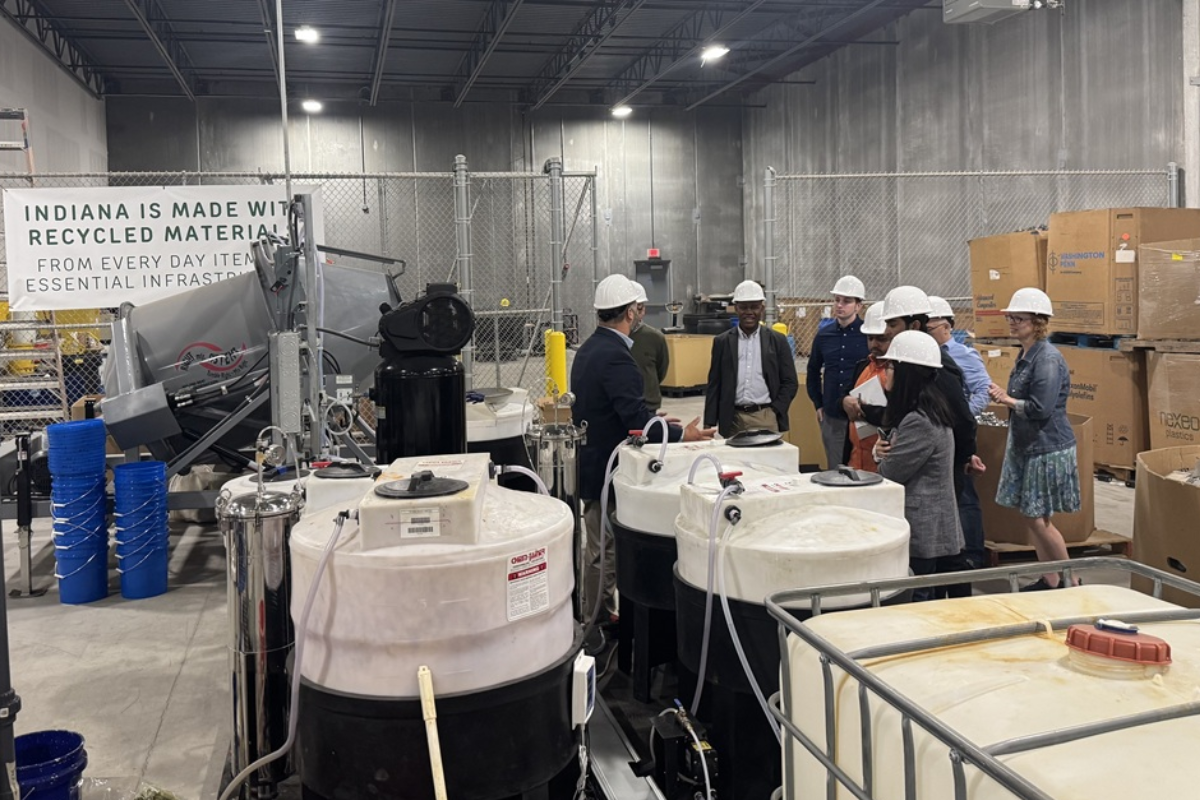
Project stakeholders tour RecycleForce in May, observing an on-site rare earth recovery system built around acid-free dissolution technology. | Photo courtesy RecycleForce
Editor’s Note: Learn more in person – RecycleForce and Ames National Lab will speak about the rare earth recovery project during a plenary session at the 2025 E-Scrap Conference, set for Oct. 27-29 in Grapevine, Texas.
A pilot project is demonstrating a bolt-on modular system that could make it logistically and economically feasible for e-scrap processors to recover rare earth elements from end-of-life electronics within their existing facilities.
The project involves numerous stakeholders and multiple sources of grant funding, and has resulted in a system being installed on-site at Indianapolis e-scrap processor RecycleForce’s facility. Shredded hard drives are being put into an acid-free copper-based solution that chemically dissolves the small amount of rare earths from the shredded magnet fraction, while leaving the rest of the metals and plastic intact for typical commodity recovery.
The resulting rare earth fraction is in a form that is ready to be sent to a refinery to produce manufacturing-ready rare earth raw materials.
In an interview with E-Scrap News, Ikenna Nlebedim, a scientist at Iowa’s Ames National Laboratory and a lead researcher on the project, said this is “the only technology I know that would work in an e-scrap facility,” for a few reasons.
Most importantly from an electronics processor perspective, it allows for rare earth recovery from the shredded device stream, meaning recovery is possible from hard drives even when clients require physical destruction due to data security concerns. Most rare earth recovery efforts targeting electronics involve manually separating the magnet from the hard drive before processing it, which can be labor intensive and hard to pencil out economically.
“We can actually take the shredded (materials), put them in a copper solution, and the solution will selectively dissolve the magnet that contains the rare earth,” Nlebedim said. “The aluminum will not be dissolved. The copper is not going to be dissolved. The plastics will not be dissolved. So now you have the rare earth in a solution.”
Daniel Rowe, executive director of recycling at RecycleForce, explained the system is housed in a 30-by-30-foot space in the nonprofit e-scrap processor’s Indianapolis facility.
First, hard drives are shredded and the aluminum is separated out. Then, RecycleForce puts the ferrous fraction, which includes the rare earth elements, into what is akin to a large cement mixing machine, where it’s mixed with the copper solution. The mixer agitates the ferrous mixture and puts it through a series of pumps and filters, and over about four hours, the copper solution pulls out all of the rare earth material.
The result is a green substance — Rowe describes it as looking something like matcha — that RecycleForce can then send off for refining. Generating such a concentrated stream of rare earth materials improves the logistics significantly, he explained.
“So rather than sending 4,000 pounds of hard drives, we’re only sending 40 pounds of the rare earth concentrate oxide,” Rowe said.
The project was kicked off by a 2022 grant award from the U.S. Department of Energy (DOE), through its Office of Energy Efficiency and Renewable Energy. Titled “Infrastructure for Midwest Regional E-waste Circularity,” the project drew $3 million and fit into DOE’s “secure and sustainable materials” topic of focus for that grant round. Other project partners include TdVib, Terves, Current Chemicals and the University of Arizona.
Rare earth recovery “will take place on a modular process skid (MPS), a self-contained and portable system that will be deployed at the site of e-waste destruction,” DOE wrote in awarding the funds. “One key innovation of this project is that the e-waste treatment process will take place entirely on the MPS unit, thus eliminating the cost, emissions, and hazard of large-scale e-waste shipping.”
The technology was developed at the national laboratory and Critical Materials Innovation Hub, and is currently licensed to Critical Materials Recycling, a company that is working to advance the technology at commercial scale.
Early this year, Critical Materials Recycling was awarded funds and technical assistance through DOE’s Electronics Scrap Recycling Advancement Prize (E-SCRAP) to support the technology.
“The ability to recover value from the REEs enables a circular supply chain for all materials that have previously been economically unfeasible to recover from these feedstocks,” the company wrote in its grant application.
Technology uses simple chemistry concept
Ames National Laboratory’s Critical Materials Innovation Hub, formerly the Critical Materials Institute, has been focused on rare earth recovery for well over a decade, Nlebedim said. The organization has explored how the U.S. can diversify its supply of rare earths and do so economically, and whether the country can substitute other materials to reduce reliance on the minerals. It became a focus long before the current wider attention on securing domestic sources of rare earths amid international trade strife.
Recovering the minerals from recycled electronics fits squarely into that first area of study, which led Nlebedim to experiment with the technology now in place at RecycleForce.
“The technology is called the acid-free dissolution recycling (ADR) technology,” Nlebedim said, explaining that the motivation behind it is right there in its name: “It was really a decision to eliminate the use of acid from the solution of rare earth elements prior to recycling.”
The lack of acid turns out to be a crucial detail when considering on-site processing within an e-scrap facility. For one, acid leaching would generate acid-contaminated waste, which then has to be dealt with in some way. It also presents logistical challenges, setting up a space for acid dissolving to take place alongside a shredding line.
“Acids bring in some difficulty when it comes to operational safety,” Nlebedim said. “What we’ve installed right now seamlessly in RecycleForce’s facility would be nearly impossible if they were going to use acid.”
The inspiration for the acid-free process comes from what is a common chemistry class experiment: A nail is placed into a copper solution, and the nail starts to dissolve, extracting pure copper metal through the chemical reaction.
Nlebedim says the ADR process uses the same concept on rare earth magnets.
“Consider the magnet replacing the nail — you put the magnet in a copper solution, the magnet goes into the solution, copper comes out,” he said.
The rare earths are contained within what Nlebedim terms a “rare earth oxalate,” while other metal and plastic commodities are not affected by the solution.
Under the DOE-funded project, the oxalate from RecycleForce is being sent to Critical Materials Recycling, the company licensing the technology, which is purifying it to commercial grade. That involves heating the oxalate up to 800-900 degrees Celsius in a furnace, resulting in a market-grade rare earth oxide.
The DOE-funded project runs until December this year, and the stakeholders are already looking at the next step. Part of that is analyzing where it makes sense logistically around the country to set up refining capacity, Nlebedim noted. And Rowe, of RecycleForce, said the stakeholders are already thinking beyond hard drives.
“We’re beginning to look at other streams outside of hard drives that contain these rare earth magnets that we would be able to run through the solution and recover as well,” he said, giving examples such as electric scooter motors, power tools, and other streams that may be more plentiful than hard drives.