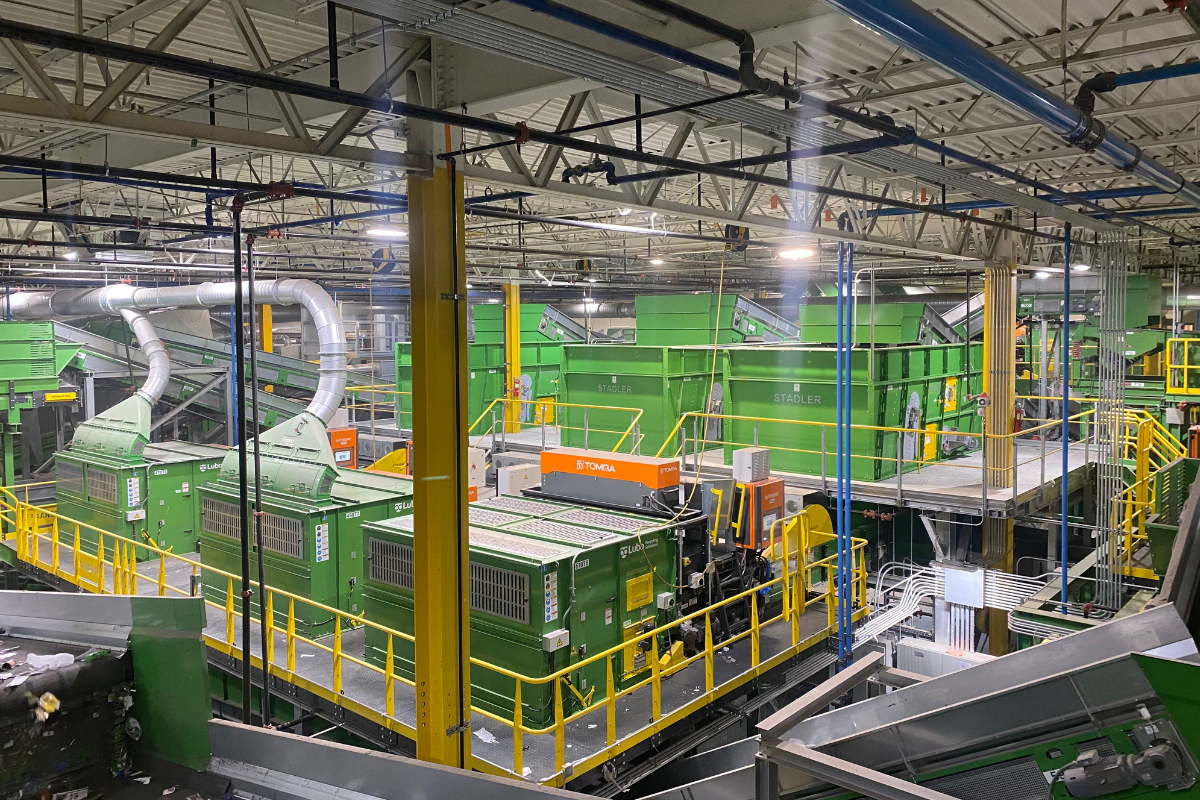
The recent upgrade of WM’s Germantown MRF in Wisconsin added 20% more capacity to one of the company’s largest facilities in the heart of a rapidly growing manufacturing corridor. | Courtesy of WM
With a nearly $39 million upgrade completed at one of its biggest MRFs, WM officials are looking to further refine automation capabilities as well as add volumes in the Midwest.
Although optical sorters are extremely sophisticated, WM has seen an uptick in textiles come through the sorting lines.
“One item on our to-do list is to improve the differentiation between PET and polyester (fabric),” said Frank Fello, area vice president of the Upper Midwest, in an interview during a recent Resource Recycling tour of the MRF.
Some buyers have told Resource Recycling that PET bottle bale yields are lower from any automated plant, containing only 50-55% PET versus the industry standard of 60%. However, several sellers including WM have said they do not see a decrease in quality in the final bale contents.
One difference Fello has seen since relocating to southeastern Wisconsin is the level of community buy-in.
When he worked in the Great Lakes region of WM that includes Michigan, Indiana and Ohio, the contamination rate of collected volumes was around 18-20%. In comparison, in Wisconsin the rate is much lower at around 12%, he said.
“People here want to recycle,” he said. “Sometimes that can be an uphill push.”
In Germantown, paper and OCC constitute about 60-65% of volumes processed there, as is typical for MRFs, according to John Schultz, recycling facility manager at Germantown, who led the tour.
Brent Bell, vice president of recycling for WM, said in a later interview that much of the Wisconsin facility’s baled material remains local, with “a lot of really great, strong recycled paper mills” nearby.
Packaging manufacturer Uline is headquartered in Pleasant Prairie, Wisconsin, about 50 miles from the MRF, and has two 1-million-square-foot warehouses that supply its regional distribution centers.
Uline offers paper and plastic bags and boxes containing varying amounts of post-consumer fiber and resin, according to the company website.
Plastics compounder Rehrig Pacific has a manufacturing plant in Pleasant Prairie as well, and corrugated box maker Smurfit Westrock also is building a plant there, though how much recycled content the facility may use hasn’t been made public. In addition, Green Bay Packaging recently broke ground on a plant expansion in Germantown.
“Our focus is on making sure we have good end markets, because we don’t have a lot of room to store material,” said Bell. “We’re working on doing a better job of storytelling, investing in recycled paper mills that can only take cardboard boxes, not trees or woodchips, so that supply chain is very important.”
While the Germantown plant was shuttered, most waste volumes were diverted to the company’s Chicago facility about 120 miles away, Bell said.
“Chicago was able to handle it, and that provided a nice relief valve,” Bell said. “Now that Germantown is back up, Chicago is looking for more volumes.”
Additional volumes could come from third-party haulers that may not have their own processing capabilities, he said.
“Third-party haulers are big customers of our MRFs – counties, competitors and so on,” Bell said.
During MRF upgrades, WM works to ensure that recycling volumes stay out of landfills, he said. Nevertheless, WM executives cited factors including downtime at four of its recycling facilities for a 3% decrease in overall volumes collected in 2022.
“We’ll always have a plan B in place to make sure those volumes are processed. They may need to be trucked further than we’d like, but we definitely want to keep those curbside programs in place,” he said.
Beyond Wisconsin
WM looks to future needs when upgrading its facilities, Bell said.
“All of our facilities have extra capacity by design,” he said. “We’re building them for the next 10-15 years, so capacity is really high. So even though the Germantown plant is one of the largest, it’s not running at full capacity. As volumes in communities grow, we can continue to serve without any disruption.”
Between 2022 and 2026, WM will upgrade or build 40 facilities and add 2.8 million tons of capacity. But the company will continue to invest beyond 2026 as well, Bell said.
Pittsburgh, Atlanta and Germantown were the first three retrofits completed this year, Bell said, while more are underway in Philadelphia; Sacramento, California; and Elkridge, Maryland.
Of the 13 facilities slated for work in 2024, two will serve areas where WM is not currently active – Fort Walton, Fla., and Portland, Ore.
The Fort Walton facility will service the Panhandle region, Bell said. “No one processes in that area right now,” he said. “It’s definitely a new market, and right now the tons are going further out to be processed or not at all.”
Because the recycling stream continues to evolve, WM chose equipment that could keep up with those changes.
“We want to be able to program those changes into the optical sorters,” Bell said. “Having technology we can adjust in a very short amount of time will be very helpful in the future.”
A handful of very large facilities including Germantown have 230,000 tons of annual capacity, while locations including the upcoming Fort Walton site are on the smaller end of the scale, Bell said. The Germantown upgrade added 20% more capacity.
The size of the facility is the biggest factor in deciding what equipment will be installed. WM employs a combination of off-the-shelf equipment and bespoke machinery, using components from various vendors, he said. The upgraded Chicago MRF – whose design WM patented – provided a blueprint for full automation at future WM facilities, with the company showing its engineers the features they liked from each component.
“We’ve built that design again, in Seattle and in Elkridge, Maryland,” Bell said.
The Portland MRF is expected to start up by the end of 2024. Public comments are due by July 26, and Bell said he didn’t see anything that could potentially change based on public comments.
“Hopefully they are all positive, and it’s clearly needed capacity,” he said. “Hopefully we’re welcome.”
Fires: Ever-present danger
Since reopening in February, the Germantown MRF has experienced seven small fires, according to Fello. As with many fires at recycling facilities, improper battery disposal is often to blame.
“It used to be pool chemicals and hot coals that started the fires,” Fello said, adding that fires take place throughout the supply chain, from collection trucks to the tipping floor to the machinery.
Those hazards still exist, but household batteries including lithium-ion versions are an ever-growing problem, he said.
As advanced as automation has become, it cannot yet detect batteries. “Give the optical sorting companies a few years to start utilizing AI to get that capability, but we’re not there yet,” Schultz added.
A version of this story appeared in Resource Recycling on July 23.