This story originally appeared in the August 2016 issue of Plastics Recycling Update.
Subscribe today for access to all print content.
There are promising signs that the plastics recycling industry in North America is beginning to develop an infrastructure to recover plastics other than PET and HDPE.
A variety of different companies are starting to scale up operations that focus on sorting out polypropylene and other plastic resins that have long been disregarded. These plants are aiming to show that even in a time of depressed markets, there’s economic viability in digging deeper into the plastics stream.
How are these companies finding their place in a recycling marketplace that’s already highly competitive? And what opportunities may open up as the trend toward richer domestic sortation continues to unfold? Read on for answers.
Seeing hope in mixed bales
In the U.S., the demand for recycled polypropylene (PP) has led to the emergence – even in a tight pricing market – of several operations that focus on recovering plastics from bulky rigid mixed plastic bales and from bales of plastics Nos. 3-7.
One operation that’s gotten plenty of attention is a $15 million, 140,000-square-foot plant run by QRS Recycling. The plastics recovery facility (or PRF) opened outside Baltimore in Dundalk, Md. last November, and its primary focus is sorting out materials from Nos. 3-7 bales that come from materials recovery facilities (MRFs), the plants that have traditionally been the last line of domestic sortation before bales went to reclaimers or overseas.
Meanwhile, another intriguing effort to more effectively separate recyclable plastics can be seen at a prototype plant operated by Titus MRF Services in Los Angeles. The so-called “secondary materials recovery facility” began operations two years ago and has the capacity to process 2.4 million pounds of material per month. Titus aims to triple the size of the plant, possibly by next January, in the hope that it can become the model for secondary MRFs in large U.S. metropolitan areas.
The Titus operation takes in baled materials that MRFs would otherwise landfill and separates out cartons, mixed plastics, small paper and plastics such as polystyrene and PLA as well as any other high-value recyclables that may have escaped the initial MRF sort.
A number of other varied players at different points in the plastics recycling chain are also beginning to focus on pulling materials out of mixed bales. Among them: plastic recovery and recycler Trigon Plastics in Ephrata, Pa.; plastics compounder and recycler Astro Industries in West Monroe, La.; and recycled plastic composites railroad tie manufacturer IntegriCo Composites in Sarepta, La.
Industry observers say the rise of secondary processors ultimately means more material diverted from landfill – and moved to operations hungry for post-consumer plastics. “These models offer great potential to get materials deeper in the stream,” said Patty Moore, president of Moore Recycling Associates, “and recover materials that haven’t been captured before.”
Reaching what MRFs cannot
So why are MRFs passing over these mixed plastic streams in the first place? The simple answer is that it’s difficult for most existing MRFs to add sorting stations and equipment. Many MRFs were built years ago and are already dealing with space limitations. Polypropylene is the third-most recycled plastic in the U.S., after PET and HDPE, but PP volumes are still too low for many MRFs to justify the costs required to set up additional systems.
“If MRFs were going to [add] another material type, they would need another sort station, additional equipment and more manual sorting, and they also would have to tie up more linear space on their floor,” said Will Sagar, executive director of the Southeast Recycling Development Council (SERDC).
However, a variety of factors are allowing PRFs and secondary MRFs to economically separate and reclaim mixed-plastic materials.
First, they can amass materials (bales) from an endless number of MRFs to get the volume needed to be economically viable.
Second, they are starting from scratch with focused designs. The flow of materials and equipment within their plants differs from what is seen in a traditional MRF. In most cases, these newer operations focus first on pulling out PP and then any residual HDPE and PET that was missed by MRFs and wound up in that 3-7 bale.
The PP component is critical to the economics at the foundation of secondary processors.
At the Plastics Recycling 2016 conference in New Orleans earlier this year, a session detailed the recent rise of PP in the domestic market. Greg Janson, CEO of QRS Recycling, noted from stage that the amount of PP in mixed 3-7 bales “is what supports” the economic viability of PRFs. “We need 39 percent of the 3-7 mix to be polypropylene to make sorting worthwhile.”
Equipment and efficiency
Sortation technology is also a big piece of the puzzle.
“There is more intensive use of optical sorting equipment at PRFs and secondary MRFs,” said Scott Mouw, a top environmental official for the state of North Carolina. “They are almost a hybrid between a MRF and a reclaimer that sorts out either PET or HDPE. They have to have the equipment of both.”
In fact, some observers say equipment innovation has had just as much to do with the rise of secondary sorters as market forces have.
“There have been some pretty good advances in technology in the last few years that have made it possible for PRFs to emerge,” said Byron Geiger, president of reclaimer Custom Polymers PET in Alabama. “There is better optical sorting equipment and better disc screens. … They are running some pretty serious volumes through these plants.”
Titus, which operates the prototype secondary MRF in Los Angeles, is in fact an equipment company first and foremost. When company representatives saw material that was not effectively captured in the MRF environment, they decided to try to leverage their tech expertise.
“We took our own patented equipment and combined it with top-of-the-line, state-of-the art infrared optical sorters [made by other companies] and set up a sort with air streams, sizing screens and optical sorters,” said Mike Centers, president of Titus.
While reliance on technology tends to mean higher costs, companies in the secondary sortation space appear to be finding ways to make operations pencil out, even in the current tight pricing market.
“Secondary MRFs and PRFs rely more heavily on auto-sorting, so their initial capital costs are higher,” said Moore. “But their operating costs are lower because they don’t rely on hand-sorting.”
Another critical element to PRF success is how the sort line is organized.
“Because we consolidate volume from across the eastern half of North America, we are able to invest in more advanced sorting and washing technology, and then sequence that technology in such a way that yield is maximized,” said Dave Bellon, managing partner of QRS Direct, the sourcing arm of QRS Recycling.
That sentiment was echoed by Centers of Titus.
“The order and sequencing is critical,” he says. “You can’t hit high purity levels without the right sequence.”
A domestic market in development
The growth of PRFs, secondary MRFs and other companies that sort out plastics Nos. 3-7 in the U.S is likely to continue because the demand for those materials is growing, according to experts.
In 2013, as China’s Green Fence customs crackdown was taking hold, domestic PRFs and/or reclaimers bought more than 50 percent of the post-consumer mixed resin rigid bales generated by MRFs in the U.S. and Canada for the first time since Moore Recycling Associates began tracking that information in 2007 (the company prepares reports annually on the subject for the American Chemistry Council).
Moore said she expects tonnages of post-consumer mixed-resin bales purchased by domestic PRFs and reclaimers to “more than double in the next few years” from the roughly 260 million pounds those domestic PRFs and reclaimers purchased in 2014.
What exactly will the secondary-processing landscape look like as this market develops? Steve Alexander, executive director of the Association of Plastic Recyclers, said the industry will likely continue to see a mix of different approaches, and he noted PRFs and secondary MRFs each bring advantages.
“I don’t favor one over the other,” Alexander said. “Both are extremely beneficial to generating good-quality material for the industry. These secondary sorting facilities provide material to reclaimers that otherwise wouldn’t be available. … They have been a boon for the industry, especially for PP reclaimers.”
Mimicking the transfer station model
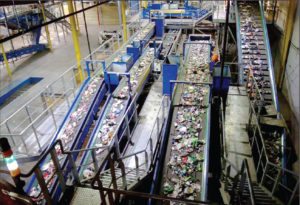
QRS Recycling opened a $15 million plastics recovery facility outside Baltimore last November.
Whether PRFs or secondary MRFs – or both – emerge to help expand the supply of recycled plastics, it’s clear that the groundwork is being laid for that deeper sortation infrastructure to ultimately take root.
“We are seeing a lot of efforts today to develop hub-and-spoke models for plastic recycling,” said SERDC’s Sagar. “We’re seeing efforts to aggregate materials for plastics recycling that are similar to how solid waste disposal developed transfer stations to get materials to regionally owned landfills.”
QRS leaders said they believe their company can serve the eastern half of North America from its PRFs in Maryland and St. Louis and that they have found end markets for most plastics except PVC and PS. The company had a third operation in Atlanta, but it shut that down in May after moving that plant’s production to the newer Baltimore-area operation, which has the capacity to process 9 million pounds of material monthly.
QRS has close to 300 suppliers, the majority of them MRFs. But it also gets HDPE bales from its PET customers, and PET bales from HDPE customers when the pricing is right.
However, there is currently still a gap in infrastructure from Texas to California and up the West Coast to Seattle, said Scott Saunders of Alabama-based KW Plastics Recycling Division, which buys PP from both QRS and Titus.
“PRFs are filling the needs of providing more material and most of that is staying in the United States on the East Coast,” Saunders said. “But there is a huge opportunity on the West Coast because there is not a PRF there and there are a lot of people from Phoenix to California and up to Seattle that are underserved.”
Filling that void is part of the Titus strategy. The company’s Los Angeles secondary MRF, which was set up in an old MRF that was no longer in use, currently employs 20. But Centers anticipates that the workforce will increase to 50 when the plant, at a cost of $3 million, is scaled up to a capacity of 7 million pounds per month, possibly by early 2017. Centers said the operation salvages about 50 percent of the material in bales and that he is able to find end markets for all the plastics except PVC and PET clamshells.
Titus is in discussions with three cities to set up secondary MRFs, and Centers said the volume of materials from three or four major MRFs in a metro area is what’s needed to make his model sustainable.
“If we can get material from MRFs that collect blue bin material from roughly 875,000 households and 3.125 million people, we can succeed,” Centers said. “This is not a regional solution, but a metro-based solution designed to allow the MRF structure to sort out the seven big commodities – PET, HDPE, aluminum, mixed paper, metal, glass and old corrugated containers – while the secondary MRF, with a new design, sorts out what the first MRF chooses not to sort by material type.”
Critical nature of end markets
Of course, whether expansion to the West Coast or elsewhere takes place ultimately may depend on factors beyond the control of MRFs, PRFs, secondary MRFs or anyone else in the sortation sector.
“The potential for growth is high,” said Bellon of QRS. “But future growth is no longer about the ability of the industry to recover these materials because we can do that. Future growth all depends on the end markets. We need the consumer product brands to commit to the use of recycled materials for the market to really take off.”
If those end markets are able to support the secondary processing push, the financial and environmental payoffs could be significant.
“This is the new frontier in recycling because we can divert at least half the materials that MRFs would just send to landfills, create jobs and divert materials to their highest possible end use,” said Centers. “This is a sustainable way that we can build on the existing infrastructure.”
Mike Verespej is president of MAV Business Communications. He can be reached at [email protected] or 440-973-4159.