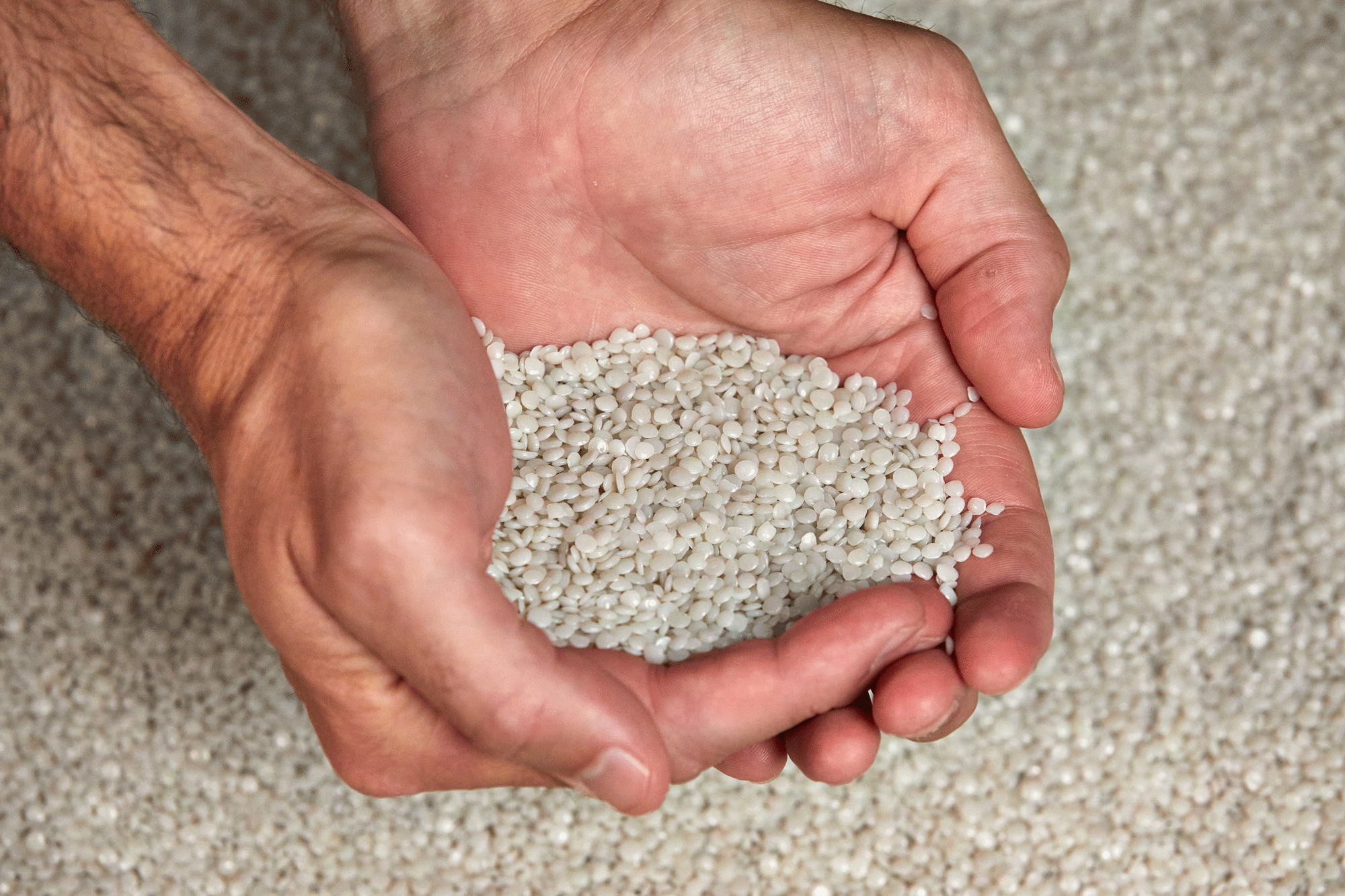
Courtesy of Nova Chemicals
This article appeared in the December 2024 issue of Resource Recycling. Subscribe today for access to all print content.
As the demand for plastic packaging continues to grow because of its benefits for protecting food and lightweighting, consumer preferences and government legislation are driving brand owners to rethink the way plastic packaging products are used and recycled. To address concerns about waste, pollution and human and environmental health, packaging producers are searching for ways to transition to a more plastic circular economy. In a circular model of consumption, one of the primary goals is to divert plastic waste from landfills and keep materials in the economy in high-value applications as long as possible.
In addition to redesigning packaging for recyclability, many companies are setting ambitious goals to increase the use of post-consumer recycled materials in their packaging by 2030. Some organizations are also investing in recycling projects to process post-consumer materials. Despite this momentum, some of the world’s largest brands are already revising their post-consumer resin targets due to difficulties sourcing high-quality recycled plastic feedstock.
The current waste collection and plastic processing infrastructure is not equipped to meet the purity requirements of feedstock for many types of in-demand packaging solutions such as food-contact materials. According to The Recycling Partnership, material recovery facilities vary greatly in their ability to process collected recyclables into outbound commodities, and they estimate that only 79% of post-consumer plastic materials received are actually sorted and processed. McKinsey reports that even the bales that are sorted and sold often consist of multiple types of plastics and non-plastic contaminants and residues, making them unqualified for most types of mechanical recycling and even some chemical recycling processes.
As overall recycling rates in the U.S. stagnate and demand for PCR increases, recyclers are resorting to importing plastic scrap. ICIS reports that 2023 was the first year that the U.S. was a net importer of scrap plastic, bringing in more than 63,000 tons of polyethylene to supplement their PCR capacity. Without an adequate supply of recycled feedstock, it will be impossible for brands to achieve their PCR packaging goals and comply with PCR material mandates such as those enacted in California, Washington, New Jersey and Maine.
Creating high-quality feedstock is a complex opportunity that involves the entire value chain. Regulatory and processing requirements demand materials that can be traced to their origin to ensure safe, high-performing recycled plastics that can be used in food packaging and other high-performing plastic products. Although building the supply chain for recycled feedstock requires many moving parts, with continued collaboration, creativity and investment, the packaging industry can build an economically viable circular economy that supports both plastic recycling and the use of recycled materials.
Complicating factors
There are multiple factors that make plastic recycling complex. For example, there are multiple types of plastic that are further modified by colorants, processing aids, antioxidants and other additives. These substances, along with the recycling and reforming process, impact the possible end uses of the recycled materials. Mixtures of multiple types of plastics can also affect the functionality and structural integrity of the recycled product.
For food-contact PCR materials, recyclers need to establish a chain of custody that includes the source and uses of the material to track additives and chemical contaminants. The U.S. Food and Drug Administration states that recycled food-contact plastic must meet the same specifications as virgin plastic. The organization reviews each proposed recycling process designed for food-
contact applications. If the process is expected to produce acceptable food-grade materials, a letter of non-objection is issued.
Although not a formal approval or a legally binding document, obtaining an LNO is a best practice for recyclers looking to create food-contact materials. To submit an LNO, recyclers must describe their recycling process, provide surrogate contaminant testing results and explain the intended use of the recycled plastic. Even within post-consumer food packaging, different additives can limit end uses, such as plastics approved only for low-temperature applications or specific food types.
Changing perspectives
Because plastics are so diverse and pure feedstock is so critical, producers, retailers and consumers must all play a part in improving recycling rates and practices. Public education on the value of recycled plastic and the legitimacy of plastic recycling is needed to motivate people to take action. For consumers, that could involve encouraging participation in a variety of recycling options, such as sorting materials in bins for curbside pickup or bringing plastic materials to store drop-off locations.
On the commercial side, businesses must be willing to commit to increased tracking and recordkeeping to validate the chain of custody, including documenting the manufacturers of plastic they use, what it was used to package and what it came in contact with during transportation and storage. Everyone from consumers to businesses has an important role to play in plastics circularity.
Investing in infrastructure
In addition to education on plastic recycling, governments and corporations must work together to increase access to recycling programs. Investing in the recycling infrastructure includes increasing capacity with new facilities and may also involve the development of secondary sortation facilities. Known as plastics recovery facilities, these secondary operations have advanced sorting capabilities that can separate mixed materials that MRFs cannot. Increasing the supply of high-quality PCR bales requires the development of collection networks and validation protocols to create traceable sources of post-consumer plastics. This process should involve the exploration of untapped resources of recyclable materials, such as large users of food packaging like event venues and sports stadiums.
The plastic industry must work together to improve the quality and availability of recycled plastic feedstock. Research into plastics circularity operations estimates that a third of the $50 billion needed to scale up plastic recycling by 2030 should go to feedstock sourcing and preparation. With several extended producer responsibility programs and PCR material mandates in process and many more proposed, the time is now for investing in the changes needed to advance recycling technology and enable high quality PCR materials. Partnerships, supply agreements and joint ventures throughout the plastic value chain are necessary to drive the widescale, system-level change needed to make PCR material mandates achievable and make meaningful progress toward a circular economy.
Alan Schrob is director of mechanical recycling at Nova Chemicals. He spent 20 of his 30 years in the plastics industry encouraging circularity in a variety of roles, including business development, marketing and the rigid and performance films markets.
The views and opinions expressed are those of the author and do not imply endorsement by Resource Recycling, Inc. If you have a subject you wish to cover in an op-ed, please send a short proposal to [email protected] for consideration.