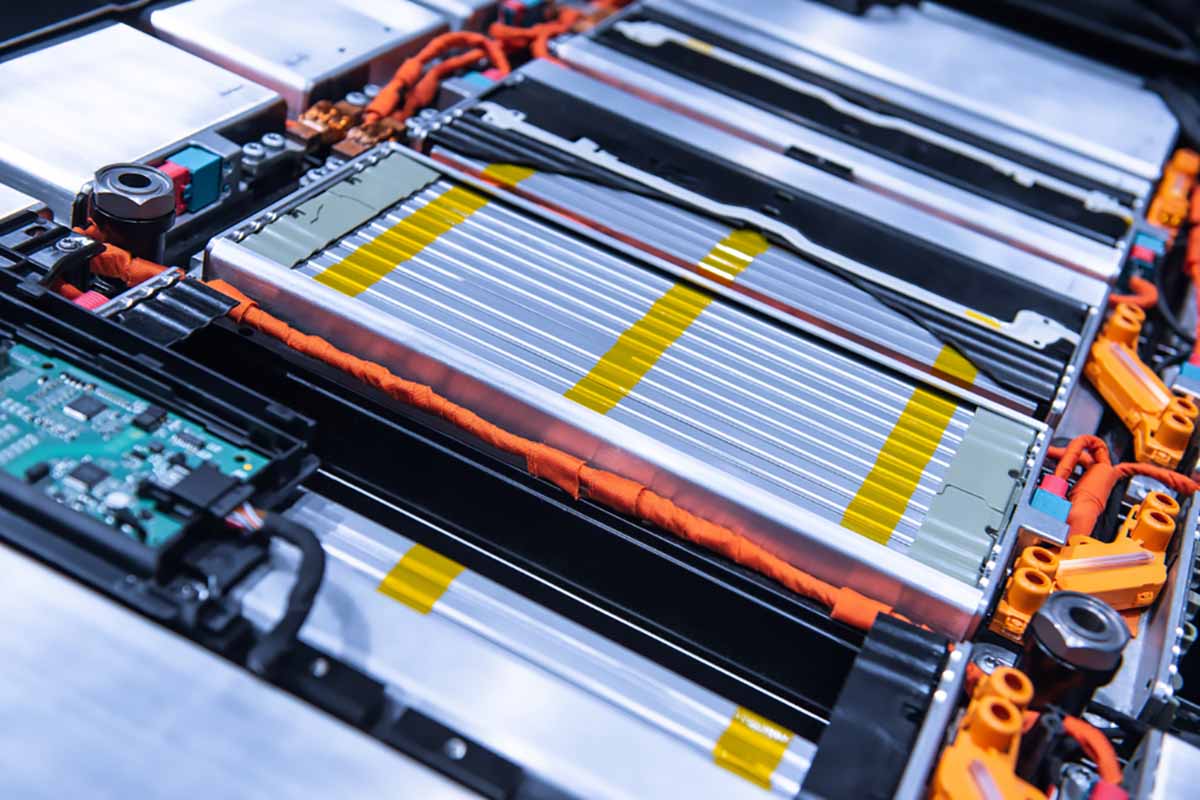
Kyle D’Silva, director of clean energy for analytical instruments at Thermo Fisher Scientific, highlights new technologies the battery recycling sector could benefit from. | Sergii Chernov/Shutterstock
The global demand for lithium-ion batteries is growing exponentially, fueled by the rise of electric vehicles, consumer electronics and renewable energy storage solutions, meaning recycling systems need to employ new technologies to keep pace.
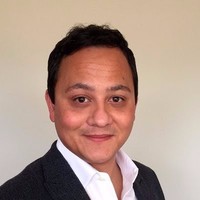
Kyle D’Silva
According to the International Energy Agency, demand for critical battery minerals like lithium, cobalt and nickel could increase by more than 40 times over the next two decades, putting immense pressure on resource availability. Recycling lithium-ion batteries has become an economic and supply chain necessity to reduce environmental impact and lessen dependence on newly mined materials, and in 2022, the U.S.collected nearly 8 million pounds of batteries for recycling, including a record three million pounds of lithium-ion batteries, yet the recycling process remains complex and inefficient.
Lithium-ion batteries are complex structures composed of multiple cathode chemistries, anodes, electrolytes, separators and metal casings, making recycling far more complicated than traditional lead-acid batteries. One of the biggest challenges in battery recycling is accurately identifying and sorting valuable materials, such as lithium and cobalt, inside the batteries. Many recycling methods fail to accurately differentiate between battery types, leading to cross-contamination and inefficient material recovery.
One of the biggest obstacles in lithium-ion battery recycling is the complexity of battery chemistries. Lithium-ion battery recycling involves breaking down used batteries into black mass, a mixture of valuable metals that requires precise sorting and processing to maximize recovery rates. High scrap rates highlight the need for better material identification to maximize the reuse of critical elements.
Governments and regulatory bodies, particularly in the EU and the U.S., are pushing for stricter recycling targets, with some policies requiring manufacturers to recover a certain percentage of battery materials. Without effective recycling, massive amounts of depleted batteries could end up in landfills, leading to significant environmental and economic losses.
Technology advancements for battery recycling
Handheld X-ray fluorescence (XRF) analyzers provide instant elemental analysis, allowing recyclers to sort spent battery materials more accurately and efficiently. This technology offers a non-destructive analytical technique used to determine the elemental composition of materials, preventing contamination and safety hazards that can arise from misidentifying lithium-ion chemistries during recycling.
By detecting the precise chemical composition of black mass, XRF technology allows recyclers to select adequate recycling processes and optimize the recovery of cobalt, nickel, copper, aluminum and iron from used batteries.
In addition to battery recycling, XRF technology plays a critical role in scrap metal recycling. Scrap metal recyclers use handheld XRF analyzers to verify elements of interest in various metal alloys, ranging from trace levels to commercially pure metals. These tools can distinguish between alloy grades with similar compositions, ensuring accurate identification and efficient recycling. This level of precision helps maintain the integrity of recycled metals, supports regulatory compliance and maximizes profitability for scrap operations.
As a complementary technology, Raman spectroscopy provides detailed chemical characterization, enabling rapid, in-process monitoring that enhances the recovery of high-value metals. By analyzing the scattered light from laser-illuminated samples, it excels at identifying and quantifying materials, monitoring process dynamics – such as the removal of electrolytes and solvents – and assessing the quality of recovered elements. This technique is particularly effective at enhancing the efficiency and yield of recycling critical materials like cobalt, lithium and manganese from cathode active materials.
Raman spectroscopy is highly effective in detecting metal oxides, sulphates, phosphates, and carbonates, providing immediate insights into reaction progress. Real-time feedback from Raman spectroscopy allows for better control over chemical reactions, leading to higher recovery rates and reduced waste.
Integrating these advanced analytical techniques into recycling workflows improves material recovery rates, improves process efficiency and supports a more sustainable and economically viable battery lifecycle.
As battery demand grows, recycling must become not just a secondary option, but a primary strategy for securing battery materials and reducing waste amid the push for electrification. XRF and Raman spectroscopy are complementary technologies addressing long-standing challenges by improving end-of-life material identification and recovery rates.
With a continued investment in innovative recycling solutions, the industry can help secure critical resources, support circular economic initiatives and reduce the environmental impact of lithium-ion batteries.
Kyle D’Silva, director of clean energy for analytical instruments at equipment supplier Thermo Fisher Scientific, is an analytical chemist with expertise in spectroscopy, chromatography and mass. He is responsible for the strategic and market development of analytical instrument portfolios that serve battery, solar, carbon storage, biofuels and hydrogen end markets.
The views and opinions expressed are those of the author and do not imply endorsement by Resource Recycling, Inc. If you have a subject you wish to cover in an op-ed, please send a short proposal to [email protected] for consideration.