This article originally appeared in the Spring 2019 issue of E-Scrap News. Subscribe today for access to all print content.
The fire and health risks from lithium-ion batteries are accelerating in recycling operations worldwide at a near runaway rate.
The California Product Stewardship Council, for instance, recently reported that these batteries are now the primary source of fires at waste facilities.
And it’s not just processing sites that face risks as lithium-ion batteries get leveraged by manufacturers in a growing array of electronic devices. The activities of collecting, transporting and storing material have become more complicated (the Federal Aviation Authority has even banned lithium-ion batteries from being checked into luggage due to the documented risk). Finally, in addition to the fire danger is the fact that workers who handle lithium-ion batteries can be exposed to toxic fumes and shock hazards.
Why exactly does this material pose such a threat? And what are the techniques for reducing the impact and risk of fire and other incidents? Those are questions everyone in electronics recycling should be asking.
The hazard
Lithium-ion battery design is a blueprint for catastrophic failure. The electrolytes in these products are flammable and can ignite when the battery is shorted and overheated.
A complicating factor is that a shorted battery produces its own oxygen through a chemical reaction during a short-out event. The flammable contents and self-produced oxygen together can often result not only in a substantial fire, but explosions as well. For example, an average laptop battery can contain 900 kilojoules per kilogram of stored energy, which is the same amount of energy 30,000 firecrackers release when exploding.
Issues often stem from the battery being punctured, which can happen if a battery is shredded or impacted during processing or handling. However, some lithium-ion batteries can thermally run away just sitting. Many poorly made or abused batteries exhibit a condition called lithium dendrite formation. This condition is caused when fine hairs of lithium form within the battery and pierce the internal polymer separator to produce a short. The issue is of particular concern when batteries are stored in numbers.
A shorted battery can be managed relatively quickly if proper procedures are in place (more on those later). But the problem grows considerably if the battery is surrounded by other flammable items, as is often the case in recycling environments, where paper, wood or other batteries might be nearby.
In addition to the dangers of fire, those working with and around these batteries face the hazard of toxic gases containing fluorine, which are produced during combustion of lithium-ion products. Among the gases formed are hydrogen fluoride (HF), phosphoryl fluoride (POF3) and phosphorus pentafluoride (PF5). The HF gas is especially toxic to people and affects the eyes and lungs fastest.
A battery-caused incident can threaten a recycling business in multiple ways. Even if the fire and evacuation only consume several hours, the grief from the landlord, local media, neighbors and customers can have a lasting negative effect.
If equipment is damaged and days of production are lost, the cost of new machinery and disrupted service can be hugely damaging. And if the building is damaged, equipment is severely burned, or fines are unleashed, the company could be entangled in bankruptcy and legal proceedings for years – or it may need to close immediately.
Trends expanding the problem
As society’s use of electronics continues to evolve, the complications of battery management will only grow.
The lithium-ion issue was the topic of the opening session at the 2018 Electronics Reuse Conference in Nashville, Tenn. last October. Panelist Charlie Monahan, director of regulatory compliance at Panasonic, noted that between 2015 and 2020, manufacturers were expecting to triple the output of lithium-ion batteries worldwide. And such growth is expected to accelerate. “The amount you see out there now is nothing compared to what we’ll be seeing in the future,” Monahan said.
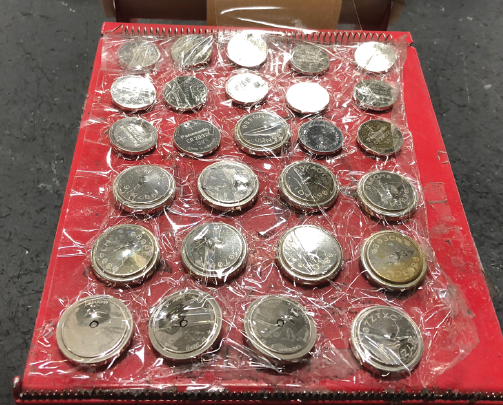
One storage and transport best practice is to isolate terminals with tape.
Besides being found in more types of devices, including appliances and toys, these lithium-ion batteries are taking on new form factors and can be harder to identify to the novice, which means they will likely end up in the waste stream more often and could be much more challenging to spot in an e-scrap plant.
To compound the issue, the proliferation of 5G wireless technology is going to open the door to faster speeds and more device connectivity. As the internet of things accelerates, lithium-ion usage will proliferate. Meanwhile, some electronics are being developed with multiple batteries within the same device. This can lead to a situation where someone on a recycling line or elsewhere removes a battery and thinks the risk has been averted; meanwhile, another battery remains hidden.
And speaking of battery removal, many mobile and small devices have their batteries glued or taped in place. This design choice makes it labor-intensive to remove the batteries, causing prying and other crude means of removal that can short the batteries in the process. Some companies, such as iFixit, now supply special spatulas making the removal activity safer. Custom jigs can also be developed that selectively bend, pull or pinch open a device in a safe and repeatable way.
Finally, due to strong fluctuations in volumes of inbound material, many plants use temporary staff or workers that do not stay long. Proper training and level of care can be lacking in these situations, and such production pressures may cause some batteries to be missed during de-manufacturing or make them more likely to be damaged during repair efforts.
Preventative best practices
The good news is that many of the techniques used to mitigate risks associated with battery handling and storage are relatively low-cost. And as more companies take steps to protect themselves, the most useful steps are becoming better understood and systems well-honed.
For facilities that accrue battery-bearing material, two storage strategies are common: palletized materials or pile storage. In both scenarios it’s important to build in fire breaks (open spaces that can help stop the spread of fire). In the case of palletized rows of scrap materials, consider fire breaks of 24 inches every two rows.
Also set a limit on double-stacked materials to prevent the risk of falling or crushed boxes. For piles, even more diligence is needed – one best practice is to make sure the sprinkler system over the storage area is rated for the relevant hazard and fuel level. Setting maximum pile sizes and adding fire breaks is even more critical.
Most importantly, ensure the scrap is de-polluted, with batteries removed, before material is stored or baled for shipment. If a shovel loader or skid steer is used, the likelihood increases for the material to be unintentionally crushed and potentially short (this unfortunately happens often).
Once batteries are removed, the risk now shifts to the storage of batteries themselves. Batteries should have terminals isolated with tape, or similar effective means, which most downstream destinations require. Proper containers, approved by entities such as the Department of Transportation or the United Nations, should be used, per local and federal regulations.
Besides having a dedicated area for battery storage, consider keeping smaller inventories once the batteries are prepped. This step can reduce the potential for a large exothermic event, since even in a stored state batteries can spontaneously short and explode. Certain agencies are in fact reviewing guidelines on fire codes, and it is possible these codes may change in the future and cover things such as areas of isolation, designated areas and adequate fire protection.
And communication with all staff about best practices is critical. A storyboard showing examples of proper battery management that is placed at strategic locations on a processing line can be a partial remedy to keep proper handling protocols on everyone’s mind.
Control and suppression
Should a fire begin in a facility, a host of concerns will come up. Are the employees, neighbors and first responders safe? What will my customers say? These are the tough questions that will be on a business owner’s mind and that can sometimes be avoided with means to detect and suppress a conflagration.
The cheapest solution is having water available in proximity to the fire. Even though the batteries in question do have the word “lithium” in their name, the amount of elemental lithium in the items is limited and water or standard extinguishers can be effective when the fire is small. Some facilities even install water hose stations as an inexpensive measure.
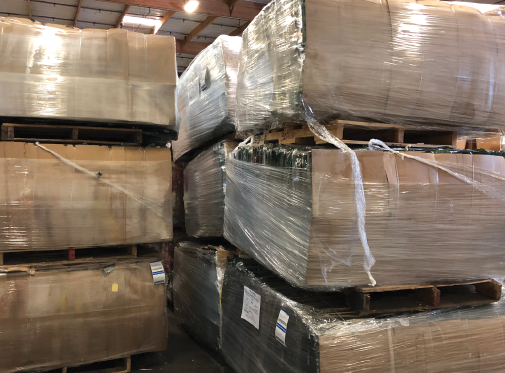
Proper stacking is an important consideration when handling battery-bearing material. Falling or crushed boxes can lead to shorted batteries and possible fires or explosions.
Adding extra extinguishers in certain high-risk areas is also well worth the minimal expense. For an area with pile storage or centralized battery collection, a compressed air foam system (CAFS) may be the right fit. These systems are portable on carts and often use compressed nitrogen to make a foam from water and a special foaming agent. The foam produced can be up to 20 times the volume of the tank and reach distances of over 90 feet. The foaming chemical concentrate also acts as a wetting agent that rapidly cools the material on fire and promotes surface sealing to reduce vapor from emitting and burning. In the case of a pile or stack of boxes being on fire and far from access, the CAFS systems are very effective at reaching the affected area, but these work best when the fire is smaller.
Since most workers in a recycling plant are focused on their normal duties, some fires may go unnoticed until too late, or worse, may happen after hours. Fortunately, many automated detection solutions are readily available and easy to adapt to most plants.
Smoke detectors should be used per code but added in higher concentrations in areas of risk. Some styles of detectors use an infrared beam to span a large area for a faster response. And newer detectors use multiple gas detection sensors through which carbon monoxide (CO) and carbon dioxide (CO2) concentrations are closely monitored. These technologies can detect with a high degree of accuracy even extremely small fires.
Other early-warning systems that sense heat use infrared detectors, cameras or simple tubes designed to open a circuit at a certain temperature. The tube-style heat detectors are especially useful in ducting, dust collectors and tight-quartered areas. Depending on the activity, some facilities may need a detector that has less false positives, such as a triple-band optical flame detector. While expensive, the accuracy and early-warning capabilities of these tools are effective. Key in applying these detection methods is having automated notification to multiple parties.
Automating the response
When it comes to shredding systems, higher risk pile storage, or finished goods that have a risk of a rogue battery, a more automated approach is needed.
For a shred line, optical flame detectors can be placed in the shredder and over conveyors that sit directly downstream. These fast-response detectors are offered in explosion-proof heavy enclosures to stand up to extreme conditions. As a small flame is detected, a specialized controller can stop the shred line to prevent the spread of the fire downstream or to the dust collection system while sounding an alarm.
In parallel, a solenoid valve can direct water specifically to the conveyor or zone where the detector was placed. Some variants will have local buttons for each zone in the case of an operator seeing smoke and wanting to engage the system manually. These shredder-based systems are common in Europe and are now becoming more mainstream in North America.
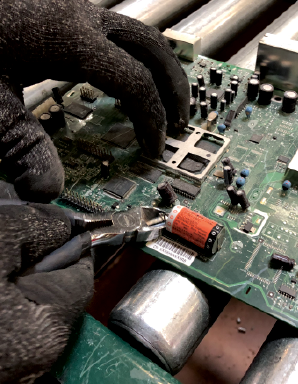
In many cases, the design of electronic products leads to batteries that are difficult to properly and efficiently remove.
Due to the dusty and rugged environment of a recycling plant, these systems require a preventative maintenance program to make sure detectors are kept clean and solenoids are in good working order. For tougher zones, such as the shredder, an air shield can be installed that uses periodic blasts of compressed air to keep the sensor clean.
For the case of covering a large area, a company called Fire Rover has developed a CAFS system that is pre-installed in a shipping container. It features a tall mast that contains infrared cameras and closed circuit video. The camera automatically detects heat, and a person at a remote central station can verify whether the detection is indeed a fire. The central station will also remotely control a nozzle on the top of the mast to direct a foam sprayer and disperse it correctly to suppress or extinguish the fire. While these systems are used abundantly in municipal recycling plants, they are suitable for e-scrap plants as well and can be installed quickly.
Outlook for new technology
Electronics and their power sources are constantly evolving, and we can expect lithium-ion batteries to become safer over time. However, recycling plants will see residuals for years after a change is made and must be ready. Safer chemistry may be on the horizon, but the human health risk of the chemicals used in the electrolytes should be carefully monitored. And battery-bearing devices should not be accepted easily for shredding.
It’s also true some valuable new tools are becoming available. Artificial intelligence sort systems are now able to use a simple camera and make identifications and sorting decisions. These can be deployed prior to a shredding process and identify items that may have a battery inside. Other units may be able to scan the shredded scrap and pick out a battery that may have been bypassed during the de-manufacturing process. Some equipment providers are working on systems to automatically sort batteries by type and then tape and isolate.
Whether investing in best practices for storage, better de-manufacturing, heightened detection or other steps, the cost for this “insurance” is low compared with a burned-down business and a broken dream.
Rafael Reveles is the president of Converge Engineering, a manufacturer of products and services that support data destruction, shredding and recycling systems. He can be contacted at [email protected]. For more information, visit the Converge website at convergeengineering.com.