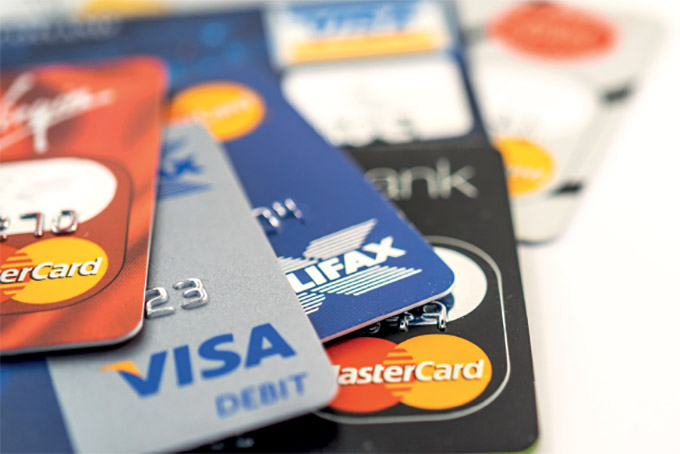
The action toward more environmentally friendly products is involving major players in the payment-card industry.
It used to be that “green payments” meant dollar bills, but not anymore.
The payment-card industry has tapped into new technologies and alternative materials to reduce the consumption of natural resources in card production. This trend has included more use of recycled plastic content and shifts to new materials altogether.
Biggest brands are involved
The action toward more environmentally friendly products is involving major players in the card industry.
Mastercard has partnered with manufacturers IDEMIA and G+D Mobile Security GmbH to create the Greener Payments Partnership. This program will work to establish environmental best practices and reduce virgin PVC plastic in card manufacturing at scale.
American Express, meanwhile, has set the ambitious goal of issuing corporate and consumer credit cards manufactured from recovered ocean plastic pollution.
Along those same lines, CPI Card Group Inc. recently launched Second Wave, a payment card aimed at reducing use of virgin plastic and diverting plastic waste from entering the ocean. The company estimates that for every million Second Wave payment cards produced, over 1 ton of plastic will be diverted from entering the world’s oceans, waterways and shorelines.
And Bilcare Research Srl launched a card-grade substrate made from 100-percent recycled PVC – the product is called called SICO-R.
“We were looking for a way to address environmental concerns, and since we are running PVC-centric technology, we came up with the idea to recycle PVC,” said Marco Balatti, sales and marketing manager at Bilcare. “It’s a material we know very well and the recycled PVC works in our manufacturing processes.”
Similar action has come from global plastic film supplier Klöckner Pentaplast. It recently created the Positive Plastics Pledge, a plan that outlines its current commitments and further sustainability goals for the next 10 years.
Two card-related components are included in the plan: Pentacard SecondLife, which has a high percentage of post-industrial content, and Pentacard kpLonglife, an overlay which creates more durable cards and extends their life.
“The Positive Plastics Pledge calls for solutions that are more sustainable, provide excellent performance and create greater value for card manufacturers and their customers,” said Kent Sides, global corporate accounts manager, cards at Klöckner Pentaplast.
An eye on new materials
At the same time, card stakeholders are rolling out innovations geared toward shifting the very foundation of how cards are constructed.
Karen Brooker, vice president of sales at Plasticard-Locktech International (PLI), noted the company is experiencing increased interest in non-PVC plastics and paper substrates. She said it’s a reaction to marketplace demands around sustainability.
“Cards are highly visible to the consumer,” Brooker said. “When a card issuer reduces its impact on the environment with a change to card construction, the value of the brand is elevated in the eyes of environmentally conscious consumers.”
Corporate and community initiatives to reduce or eliminate plastics have fueled the shift for some brands away from PVC to durable engineered paper. “Paper can be a fantastic alternative for gentle-use cards and cards with a short life cycle,” Brooker said. “But sustainable plastic resins are preferable for heavier-use cards, cards that will be exposed to the environment and cards that are intended to have an extended life.”
While demand is increasing for greener card options, the industry still has several challenges to overcome before they become mainstream. The cards must be durable, secure and live up to the technological requirements of modern cards, which are no longer simple plastic rectangles.
Brooker said alternative materials generally come with drawbacks. For decades, card manufacturers have been engineering card products to comply with ISO/IEC 7810 and related international standards. Products made from alternative materials may not fully comply with ISO/IEC 7810. And recycled-content films, especially recycled PVC, can present challenges to the film producers.
“There is often limited supply of suitable recycled materials, which runs counter to the card issuer’s desire for a high percentage of recycled content in the finished card,” said David Tushie, CEO of Magellan Consulting, Inc. “Additionally, recycled content often needs additional processing for successful film production, making the card more expensive than the standard product. Finally, contamination of the waste stream seems to always be an intermittent issue.”
One of the biggest challenges when dealing with alternative materials is getting a good bond between the layers that make up the finished card. “In traditional card construction, PVC layers form a chemical bond during lamination,” Brooker of PLI explained. “Non-PVC alternative materials may require the investment of significant research and development on the part of the manufacturer in order to achieve the minimum required bond and even a fully developed product is unlikely to have the bond strength and dependability of PVC.”
No matter what a card is made of, it has to be durable and live up to the technological requirements of modern cards – including EMV chips and contactless capacity – and stringent manufacturing standards. For example, wood-based cards can’t be embossed, and bioplastics require entirely different laminating materials and adhesives than what is used with PVC.
“The goal isn’t to make 100,000 cards, but to develop a viable alternative for the billions of cards out there,” Tushie said. “The greatest current trends seem to be increased use of metal cards (reduced PVC content) and plastic cards with recycled and/or reduced content. A lot of development work continues in alternative bio-based plastics like PLA and bioethylene PVC, but the widespread use of these materials is still somewhat in the future for card manufacturing.”
New card designs may require card issuers to accept products that have different characteristics going to the user. For example, sustainable cards may be slightly lighter or have a different feel than the traditional product. More flexible cards may be mistaken as “light and flimsy,” dreaded adjectives for a card product in today’s market, which values a decided “thunk” factor.
Regardless of the challenges that eco-friendly cards present, the trend toward alternative materials will ultimately be a positive change for the industry and the planet.
“The heightened sense of interest in sustainable/recycled content over the last several years is due to a greater sensitivity and awareness in general to climate change issues,” Tushie said, “but some is also due to better economic growth and a desire to contribute to the sustainability of the planet.”
Jeffrey E. Barnhart is founder and executive director of the International Card Manufacturers Association (ICMA).
This story originally appeared in the Fall 2019 issue of Plastics Recycling Update. Subscribe today for access to all print content.