using the ASTM tests utilized by the Polymers Center of Excellence. Similar test results were found on trials run on a dry process machine from Milner Engineering. (Both machines required dust control to prevent the settling of dirt back onto film pieces.)
At this stage, the relatively clean plastic flakes displayed the following characteristics:
- Loose and light – not flowable by gravity, but conveyable by pneumatic systems.
- Not dense enough for cost-effective transport from location to location.
- About 5 to 6 percent ash, which may not be low enough to be recycled into some end products but perhaps suitable for others.
The flakes could be further processed by a wet wash process, such as in a wet friction washer. This type of wash, based on our simulation and research, would likely reduce the ash content to the 3 to 4 percent range. This step introduces water, but the lightly contaminated waste water may be discharged into the sewer in most jurisdictions, and therefore it is a much less costly endeavor than using a wet-wash system at the beginning of the cleaning process. At the final stages, the water should be removed prior to any further process that requires a dryer in the process line.
It’s also worth mentioning that some processors investigating mulch film recycling have expressed concern about barrel and screw wear due to the granular nature of dirt particles. Theoretically, large bore extruders have wider barrel/screw clearances and may be less affected by this material. This has not been studied by WRP.
Another common question: What happens to the removed dirt? It can be returned to the fields, sent to the nursery trade or be used as daily cover at a landfill.
Further processing and finding markets
The WRP team experimented with several methods of densifying and further purifying the material.
The first trial used a film reclaiming extruder/pelletizer (the piece of equipment was an NGR shredder, feeder, extruder and pelletizer combination) with a screen filter and single vent.
The flakes processed well with no surprise except for a smell of burning wood attributed to vegetation not being totally removed in prior operations.
This finding amplifies the need to work with farms to remove all vegetation from the film in the retrieval process and suggests that a wet wash may be required, depending on end-product applications. The run was too short to plug the filters.
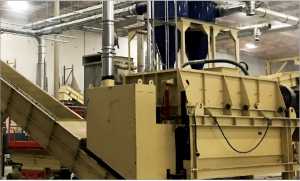
The use of a dry impact separator can reduce dirt levels in recovered ag plastics without water.
These pellets were tested, and no improvement was found in ash test results. A more dense screen pack or more advanced filter system was not tried.
The pellets were distributed to various organizations to gather feedback.
The crew also trialed an agglomerator from MGB, which densifies the material to make it flowable and reduces transportation cost. A densifier or agglomerator heats the material only to the softening point, thereby adding little heat history to the material. The volume reduction was about 6:1 and provided material acceptable to one molder of structural plastic blocks.
This process affords low upfront costs but is dependent upon operator skill for efficiency and quality performance. Additionally, this process did not change the results of the ash test.
More automated agglomerators intended for volume production are available from European suppliers, but the team did not trial those other equipment options. Presumably, that machinery would produce material that has suitable cleanliness for certain applications, similar to the results of our trials.
That all brings us to the final step needed for processing success: connecting with markets. Most readers of this publication know the pricing, logistical and export challenges in the current plastic recycling market.
When WRP researchers started this project, they expected to be able to produce a commodity material priced in the range of $0.25 to $0.33 per pound. However, at the time of this writing in October 2018, the market price is about $0.18 to $0.20 per pound, or perhaps even lower.
The team has developed a cost model with help from several equipment suppliers and recyclers, and it includes assumptions for freight rates, capital costs, depreciation, maintenance costs, utilities, labor and related costs, plus admin costs. It shows that the process described in this article comes at a cost of about $0.16 to $0.18 per pound. Thus, for a recycled commodity resin marketer, this is not a profitable venture, given current material values.
Nonetheless, the hope is that firms who produce end products with high recycled content or businesses that are vertically integrated in agricultural sector markets may find this process cost-effective. As markets shift, the system could also be profitable for other stakeholders.
Some questions remain
This project has demonstrated successful strategies for lifting agricultural mulch film from the field in a cleaner manner, shredding it during intermediate processing, and further processing it via dry cleaning methods. At this point, we can offer several recommendations.
At the farm level, it is technically and economically feasible to recycle ag mulch and other LDPE films with the right farm equipment and procedures (a more complete discussion of the farm activities is available at the North Carolina Agricultural Recycling Program website, ncagplastics.org). The big challenge here is to get more farmers to invest in mulch retrieval implements and employ best practices for film retrieval. Also, the industry needs to develop an effective collection system to move the films from farm to recycling facility.
For reprocessors, the key to cleaning these films is a dry impact separator, a machine newly introduced and derived from the carpet fiber recycling process. This unit reduces the dirt levels substantially early in the process and eliminates the high capital and operating cost of cleaning the waste water from older wet cleaning processes. All the other equipment used in the trials is well known within the recycling industry.
Nonetheless, challenges still exist, especially in terms of transportation from the field and end markets for processed material. As WRP continues this project this year, it plans to focus on three areas.
First, it’s critical to convince more farmers to use properly engineered retrieval equipment. Second, WRP will look to develop a model collection network to connect farms to recyclers. Finally, the team will be working to find product manufacturers that can benefit from using recycled ag films and help them set up a supply chain.
Those interested in this project can contact the author at the email listed in the bio below. We welcome your input.
Dave Lowles is a retired engineer with various management experiences in several industries, including managing extrusion operations for a large multinational corporation. He now serves as a consultant with Waste Reduction Partners and can be contacted at [email protected].