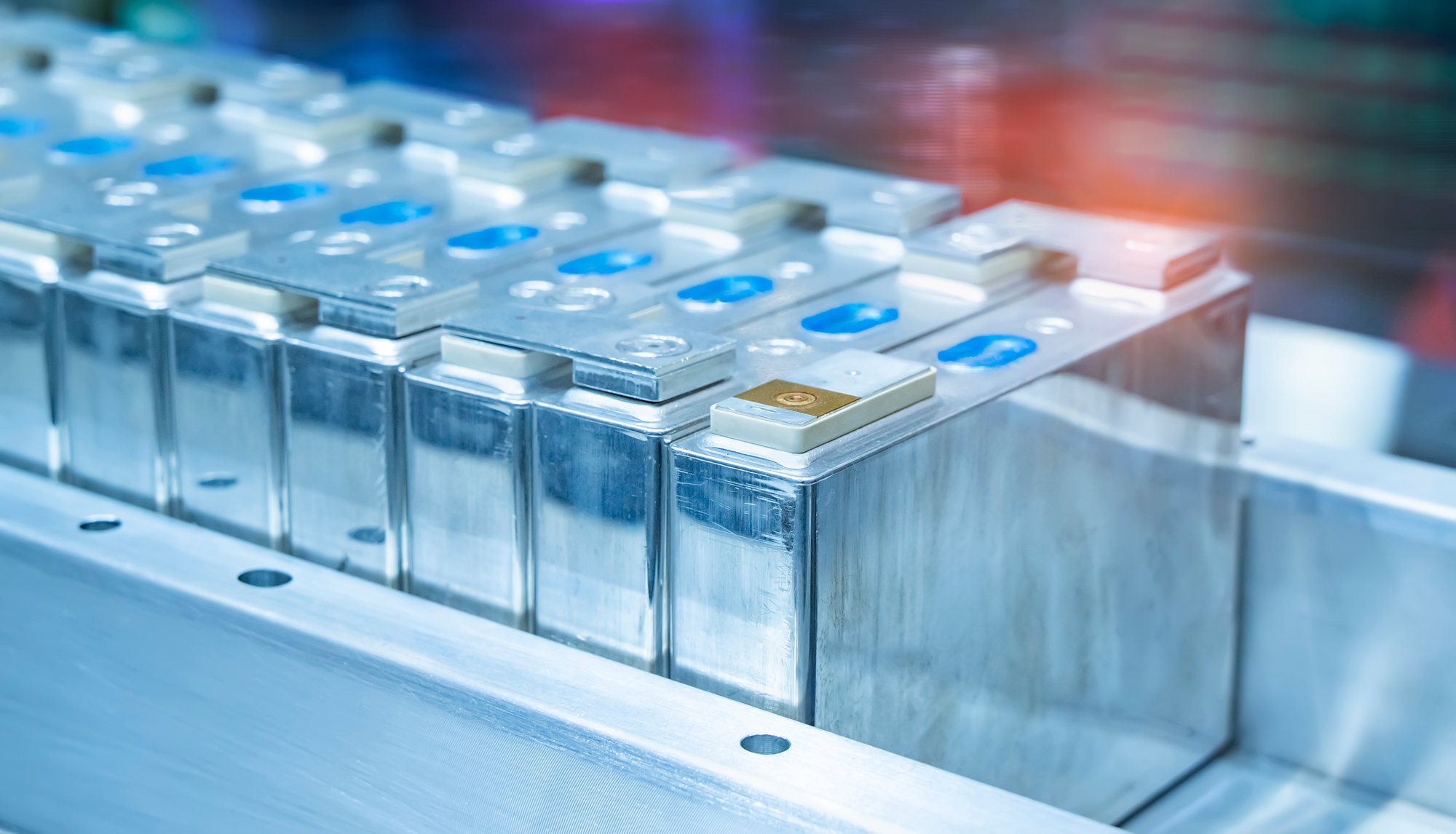
asharkyu/Shutterstock.
This article appeared in the 2024 issue of E-Scrap News. Subscribe today for access to all print content.
For recyclers involved with the rapidly expanding lithium-ion and lithium iron phosphate (LiFePO4) battery recycling market, there is an ongoing debate within the industry concerning the merits and pitfalls of dry versus wet, or water-based, processing.
Although dry battery recycling systems are prevalent, these typically require the disassembly of packs or modules and discharge of the individual battery cells before further processing and can be at risk of thermal events. Wet systems have distinct advantages in this regard and can be very efficient at recovering the most valuable materials but are largely misunderstood by those who may not be aware of recent advancements.
Industry professionals are still largely undecided as to which method can be utilized most efficiently and cost effectively to meet their reclamation safety, quality, and production goals, and there is some confusion over the role of dry and wet battery recycling methods. For example, I’ve heard some say wet processing is not feasible for Li-ion and LiFePO4 recycling, which is simply untrue. In many ways, it is safer, faster, and more efficient for recycling battery packs than dry processing — not to mention it is already being successfully implemented over the last seven years in multiple plants around the world.
The Pros and Cons of Dry Recycling Systems
Despite the prevalence of dry battery recycling systems, there are several disadvantages. To start, the variety of batteries that must be dismantled from packs and discharged can make a dry system prohibitive from a cost and return-on-investment standpoint.
The reality is that there is tremendous variation in the sizes, chemistries and construction of Li-ion and LiFePO4 batteries sourced across the globe, with essentially a thousand different arrangements and assemblies. The extent of the variety complicates creating battery recycling systems, since there is no standardization in approach. Today, all the battery packs are built differently, so there is no single method for discharge. If we could go back 30 years and start lithium battery design over, we could perhaps build a system with standardized methods and circuitry to allow for quick and easy discharging, but we are well past that point.
Since every battery cell must be discharged, there is often no easy, economical, profitable way to do it. In one method often used in the past, batteries are placed in a salt solution for several weeks to discharge, but this is messy, requires excessive space and produces a chemical effluent that must be properly disposed of. This too often requires disassembly labor and its dangers.
With dry systems, there can also be safety issues related to battery discharge. Outside of a lab, there is no practical or certain way of knowing if all the cells are fully discharged. In a large battery pack with thousands of cells, it is quite likely that at least a couple of cells can still be partially charged and create an unwanted reaction.
When dry processing Li-ion and LiFePO4 batteries, it can be very challenging to control dangerous conditions like thermal runaway, self-generating oxygen that can lead to hazardous battery fires. Although robots could theoretically dismantle, discharge and process the batteries, programming them to accommodate the wide variety of battery sizes and types would be cost-prohibitive.
Dry battery recycling systems tend to be smaller to limit the volume of combustible material and the danger of thermal runaway, so they may not always meet throughput needs enough to be profitable.
A further difficulty is that battery manufacturers are now increasingly filling their packs and modules with a glue-like gel as a safety precaution, to keep the case together in case of damage from a collision or drop. However, this makes battery disassembly even more complex. Even the companies that manufacture them have no method of disassembly.
With a dry system, battery materials also get into the air system in large volumes during shredding and processing. Treating or separating these airborne materials is more difficult as well as more costly and dangerous. You face a tougher environmental challenge using a dry system because the battery electrolyte and VOCs that are more voluminous are now in the air system, along with your inert gas. So you have to filter, scrub and oxidize them off.
The Pros and Cons of Wet Recycling Systems
Due to the rapid pace of change in battery recycling technology, there are several common misperceptions regarding wet battery recycling systems today, even among industry professionals.
Among the most pervasive misunderstandings is that wet systems are not capable of removing black mass. In Li-ion battery recycling, black mass consists of electrode coatings like metal oxides and carbon, which contain valuable elements like graphite, manganese, cobalt, nickel and lithium. Recovering the black mass generates the greatest value for reuse or sale since otherwise there are usually only trace amounts of metals like lithium, copper and aluminum.
A closed wet battery recycling system can capture black mass more effectively and at far improved purity if properly designed and built by companies experienced with these techniques. All the other particles besides the black mass are very large, so it is relatively easy to filter and press out, dewater and dry. The result is very clean, usable black mass, with the water able to be reused, utilizing a continuous water treatment system. We essentially cut and agitate the materials through the whole process to liberate the black mass from the foils in an aqueous solution and capture them without all the remnant plastics and particulate.
A turnkey wet Li-ion battery recycling system should combine several separate but complementary processes. The primary system shreds the batteries in inert atmosphere and water, and secondary systems further reduce the material to smaller, more separable sizes. The key is specialized secondary shredding, a factor not well understood yet throughout the industry.
When you try to recirculate the material through a standard shredder with a screen, the material blinds and clogs the screen. However, a specialized shredder can be used to further reduce the material to a uniform size without the need for a screen. If you can’t do that in one pass, it takes multiple shredders to get the same product at far greater expense.
In the LithiBatt system, this secondary shredding step is accomplished using its patented Triplus knife technology that reduces the material size to three-eighths of an inch. The knife technology is uniquely suited to wet battery recycling because it reduces to a predictable and regular size in one pass without screening, eliminating the concern over blinding.
Additional processing using proprietary chemical injections and drying methods captures valuable battery cell black mass from the shredded material before it goes through the entire system.
We are currently using a proprietary wet process to shred the biggest EV packs still charged for the world’s largest EV maker, and successfully collecting black mass.
The use of water in processing Li-ion and LiFePO4 batteries has other significant advantages, beginning with increasing safety by deterring thermal runaway. Since the recyclable Li-ion battery material does not readily absorb water, it can be used to cool the materials and quash incipient fires. Combined with nitrogen to eliminate combustible oxygen, we can control and eliminate thermal events with a wet process. By preventing thermal events, processing is faster with higher battery weights and volumes possible.
The glues or gels tend to float, so they can be easily handled in a wet recycling system if you have the ability to shred whole packs and whole modules all at once. In addition, a wet system can capture VOCs in the water, which can be filtered, so air filtration can be simple with just a scrubber and charcoal filter.
If there is a drawback to wet battery recycling systems, it is that it involves several separate stages that must be sufficiently integrated by an experienced manufacturer. Consequently, manufacturers and recycling professionals usually will want an industry expert involved from the start, so a system can be built that is customized to their specific needs. However, once installed, Li-ion and LiFePO4 batteries of all sizes and chemistries can be quickly and profitably reduced into valuable, reusable or saleable materials without disassembly.
This type of flexible wet system can recycle tons of Li-ion or LiFePO4 material per hour to whatever sellable state is required. If you need to produce tons per hour instead of a fraction of a ton per hour, hydro/nitrogen systems will get you there much faster than a dry system.
For industry professionals still undecided about whether to consider a dry or wet battery recycling system, they should inquire about both, weigh the pros and cons for their goals, then move forward with the system that best fits their needs. There are several different ways to design a Li-ion and LiFePO4 battery recycling system, but the decision should be based on the facts and a good understanding of dry versus wet, as well as the types of advanced systems that are already being operated by some of the largest battery manufacturers and recyclers in the world.
John Neuens is an industrial consultant for Wisconsin-based LithiBatt, a division of BCA Industries. LithiBatt provides both dry and wet, turnkey, closed loop, recycling systems for Li-ion, LiFePO4, nickel metal hydride, zinc-bromine and other types of batteries. For more information, call 414-353-1002, email [email protected] or visit bca-industries.com.
The views and opinions expressed are those of the authors and do not imply endorsement by Resource Recycling, Inc. If you have a subject you wish to cover in an op-ed, please send a short proposal to [email protected] for consideration.