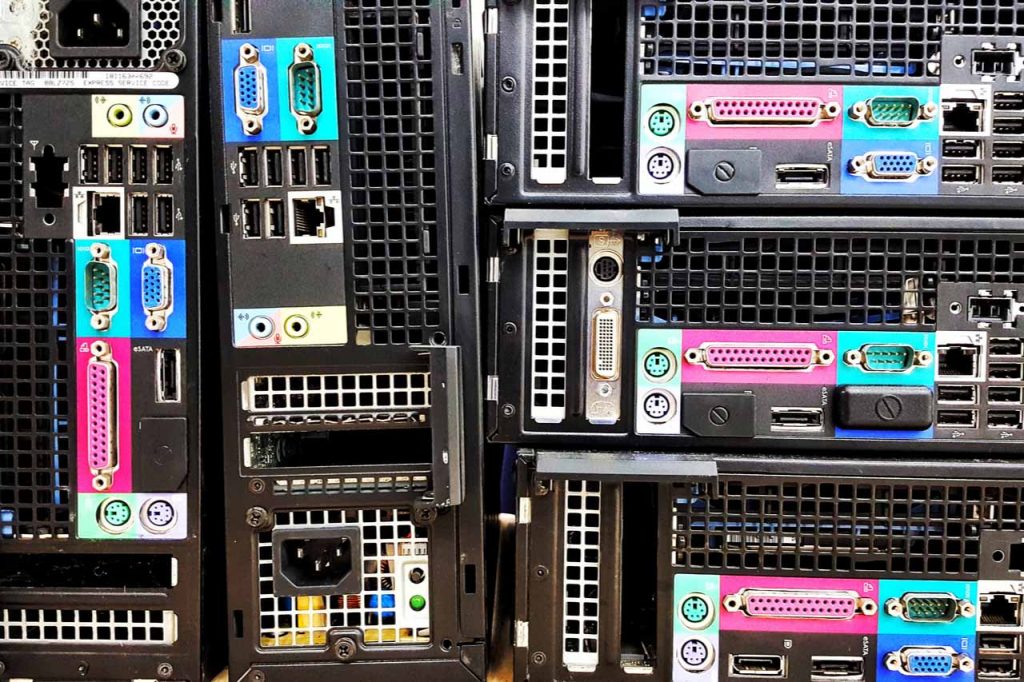
Apto recycled more than 2.9 million pounds of e-scrap and sent more than 316,000 pieces of equipment for reuse in 2020. | Koy_Hipster / Shutterstock
Apto Solutions is experimenting with a new way of tracking where its recycled IT assets ultimately end up. The company released a report on its program this month.
The Atlanta-headquartered company launched the pilot program, titled Circular Transformation, last year. In a press release this month, Apto CEO Jeffrey Jones said the program is part of an effort to increase transparency in communicating how assets are handled during the recycling process.
“When major companies hire a certified ITAD team or recycler to handle end of life electronics or e-waste, they assume that the assets are being recycled in a circular way into new materials and products,” he stated. “While most of the industry is doing the right things, we saw an opportunity to provide a better level of data and transparency that is needed for confirmation of circular economy initiatives. Our report is part of an effort to do exactly that.”
Apto added that the program helped the company “verify what was actually happening to their materials downstream and make additional adjustments to send materials to the most sustainable recyclers.”
In the report, Apto Compliance Officer Caroline Allman said the company was already working with a fully audited downstream vendor network that was in compliance with Apto’s e-Stewards, R2 and other certifications. But the company wanted to gain access to additional data it could share with its customers.
In the past, the company used a network of downstream processors, with different companies providing different processing services. One tier of vendors broke the equipment down and sent it to the next tier, which performed additional processing activities. Ultimately, assets passed through four tiers of processors, Apto wrote, and this system “simply didn’t provide any circularity data.”
Accessing that data required a significant shift in the company’s downstream practices, a model the company employed in the pilot program.
“With this new model, we engineered a refined downstream using new partners,” the report states. “Apto now handles the demanufacturing of the equipment in our own facilities, separating the components that are then shipped directly to the end smelters and refiners. By bypassing the middleman, we were able to construct a solution that provides improved data tracking and transparency, direct data on what raw materials go back into manufacturing, verified supply chain traceability and circularity applications.”
This type of information can be used by customers for compiling sustainability reports, the company noted.
The company processed 275,000 pounds of material through the pilot program, and the company wrote that it will likely continue to scale up this system. In total, Apto recycled more than 2.9 million pounds of e-scrap and sent more than 316,000 pieces of equipment for reuse in 2020, the report states.
The company will share more details about the program and how it works during an Aug. 4 webinar.
Besides its Atlanta facility, Apto operates sites in Austin, Texas and San Leandro, Calif. The company launched in 2001.
More stories about processors
- New ITAD firm launches, acquiring two processors
- Makor ERP to incorporate ESG reporting into platform
- Australian metals company rebrands, builds Texas plant