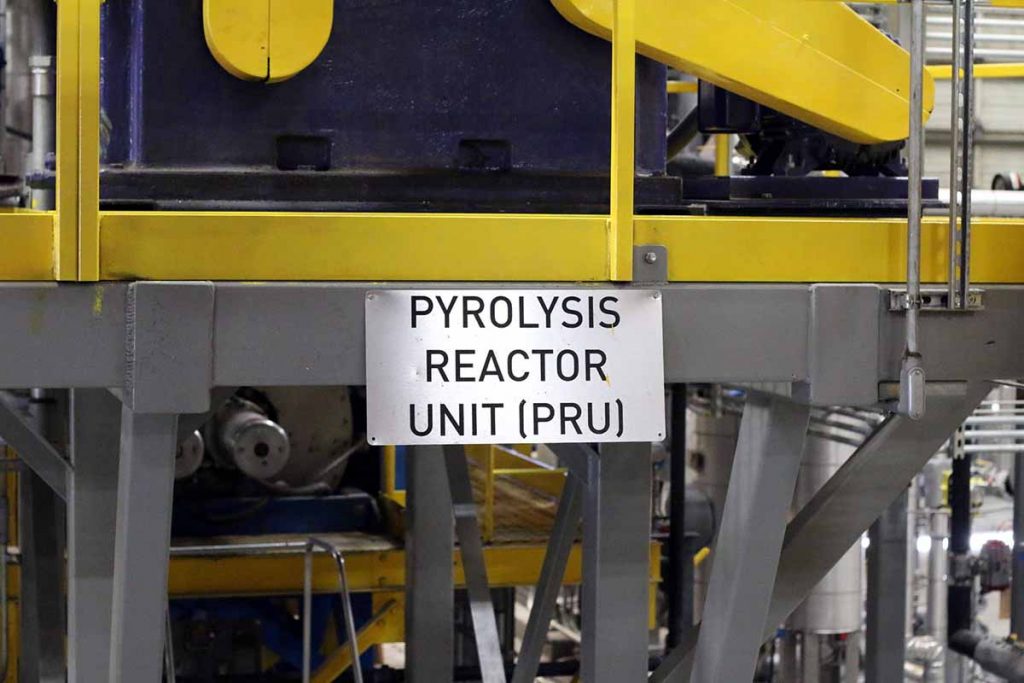
The author makes the case that conversion technologies have a positive environmental impact on managing plastic waste.
If{/dropcap] there is one thing I have learned in my career as a practicing engineer, researcher and educator, it is this: You have to actually see, investigate and work with technology to make a credible assessment of its potential impact. Furthermore, impacts should be measured and incorporated into life cycle analyses.
The question I’d like to address here is: On a life cycle basis, is the overall environmental impact positive or negative when it comes to using advanced recycling technologies (also called chemical recycling) to convert plastic wastes that would otherwise end up in a landfill?
The answer is the net impact is positive. And my perspective stems from nearly 15 years of in-depth, hands-on research on varied waste conversion technologies.
Prior to taking my current position with the City College of New York, I was an associate professor at Columbia’s Earth & Environmental Engineering Department, and before that, I worked in industry for 10 years. I have collaborated on wide-ranging research across the globe, looking into catalytic reactor development, combustion modeling, technology development and more. I have seven patents and two pending applications in the areas of catalysis and combustion and have authored over 100 peer-reviewed publications.
It is through these experiences that I am providing this perspective. The reason I am doing so is because, in general, there is far too much mischaracterization of some plastic recycling technologies and processes. The unfortunate result is confusion among policymakers, regulators and potentially the public.
An important aspect is that my team and I physically visit and work closely with the engineers and inventors of operations. We have assessed numerous technology development companies and laboratories all over the world. Many of those companies request that we quantitatively evaluate their system and suggest possible process improvements. To arrive at quantitative assessments of impacts requires site visits and direct contact.
Specific to conversion technologies (thermal or chemical), my experience and the data convince me they have a significantly positive environmental impact on managing plastic waste.
Mismatch in supply and demand
Currently, there is a mismatch between the availability of recyclable plastic waste and the ability of markets to absorb it. For example, according to a recent analysis from the City College of New York, only 48% of plastics in New York City’s blue bins get recycled through traditional recycling methods.
What happens to the other 52%? There are only two options: landfill or conversion to some other product such as energy, synthesis gas or pyrolysis oil. Clearly, in this example, it is a positive impact to employ technologies that convert that plastic waste into something useful instead of going to landfill.
It is also important to acknowledge that conversion technologies produce emissions that are released into the environment, resulting in some negative impact (keeping in mind that emissions are produced by all waste management processes, from reuse to mechanical recycling to chemical or thermal conversion to disposal in landfills).
But it serves no good purpose when organizations or uninformed individuals make claims of “toxic emissions” being produced. We need to look at what the emissions actually are and see how they compare to the regulatory limits established by credible institutions such as the EPA and state environmental protection agencies.
A review of the published literature reveals that emissions from conversion processes, such as plastics-to-fuel, are lower in terms of volatile organic compounds and particulate matter, nitrogen oxides, sulphur oxides, and carbon monoxide than they are at food processing plants, hospitals, universities and automotive manufacturing facilities.
The Earth Engineering Center, which I direct, has reviewed technical reports on numerous gasification and pyrolysis technologies, and we have also conducted our own research. The center has found that all the analyzed processes emit below the regulatory limits that have been established for the respective systems.
But back to the ultimate question: On a life cycle basis, would the overall impact on the environment be positive or negative when deciding to use conversion technologies on plastic wastes that cannot be or are not mechanically recycled? Rigorous, peer-reviewed engineering and scientific studies have overwhelmingly found it is a positive impact.
Of course, many of these developing technologies are just that: still developing. All technology takes time to mature into a commercial system robust enough to be launched and relied upon for continuous operation for years at a time.
Technologies that are and have been developed to convert waste into something useful have an additional challenge. The feedstock (waste stream) is variable and has significantly changed over the years. For example, more attention has been given to collection, sorting and pre-processing systems to extract valuable products. That extraction, though a positive thing, materially changes the input, thereby requiring adjustments to the conversion technology.
If a mixed waste stream could be completely separated into consistent, mainly pure streams of specific items (such as hard plastics, film wrap, paper, corrugated board, etc.) then it would accelerate the development of these technologies. They could be designed to accept a fairly narrow category of feedstock.
To date, however, pure stream separation has proven prohibitively expensive and faces significant technology challenges. That doesn’t mean we should stop trying. After all, past failures are lessons for future success.
Misunderstanding toxicity
I’d also like to address a false premise about the outputs of conversion technologies used to synthesize waste streams. It goes like this: Materials entering a given system can affect the make-up of the final product; therefore, toxic materials entering the system will result in toxic substances in finished fuels or chemicals.
This is simply not correct.
The main goal of companies developing conversion technologies is to produce a final product that meets certain specifications. All technology developers recognize that the production of a fuel or chemical that has unacceptably high levels of contaminants, compared to the specifications, will have major implications for a potential buyer and user.
That applies not only to specifications designed to protect the environment, but also those designed to protect the equipment. Specifically, fuels must meet very specific viscosity, smoke point, boiling point, and halogen, oxygen and metal content for engines to perform properly.
Chemicals made from waste streams must meet stringent specifications for downstream refiners or manufacturers to accept them, because those users have billions of dollars of infrastructure at stake and have multiple options for feedstock. From our research, it is clear that conversion processes are designed to deliver products well within these consumers’ stringent expectations.
The reality is we have a waste problem in the world. So we need to consider all options to safely and sustainably manage the enormous amount of waste that you and I generate – nearly four pounds per person per day.
The decisions we make about which options to use should be backed by reliable scientific data. When misinformation is used to mislead our decision-makers and the general public about these options, we run the risk that these options will be taken off the table.
Ultimately, the common objective must be to divert as much waste as possible from landfills, recover as much material and energy as possible from the waste stream, and recirculate it through the economy.
Marco J. Castaldi, Ph.D., is a professor of chemical engineering at the City College of New York. He is a Fulbright Global Fellow and Technical Fellow of the American Society of Mechanical Engineers (ASME) and the American Institute of Chemical Engineers (AIChE).
This article originally appeared in the Winter 2021 issue of Plastics Recycling Update. Subscribe today for access to all print content.