This article originally appeared in the June 2019 issue of Resource Recycling. Subscribe today for access to all print content.
Let’s come to an understanding right from the start – recycling isn’t free, and recycling isn’t a cash cow. That point has been solidified of late for local program leaders, many of whom are facing difficult choices as they sit down to develop viable contracts and programs for the future.
However, while the municipal recycling sector might look a lot different now than it did two decades ago (or even two years ago), there is also plenty of reason to believe recycling programs will remain stable moving forward and even grow in exciting ways.
This optimism is based on innovative work being done by materials recovery facilities (MRFs), end market entities and sustainability-minded communities. Yes, the industry is facing a range of challenges, but smart use of technology, strong business strategies, widespread collaboration, and dedication on the part of stakeholders are opening the door to new materials diversion opportunities with significant bottom-line benefits.
Adapting the MRF
Even before China turned the industry upside down by restricting imports, material processing operations were being forced to adapt to move ahead. Just look at the shifting stream MRFs have had to handle.
In 1960, for example, newspapers accounted for 32% of the materials recycled or composted in the U.S., according to the Environmental Protection Agency. By 2015, that amount dropped to just 5%. This is a result of additional materials entering the recycling stream and a substantial decrease in newspapers overall. The American Forest & Paper Association reports that newsprint supply has decreased more than 70% since 2000. Meanwhile, convenience-oriented packaging is more often being made of mixed or layered material composition. MRFs are challenged to capture this growing material stream.
Over the past years, the need to take action has been amplified for processors. MRFs have been slowing down belts and adding workers to improve quality standards. Many large- and medium-sized MRFs are investing heavily in recycling processing technology to achieve cleaner bales, and these investments can be seen as a dedication to the long-term viability of recycling.
One notable example can be seen in Denver, where Alpine Waste & Recycling has embraced emerging technology. The facility added a second metering ballistic separator and a second optical sorter for fiber and HDPE plastic.
Alpine also brought on an artificial intelligence unit from AMP Robotics that efficiently sorts cartons and paper cups – identifying up to 100 material types and executing 80 picks per minute – to produce a mixed poly-coated bale. The robot was installed in 2017, thanks to a grant from the Carton Council. And the acceptance of paper cups for the mixed poly bale was made possible through a partnership with the Foodservice Packaging Institute, the city of Denver and recycled fiber mill company Sustana.
“We try to see what we can pull out of the landfill and recover in the long term,” said Brent Hildebrand, former vice president of recycling for Alpine. “It is inspiring to see how technology plays into this.
Elsewhere, MRFs are engaging in projects to help test the recyclability of newer types of material and to demonstrate the processes and equipment necessary to handle these streams.
Currently, the J.P. Mascaro & Sons Total Recycle MRF in Birdsboro, Pa. is conducting a pilot project using upgraded equipment to sort and bale flexible plastic packaging. Supported by the packaging industry-backed Materials Recovery for the Future collaborative, the initiative seeks to reduce contamination in paper bales (flexible packaging, if not sorted, can end up in the fiber stream at a MRF) and also produce a new commodity bale – rFlex – that can be sold into end markets.
Growing domestic end markets
Once material is sorted, it of course needs a buyer. And with Asian countries reducing their appetite for recovered material, there has been work to push forward domestic consumption on several fronts.
There is evidence, for example, of growing domestic end markets in the U.S. paper market. Historically, poly-coated paper items like cups and takeout containers have not been widely accepted in recycling programs because recovered fiber mills were concerned about the coatings and possible food contamination. However, a growing number of mills – including those run by Graphic Packaging, Pratt, Sustana Fiber and WestRock – have determined that these items can be processed successfully and will now accept paper bales that include poly-coated foodservice packaging.
Sustana Fiber is one encouraging case study. Just outside of Green Bay, Wisc., the recycled-fiber mill has recently expanded its acceptance of poly-coated packaging options. Currently, the mill uses sorted office paper, printer waste, food and beverage cartons, paper cups and paper containers as raw material, receiving approximately 1.3 million pounds of post-consumer paper daily from suppliers within a 350-mile radius.
The mill’s 55 employees produce approximately 450 tons of deinked recycled pulp per day with the resulting fiber used for printing, writing and tissue papers. Sustana Fiber is the only U.S. recycled-fiber mill that produces pulp to make FDA-grade paper cups and foodservice packaging.
“One of the [industry] trends we are seeing is that consumers are continuously placing pressure on corporations to have sustainable products,” said Michele Bartolini, senior marketing director for Sustana. Bartolini points to relationships with communities, MRFs and other stakeholders as an essential part of the company’s strategy to source “alternative fibers” that otherwise would have gone to landfill.
It’s also important to remember that end-use innovation doesn’t always come from the companies making millions or billions of dollars in revenue; sometimes it can come through the public sector.
The Colorado Department of Public Health and Environment, for instance, last year launched Colorado NextCycle, an incentivized business incubator aimed at developing recovered commodity or organic material end markets in Colorado. The program is assisting selected teams in preparing business concepts through technical advisement, access to relevant recovery and regional data, and modest financial grants. The goal is to have these teams develop shovel-ready business plans that can be submitted for the department’s large grant application cycle and ultimately implemented in Colorado.
The latest pushes continue the drive to develop domestic end markets that has been ongoing for decades. Efforts can be seen in the form of grant programs, material exchanges, research studies, business and technical advisement centers, tax credits, idea incubators and private investments.
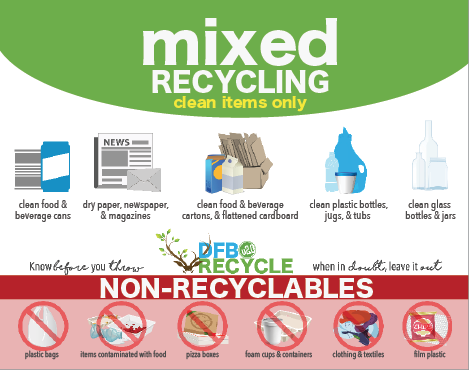
The city of Deerfield Beach, Fla. launched an outreach campaign last year that helped bring down its contamination rate by eight percentage points.
Leveraging collaborative systems
Sometimes working together can be more efficient and fruitful than working alone. And local governments are finding that to be true as they take steps to strengthen their recycling programs amid today’s turbulence.
Neighboring communities have long come together for essential services and programs such as police, fire, water, and sewer to increase efficiencies and lower costs. Given the current market conditions, communities are seeking more opportunities for collaboration on materials diversion to maintain their current levels of service (or expand them) without raising costs.
Two years ago, Washtenaw County, Mich., began exploring regional cooperation among the county’s governmental units, service providers, business stakeholders and local environmental groups. The purpose was to offer a more comprehensive system of waste diversion and services to the residents within a regional authority governance model.
Soon after, an authority was formed by eight communities ranging in population from 4,200 to 118,000 residents.
“Our stakeholder engagement process found many communities face similar challenges,” said Theo Eggermont, Washtenaw County’s Public Works manager. “Working together can begin to address these challenges, create economies of scale, and provide consistent educational messaging.”
The initial focus of the authority is to improve the quality and quantity of recyclables in the region with the potential for developing a MRF sometime in the future (the regional facility located in Ann Arbor was closed over two years ago).
While exploring options, Washtenaw County drew upon several examples in Michigan. One is SOCRRA, a regional authority that has provided services to its 12 member communities in Southeastern Oakland County since the 1950s. SOCRRA owns and operates its own
MRF, trash transfer station and composting site, all of which allows SOCRRA to better control costs while providing top-notch services to its communities.
SOCRRA also manages the collection contracts for all 12 member communities, which are collectively served by three different haulers. For SOCRRA members, recycling offsets the cost of trash disposal: For every ton of recyclables, communities earn a rebate; for every ton of trash, communities pay a per ton fee. This incentive remains in place despite market challenges.
Collaboration tends to make even more sense in rural areas. About four hours north of the metro Detroit area is Emmet County, which has perhaps one of the best recycling programs in the state. Located in the northern tip of Michigan’s lower peninsula, Emmet County has a population of roughly 30,000 people. Built from the ground up over 30 years ago, the county’s program boasts a cost-effective and comprehensive system that offers recycling of over 60 materials, resource recovery, and solid waste transfer services without relying on tax dollars.
The county’s facilities serve as a regional hub for neighboring counties that would struggle otherwise to provide consistent and convenient recycling services to their residents. These services are provided through contracts and intergovernmental agreements.
Utilizing education and communication
The promotion of recycling has changed over the decades. And, lately, outreach possibilities have been affected by the fact that many local governments are feeling helpless in the face of contract negotiations in a down recycling market.
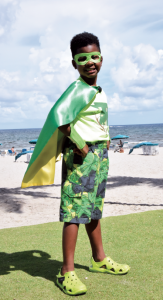
Ricky the Recycling Ranger stars in short online videos Deerfield Beach is using to keep residents engaged on waste diversion.
Recycling collection and processing is a service that should be paid, akin to garbage collection. However, cities and counties cannot adequately budget around fluctuating commodity prices, and they are feeling pressure to modify lists of acceptable materials, a move that could be detrimental to the recycling industry moving forward.
In some areas, local leaders are responding by returning to the roots of effective resident education, finding new ways to keep messaging simple, consistent, honest, current and repetitive.
In 2018, the city of Deerfield Beach, Fla. had a solicitation for recycling processing that received no response, as the terms and conditions were not desirable enough for any vendor to bid. With increased costs for maintaining their recycling program, municipal legislators decided to cancel the city’s 20-year old recycling program.
But the move created a backlash among residents, and just a few weeks later, Deerfield Beach was back at the bargaining table with a focus on keeping recycling, decreasing contamination and increasing education.
“We did not remove any acceptable recyclables with this contract,” said Chad Grecsek, director of sustainable management for Deerfield Beach. “Initially, we thought that removing glass would simplify things from a cost perspective when, actually, removing the glass would have hurt us financially and confused our residents.”
The city launched an outreach campaign called “DFB Recycle v2.0 Know Before You Throw,” which included a website facelift, public giveaways and short educational videos starring a spirited 10-year old playing a character called Ricky the Recycling Ranger. The investment in communications paid off with a reduction in contamination from 45 percent to 37 percent after the campaign.
To then reduce contamination to under 20 percent, Deerfield Beach began an aggressive cart auditing program that enacts a three-strikes rule for contamination repeat offenders. Cart auditing requires a knowledgeable team, the ability to tag and/or notify residents of the contaminant, and the creation of a clear point of contact for curious or angry residents. The cost and time to provide enforcement and provide continued check-ins is a factor that must be discussed and agreed upon by all parties.
Recycling isn’t dead
The China ban, commodity pricing declines, evolving packaging, changing waste streams – yes, recycling has its challenges. However, look to our oceans, rivers, parks, wildlife and air quality to see the effects of debilitating discards that result from human consumption.
Efforts are occurring around the globe aiming at reducing our use of certain materials, recovering the materials we do use, and improving our processes to lower our impact on our natural resources.
It is hard work, and it is worth it. That may mean taking small individual steps, or giant collaborative leaps – the key is maintaining the quest to keep up with the ever-changing economic and material landscape.
Marissa Segundo is a communications consultant at RRS and can be contacted at [email protected]. Anna Lynott is a senior consultant and can be contacted at [email protected]. Kris Kaar is a senior consultant and can be contacted at [email protected].