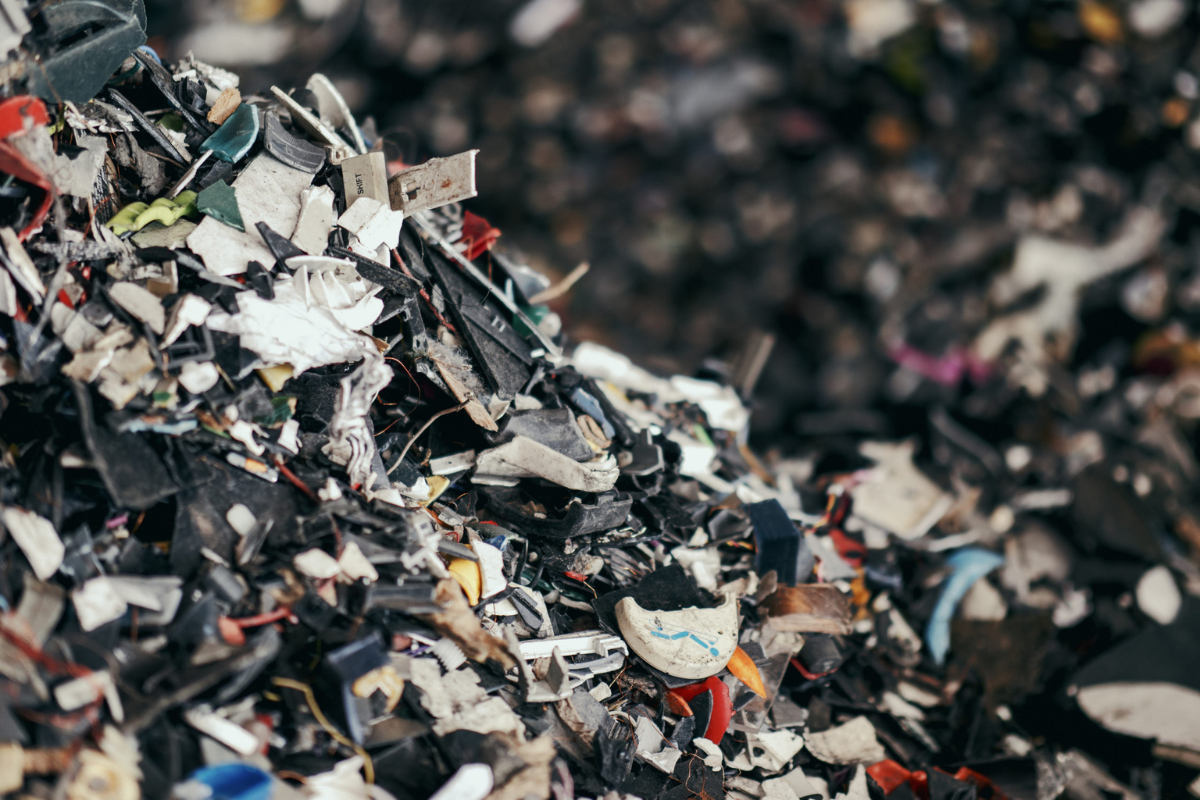
After launching in 2020, Sostenplas grew to one of the top five e-plastics processors in Europe. | Courtesy of Sostenplas
Driven by regulations that abruptly restricted global trade in plastics recovered from electronics, Spanish plastics processor Sostenplas has rapidly emerged as a major downstream for those polymers in Europe. The company’s CEO recently shared lessons the company has learned, with an eye toward helping U.S. companies seize a similar opportunity in North America.
Sostenplas was formed as an offshoot of longtime Spanish scrap plastics broker Fosimpe in 2020. The company started up a 100,000-square-foot processing facility in Segovia, Spain in 2021, bringing in loads of mixed e-plastics – commingled loads of resins like ABS, PS and more – and processing them into sorted flake.
Since launching in 2020, Sostenplas has grown to become among the top five e-plastics processors throughout Europe, according to the company. It’s sourcing material from all over Spain and from nearby countries, and it is growing: Sostenplas completed one expansion in late 2023, and it is planning for another major expansion in the next quarter of this year.
Sostenplas CEO Pablo Leon says the impetus for the company was simple.
“We saw a market opportunity there,” he said in an interview with E-Scrap News. “And I think in the U.S. now it’s a similar situation as when we started. Everyone is saying that there’s a need for some companies jumping into this sector.”
Driven by global rules
Sostenplas operates a single campus, currently processing about 55 million pounds per year of e-plastic, and it has a current capacity to handle about 88 million pounds. The e-plastics it handles are typically acrylonitrile butadiene styrene (ABS), polystyrene (PS) and polypropylene (PP), Leon said, “the three main plastics that make sense to recover, economically, in a big amount.”
Its customers include manufacturers in a range of industries, particularly in the construction and agricultural products industries, durable goods, packaging and even furniture. Leon says Sostenplas wants to get to a place where the e-plastics are going back into new electronic products, but that the landscape has not developed yet.
The company got started because of a confluence of regulatory changes and industry practices.
A 2019 amendment to the Basel Convention changed how mixed scrap plastics are traded around the world, generally requiring the exporter receive written consent from a regulatory body within the importer’s country, before the material can be shipped.
In Europe, the regulations were even stricter: the European Union adopted a policy essentially dictating that member countries can only export scrap plastics to nations within the Organisation for Economic Cooperation and Development (OECD), a group of what are generally considered affluent or developed nations.
Additionally, WEEELABEX, a widely adhered to European certification standard for the e-scrap industry (similar to e-Stewards and R2 in the U.S.), began promoting more accountability around device management throughout the recycling process, Leon said.
In effect, through new regulations and increased accountability, plastics could no longer follow the longtime route of export to Asia. And for Sostenplas, an opportunity presented itself. The company determined there was “clearly enough market for us,” Leon says, because there were virtually no e-plastics recycling outlets in the region.
U.S. e-scrap processors now face a similar dilemma. The Basel Convention changes mean e-plastics are technically not allowed to be shipped from the U.S. to most countries, because the U.S. is not a party to the Convention. These plastics have continued making their way to countries like Malaysia, but recently the top e-scrap certification standards have been increasing scrutiny of how certified companies are handling this material stream. Both e-Stewards and R2 recently said they’ll be “enforcing legal compliance with the Basel Convention and its new amendments as a core tenet of our certifications.”
With very limited North American outlets for e-plastics – the vast majority of that material has historically been exported to Asia – even Sostenplas has received inquiries from U.S. companies looking for downstream outlets. (Leon says although that might make sense in some situations, he believes the best option would be domestic e-plastics processing industry development within the U.S.)
Still, the U.S. industry isn’t in exactly the same position as its European counterpart just yet. U.S. law doesn’t restrict exports of e-plastics the way the EU does, and although it may be against the Basel Convention for countries like Malaysia to import U.S.-sourced material, there’s no regulatory agency stopping U.S. companies from initiating those exports to begin with.
Leon says the strict regulatory changes were really key to the European e-plastics market becoming viable. As long as the decision comes purely down to economics, shipping to southeast Asia will always win out, because fewer environmental and labor standards mean lower processing costs.
Entering an emerging industry
For U.S. companies looking to enter the e-plastics space, Leon advises that they take a measured approach. He ties Sostenplas’s success (it has so far been profitable every year, he said) to a careful, step-by-step progression into the industry. The company has made sure everything works before proceeding to another stage.
As one example, Sostenplas has until this year limited its processing to shredding and sorting material by polymer and by color, and producing sorted, washed flake. For some customers, Sostenplas works with external vendors to pelletize on demand, allowing the company to sell its output in pellet form.
But in the second quarter of 2024, Sostenplas plans to install capacity to pelletize e-plastics in-house.
“We wanted first to achieve the purity that the customers require, and once that is there we would pelletize,” Leon said. “Because we have seen many other companies failing exactly at that: they started pelletizing too early, and the purity was not there, and if you pelletize plastics that are not pure, then you are making something that cannot be used, basically.”
Leon says the company’s sorting process is already producing a highly pure stream, and that the main hurdle for moving from flaking into pelletizing is increasing the homogeneity of the stream. That is, ensuring each batch of material has very similar properties, beyond being the same resin.
The company has also not sunk a huge investment into entering the e-plastics space. Leon estimates the total investment has been between 4 and 5 million Euros so far ($4.3 to $5.4 million). It’s not the largest investment in e-plastics in Europe, he noted, and could be considered quite humble.
“But it has been efficient and profitable,” Leon said. “That’s what we were looking for. We didn’t want to spend the largest amount of money and then find out there was no return.”