This story originally appeared in the May 2016 issue of Resource Recycling.
Subscribe today for access to all print content.
Over 140,000 solid waste collection vehicles take to the streets of North America every day. These workhorse vehicles may not always get the respect they deserve, however, because the men and women in our industry make a complicated and dangerous task look simple. Much of this efficiency and fluidity has come through advances in truck design.
Although the solid waste vehicles we see every day may not appear to have changed much, their designs continue to improve as waste generation habits evolve. It has been said that legislation drives change and innovation, and a few key moments in solid waste history stand out as pivotal, driving design changes in solid waste collection vehicles. For example, the Resource Conservation and Recovery Act (RCRA) of 1976 and Subtitle D brought with it the concept of large regional landfills and waste-to-energy facilities, and vehicle payloads became an important concern.
The late 1980s, meanwhile, brought recycling legislation, and there was an immediate demand for revamped vehicle designs and, in some cases, entirely new fleets of trucks to provide collection of recyclables in places where this service had not existed previously. With multiple streams of new recyclables that needed to be co-collected, yet kept separate for processing, trucks were adapted with compartmentalized bodies to hold anywhere from two to eight streams of different materials.
That era was followed by the dawn of single-stream recycling collection and the cost-savings efficiencies the simplified process could bring. Today, truck engineering is being affected by growing demands for organics collection and emissions reductions as well as technological breakthroughs in the electricity systems in vehicles.
In this article, we’ll detail some of the major technological updates that have brought collection trucks to their current place and delve into the details on what manufacturers are working on to tailor vehicles to today’s market.
Garbage and recycling in one pass
Back in the days before single-stream collection dominated U.S. recycling, everything depended on local processing infrastructure. In cities or towns that could recycle a wider variety of materials, some trucks were retrofitted to pull trailers so that more compartments could be utilized for more categories of source-separated materials. Efficiencies were not the driver of the day as manual curb sorting and the loading of all these separate materials was very time consuming. Drivers spent most of their time parked curbside sorting materials.
Trucks in the next generation of technology were fondly referred to as “one-pass” vehicles because haulers did not want to send multiple trucks to the same stop. Primarily used for residential garbage and recycling collection, the one-pass trucks had compartments for both streams. Some were advanced, dual-compaction, split-body units. Others were garbage trucks with simple boxes and compartments added for newspaper and containers. The downside to one-pass technology: Differing material densities and volumes prevented an even loading of each compartment. In many cases the trash compartment filled first, forcing a disposal trip in the middle of the route with only a partially loaded recycling compartment. Many one-pass units are still in service in rural areas of the country where travel time to stops is excessive.
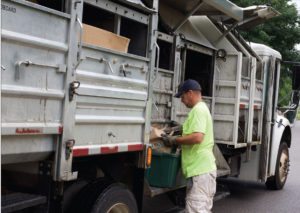
Manual curb sorting was a big part of drivers’ responsibility in the early days of municipal collection programs.
Legislation aside, haulers have always tried to improve on vehicle design. Even the trusty rear-end loader has been improved in unique ways. For instance, one rear-end load design featured a large loading hopper in the rear, which could be used to collect waste manually as well as lift containers, and its hinging pack blade and ejection panel design guaranteed a healthy payload.
The rear-end load design dictated a multi-person crew, however, because without a second person, the driver was forced to walk the length of the truck at every stop. In response to a desire for solo crews, body manufacturers moved loading hoppers to the curbside and chassis design incorporated right-hand and dual-drive steering configurations to save drivers some steps while keeping them safely away from traffic on the curbside of the vehicle. Although conducive to semi-automated lifting, manual lifting was a challenge with these new designs because even the lowest loading hoppers sat above the chassis frame.
Chassis and body companies worked together to develop the drop-frame configuration to provide for a loading hopper that would be easy to load manually while still providing a hopper large enough to accept waste and keep it in the truck. This meant cutting and reconfiguring the factory truck frames, resulting in an expensive retrofit. Still, drop-frame configured trucks have worked well in certain programs where a versatile one-person unit can collect carted materials, loose bulky items and even bagged yard waste.
Since the 1990s, many of the key changes to collection trucks have been evident only to the trained eye. Commercial front-end loaders were improved with better compaction systems; the half-pack was born when it was discovered that two smaller diameter hydraulic cylinders working diagonally and only traveling beyond the loading hopper generated more force than a single twelve-inch telescopic cylinder that traveled the full length of the body.
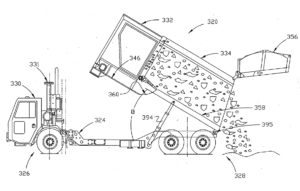
Drop-frame designs, like the one shown in this patent drawing, allow for a lower loading height and larger hopper for manual side-load collection.
Tailgate designs further improved compaction when garbage acted upon garbage and “flipped over” when it reached the tailgate. Half-pack payloads increased by more than 30 percent compared with similar sized full-pack vehicles. Other front-end loader innovations in the 1990s included a single joystick air control that improved productivity and driver ergonomics, programmable logic controllers (PLCs) to manage body systems, and creature comforts like auto-pack and back-of-blade sump clean-out drains, to name a few.
The turn of the 21st century brought with it the next major shift in collection innovation. Front-end loaders were adapted to collect residential waste and recycling when communities began the shift to rollcarts. Further innovation by Environmental Solutions Group (ESG) led to the introduction of the fully integrated, automated front-end loader (AFL) for residential collection.
Organics collection ushers in new approaches
The latest example of shifting vehicle design is a result of segregated organics programs. The high liquid content of organics has required a different approach to collection vehicle engineering. The need for water-tight compartments, different methods for cleaning, different compaction or no compaction at all have led some body designers away from platen-type vehicle compactor panels to rotary, auger-based compaction equipment or pendulum-based systems. Both of these innovations are designed to improve the handling of organics-only waste streams in an effort to prevent bypass and limit required cleaning. One example of this shift can be seen in technology from Scranton Manufacturing and its New Way line, which uses a screw-type auger for organics collection. Waste is loaded into a traditional automated side-load hopper and the screw, resembling a giant meat grinder, reduces the size of materials and drives it into the receiving body.
Labrie is approaching organics from a different angle. The Canadian manufacturer has developed a pendulum-packer design utilizing a hinged panel that is driven by exterior mounted hydraulic cylinders. The pendulum concept avoids areas where bypass can collect, eliminating the “behind-the-blade” clean-out process, which is made worse with source-separated organics. Expect to see even more variants on the collection-body side as organics collection programs develop and customers begin adopting the source separation of food waste and begin mixing it with their yard waste collection programs.
The most significant vehicle innovation currently under development is not visible to even the trained eye. The controller area network (CAN) innovation and its integration between chassis and body manufacturers represents the next level of vehicle intelligence.
Regulatory demands of lower emissions and higher fuel economy have created this shift toward computer controllers and electronic management systems. Historically, a separate loom of wire would be run to and from individual chassis systems to carry a basic set of information back to the dashboard. As independent electronic controlled systems such as automatic transmissions, engine control management (ECM), and anti-lock braking became more sophisticated and prevalent in modern solid waste collection vehicles, the method to move data between these systems needed an upgrade.
Most, if not all chassis manufacturers have adopted a system called CANbus, essentially a data superhighway with exits and on-ramps at each of these electronic systems around the truck. Rather than a separate set of wires going back and forth to each system, all these systems connect to the single CANbus, and the coded data packets know which exit and on-ramp to use to report on the individual system. The CANbus means less wire usage and fast, reliable data moving through a single controller.
How CANbus helps lift efficiency
Until recently, CANbus technology was something only your chassis technician really cared about, but it’s now something customers of the major chassis manufacturers should be asking about when considering a new purchase. As the data from these systems become more user-friendly, fleet owners can remotely diagnose vehicle issues, identify driver improvement opportunities and monitor vehicle performance. The integration of CANbus data and remote access is commonly referred to as telematics, and chassis manufacturers are investing in the infrastructure to support it. Mack Trucks, for example, has created GuardDog Connect, a remote data-monitoring platform that constantly monitors customer vehicles for maintenance issues such as fault codes, diagnostic needs, and maintenance records. The company can diagnose a vehicle issue remotely and have parts waiting at the corresponding dealer before the truck reports for maintenance.
Truck body manufacturers are also very interested in leveraging the possibilities of this emerging chassis data superhighway. Whether the body is front-end load, side load, rear-end load, or roll-off, the complexities of body design have increased dramatically as the demand for higher productivity has increased. Is the top door open? How many pack cycles did it take to reach capacity? How many arm movements were necessary to service a customer? These are just a few simple questions that can be answered with body system data.
But let’s add a twist. What was the position of the hoist, arm, or forks when the truck’s transmission was put in reverse? This is just one example of how a CANbus system can connect chassis and body, providing intelligence to fleet owners, operators and maintenance technicians. Body manufacturers are all working hard on CANbus integration in order to provide that same level of customer service uptime that chassis manufacturers are doing for their customers.
Electric and self-driving concepts
Another area that is being explored is the use of electric-powered collection vehicles. These units aim to be 100 percent electric, not hybrids or hydro-static vehicles, which have already made their way to market. The industry has always been concerned about weight and range with electric, but new things are happening in battery technology. It’s early in the process, but stay tuned.
Finally, many vehicle experts are currently discussing potential in autonomous or self-driven trucks. The mainstream media has often touched on Google cars driving themselves around Silicon Valley, and questions are being asked if we could possible see autonomous garbage trucks on U.S. roads.
It’s this author’s opinion that this type of system is many years away. The wonder of the human brain is its ability to recognize patterns and adapt. Computers cannot do that without a tremendous amount of input and programming.
Solid waste collection is a dynamic process that is influenced by the environment, road conditions and traffic, a changing waste stream, and the nature of the people around us. Removing the human element from such a fluid environment is a complicated undertaking.
And that human element remains central to the evolution of trucking technology. According to the Occupational Safety and Health Administration, solid waste operations continues to rank as one of the country’s most dangerous professions, but thanks to innovation and ingenuity, the tools for collection keep getting better and are making the job safer.
Don Ross is director of operations for Kessler Consulting Inc. and a 30-year industry veteran specializing in collection and transfer systems. He can be reached at [email protected] or 813-971-8333.