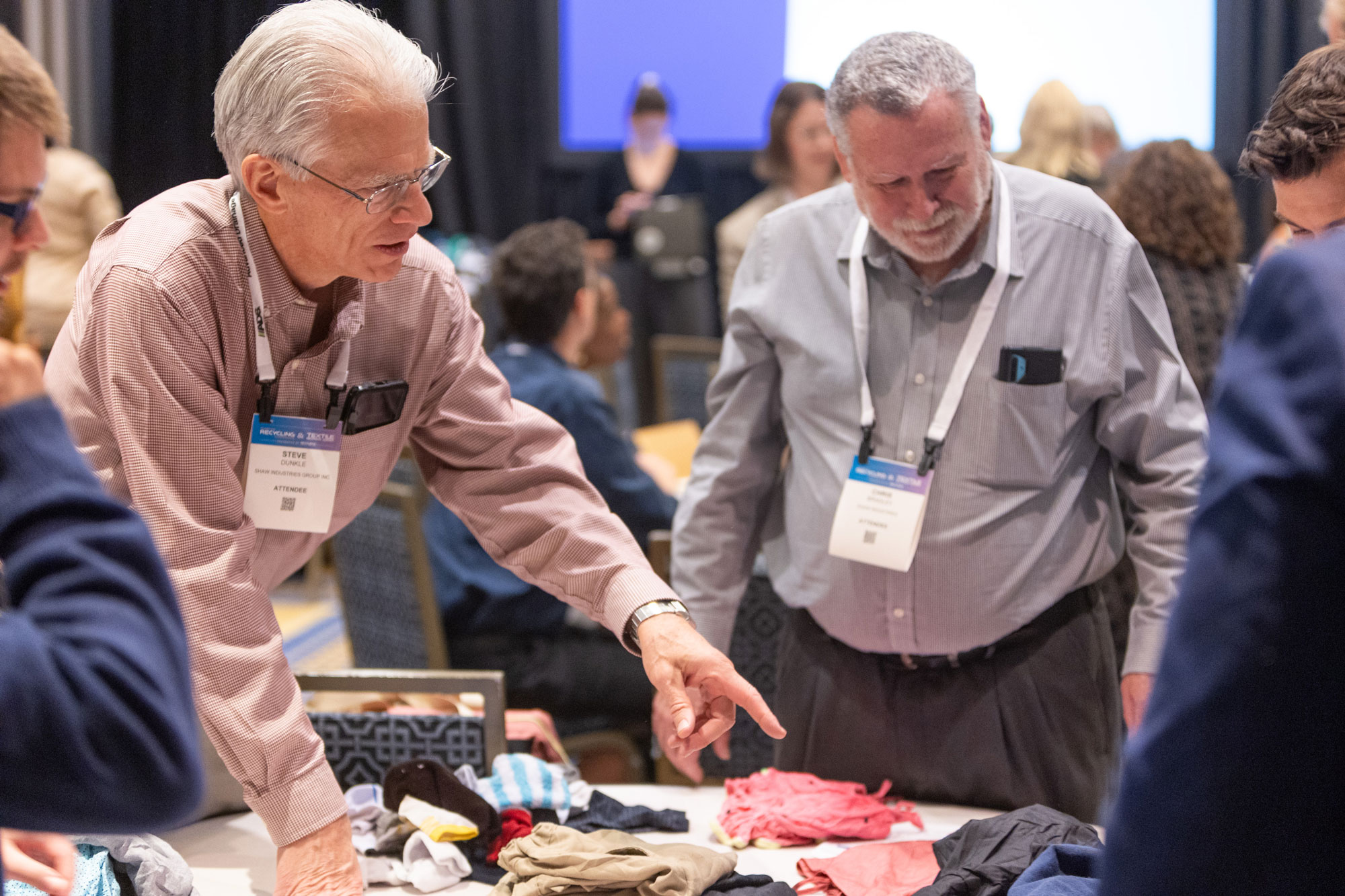
This year’s Plastics Recycling Conference featured the first Textile Recovery Summit, a special track devoted to the most recent developments in an old industry. | Big Wave Productions/Resource Recycling, Inc.
This article appeared in the May 2025 issue of Resource Recycling. Subscribe today for access to all print content.
Textile recycling was a novel addition to this year’s Plastics Recycling Conference, but as several experts said at the event, the topic’s roots go back centuries, and its contemporary issues and developments are familiar to just about any recycled material.
A need for better data and better education? Check. A nascent but growing extended producer responsibility apparatus? Check. Advancing technologies for identifying and sorting? Check. An increasingly urgent need to do more? That’s an easy one.
The U.S. produces around 17 million tons of discarded clothing and other fabrics each year, according to RRS, and more than two-thirds of all of those fibers and strings are made of polyester, nylon and other forms of plastic. About 15% of this mountain of material is repurposed or processed into rags, insulation and similar goods or, rarest of all, new clothing.
“Big picture here, we’re generating lots of textiles, and we’re not doing a very good job of recovering it,” said Marisa Adler, a senior consultant at RRS.
Adler partnered with Resource Recycling, Closed Loop Partners, Goodwill Industries and textile trading company Whitehouse & Schapiro to put on the inaugural Textile Recovery Summit, a focused series of sessions and workshops at this publication’s annual plastics conference. The combo event brought more than 2,400 attendees to National Harbor, Maryland, in March.
Speakers and innovators described an industry in the midst of a sea change, as new policy and new technology take hold.
Untrustworthy labels
One crowded workshop gave a hands-on opportunity to simulate one of the first steps in recycling textiles: sorting by composition, most fitting end market and other characteristics. Attendees dug through genuine bales of donated clothing, using their best judgment and portable fabric scanners to answer such questions as whether an old cardigan was made of wool or polyester and whether it would be better off in a nice vintage store or cut into rags.
Identification and sorting are essential for maximizing a used textile’s value, Adler and others said, but there’s a big problem with the little tags that purport to say what a piece of clothing is made of.
“There’s a high inaccuracy on the labels; you can’t trust them at all,” said Helio Moreira, head of sorting for Textile House (stylized as TEXTILE house), a Slovakian company that runs almost 200 secondhand clothing stores across Europe.
To get more reliable information on its wares, Textile House has begun leaning on equipment from Picvisa, a Barcelona-based company that combines spectroscopy with artificial intelligence to identify color, fiber type, texture and more. The system can be tailored to handling post-consumer clothing, for fabric off-cuts and clippings, and just for shoe soles, said Silvia Gregorini, Picvisa’s business development manager.
“Probably one of the key elements is that we have the knowledge on the technology, and they have the knowledge on the market,” Gregorini said of her company’s partnership with Textile House. “Of course there’s an investment to do when we install this technology, but on the long term this is a machine that allows you to scale up volume.”
Similar systems were also highlighted during the textile summit’s innovator stage, a pitch competition among five recycling start-ups.
California-based Refiberd, for instance, uses a hyperspectral camera and an AI system trained on a library of thousands of fiber samples to detect all manner of fiber blends, said Rebecca Geppert, director of partnerships. The system was about to be deployed to a commercial facility for the first time.
“The hyperspectral camera gives us the spectral data, but without anything to interpret that spectral data, you really don’t have anything that detects the material composition,” Geppert said.
Besides fiber composition, chemical additives make clothing even more complicated, and even the same product from the same company can differ from one piece to another, said Christopher Wai, co-founder and CEO of Sixone Labs, which the contest’s judges picked as the winner.
The British Columbia-based company builds a database of all of those different permutations to guide chemical recycling, which breaks plastics down into their molecular components for remanufacture but often relies on pure feedstock. Wai said Sixone’s database allows this process to be finetuned so that polyester can be extracted from fabric that would conventionally be considered impure, such as a cotton-poly blend, while also leaving the cotton and other components unharmed for other uses.
“As we think about clothing, I look at it as a big puzzle,” Wai said. “This is a data problem more than a recycling problem.”
Emergence of EPR
Another panel discussion dug into California’s SB 707, an EPR law for textiles that passed late last year and is the first of its kind in the U.S. Like most EPR programs for other materials, the law requires producers of apparel or textile articles to form a producer responsibility organization that will conduct a needs assessment and set recycling targets over the next few years, among other duties.
The program’s details are in development, but it’s already creating exciting opportunities to grow textile recycling and set an example for other states, several experts said. Chelsea Murtha, senior director of sustainability for the American Apparel & Footwear Association, said member companies often discuss their circularity goals with her, but only one-on-one.
“It has been a struggle to give them a space to really have those conversations at the industry level that doesn’t violate anti-trust guidelines,” she said. EPR can give them “that space and that platform.”
Joanne Brasch, director of advocacy at the California Product Stewardship Council, also praised the law’s emphasis on repair, as distinct from straight resale on one hand and deconstructive fiber recycling on the other.
“There’s this entire stream in our textile stream that, with just a little repair, with a little upcycling, some (innovation) and creativity, it can still have its reuse functionality,” she said. “One thing that 707 does is create that third stream, and it puts a lot of funding into that repair stream.”
EPR for clothing has been around for years in several European countries and has been invaluable in ensuring the existence of end markets for textiles and fibers, Moreira at Textile House said.
“We are quite reliant on that, and if this type or shape of legislation would be widespread throughout the EU, it could put up a demand. Otherwise, we will never be as competitive as Asian feedstock,” he said.
Still, several panelists voiced concerns over the California law’s implementation, saying regulators should listen to industry expertise, while the industry should also prepare for new and more extensive data collection and other changes. As the first state EPR programs for packaging go into effect, Andriana Kontovrakis, director of EPR solutions for Reverse Logistics Group, pointed to widespread procrastination among packaging companies as an example to avoid.
“A number of big companies came to us in the summer and were like, ‘We’re not ready, what do we do?’ And we’re like, you should’ve come to us like two years ago,” Kontovrakis said with a laugh. “The more forward-looking you are, the farther out you start, the better off you are.”