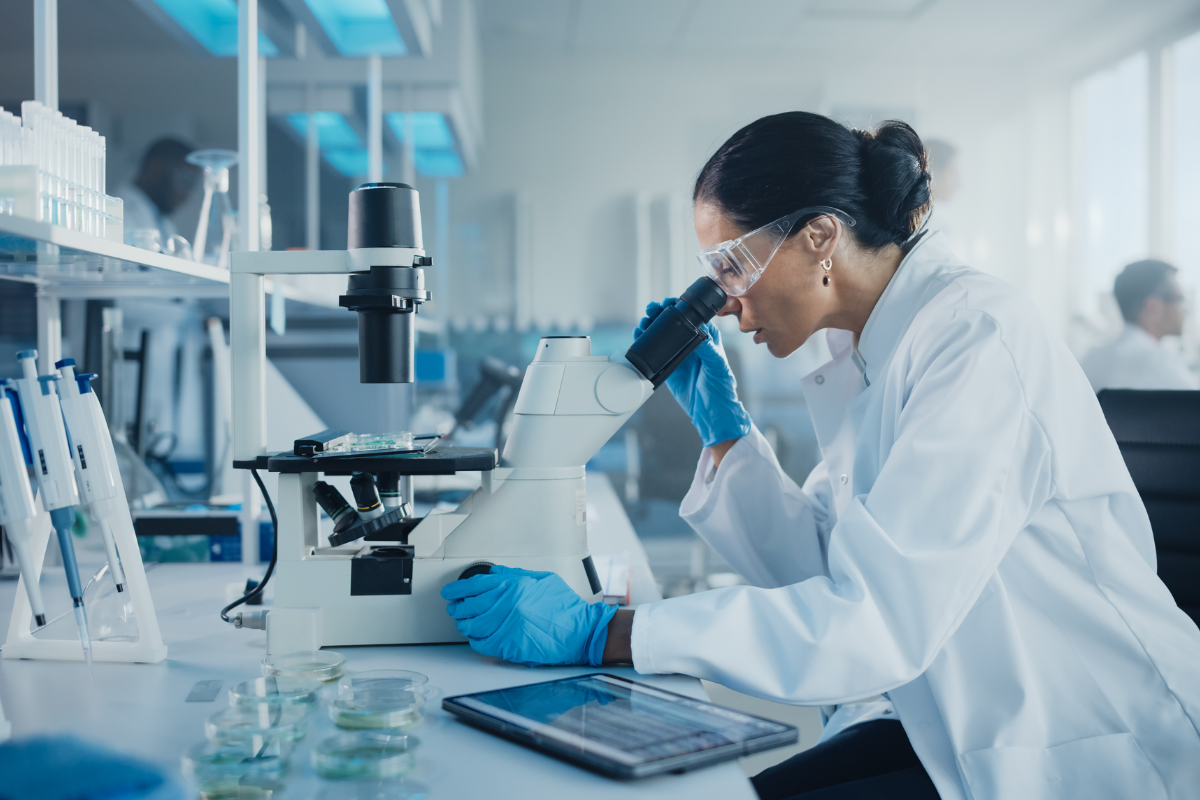
In the collaboration between multiple Austrian research universities, researchers tested a two-stage bacterial process for recovering both common metals and rare earths from the shredded e-scrap stream. | Gorodenkoff/Shutterstock
A team of Austrian researchers have developed what they describe as a “cost-effective” and non-polluting method to recover rare earth metals from electronics, and so far, they’ve achieved recovery rates of up to 85% from the e-scrap stream.
In the collaboration between multiple Austrian research universities, researchers tested a two-stage bacterial process for recovering both common metals and rare earths from the shredded e-scrap stream.
They found that the acids produced by specific microorganisms are able to leach iron, copper, aluminum and other metals from the stream, and that with these metals leached out, separate bacteria draw in the remaining rare earth metals through a process called “bio-accumulation.” Without the first stage, the common metals interfere with this process of accumulation, so both steps are needed for rare earth recovery.
The specific bacterium used in the rare earth recovery stage may unpleasantly ring a bell: Escherichia coli, better known as e-coli, was found to be the “most successful accumulator of rare earths,” the researchers noted. E-coli is also a well-known intestinal bacterium often implicated in foodborne illness.
They suggested several benefits to their bacterial approach over the current standard practices.
“The methods currently used to extract rare earths are based on chemical processes, which are associated with the formation of environmentally harmful by-products and the creation of new problematic substances,” the university stated in summarizing the results. “A combination of biotechnological methods has clear advantages over chemical methods, as both the leaching and the accumulation in the cells of the bacteria are environmentally friendly and sustainable, and no hazardous or polluting substances are produced at any stage of the process.”
They added a caveat, that the process needs to be refined to be able to handle the typical varying concentrations of different metals in the e-scrap stream. This is the current area of research, they added, with a goal of making the process “reproducible and reliable” with any inbound ratio of metals.
The research was conducted by the University of Natural resources and Applied Life Sciences, abbreviated as BOKU in Austria, and the IMC University of Applied Sciences Krems.
The Austrian research joins a growing body of work to explore a variety of recovery processes for rare earth metals. One recent project examined a method that does not involve any acid, while another explored what the researchers described as “membrane solvent extraction.” That process involves dissolving rare earth magnets in acid and feeding the resulting liquid through a membrane that only allows the rare earth component to come through.