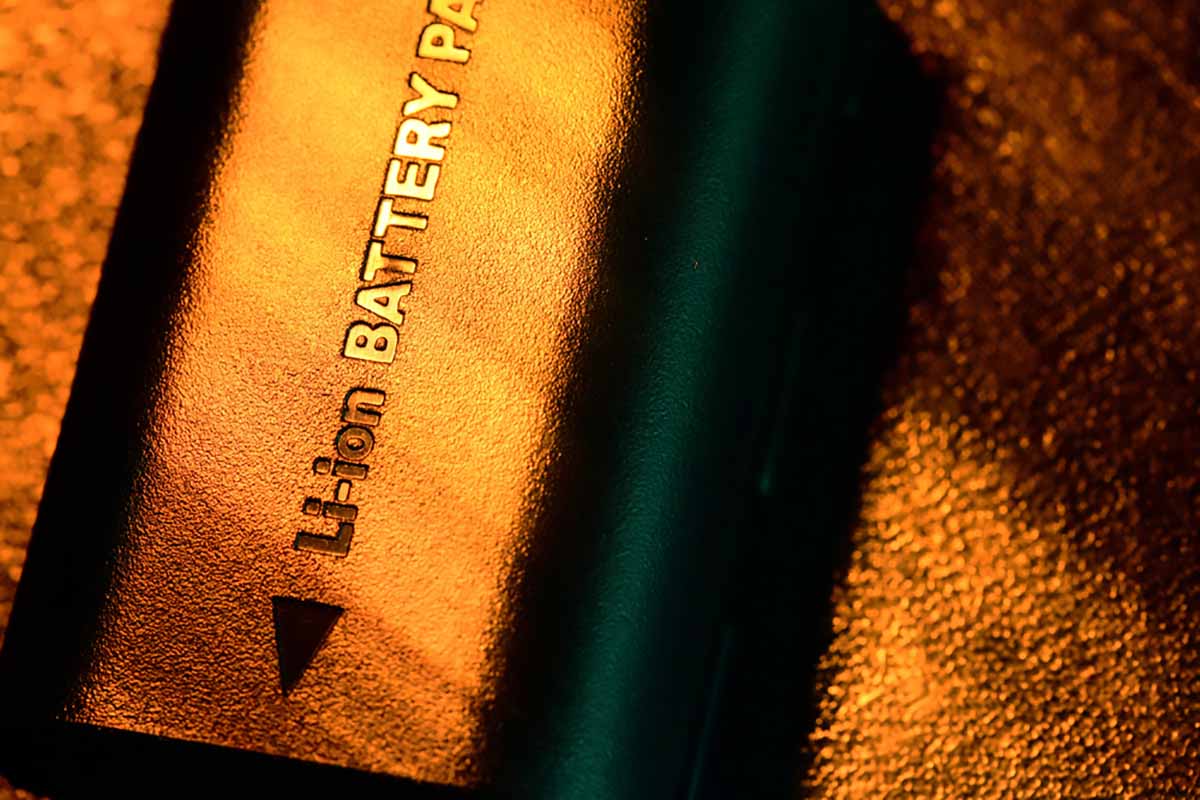
Green Li-ion’s battery recycling technology can take shredded lithium-ion battery material to pCAM material within the same system. | Janaka Dharmasena/Shutterstock
A lithium-ion battery recycling technology company is looking to build regional supply chains by providing recyclers and manufacturers with modular units that can take batteries from black mass to pCAM.
Singapore-founded Green Li-ion’s system was developed to solve a geopolitical and environmental problem with recycling lithium-ion batteries, Stephen Hayward, vice president of operations, told E-Scrap News. Traditionally, recycling batteries involves shredding them then separating out the critical materials, such as cobalt, manganese and nickel, along with the black mass.
However, before those materials can be re-manufactured into batteries, they need to be combined into cathode active material (CAM) or precursor cathode active material (pCAM). Most of the facilities that can complete that step are located in Asia, Hayward noted.
“Is that truly a secure supply chain and really a true carbon footprint reduction if you have to send your material out of the country to get it put into the format you need?” Hayward said. “My opinion would be no, it’s not. What you really want to do is keep it in the region where you shred the battery.”
That’s exactly what Green Li-ion aims to do, by selling both patented technology designs and equipment to e-scrap processors, OEMs and “anyone who ultimately has black mass.”
“It can reprocess pCAM and even use scrap off the back of manufacturing lines,” Hayward added. “It’s a very flexible unit and our target market is pretty broad. This truly is a solution for a pure circular economy and reduced carbon footprint versus the traditional way of recycling.”
The technology
The units, manufactured globally, use a single-batch, four-stage process. Instead of breaking the materials out into different sulfates, the technology keeps the critical materials in the desired end format through a series of leaching, filtration, precipitation, co-precipitation, selective regeneration and electro-separation.
“The best way to look at it is as you put the shredded material and cathode powder and black mass in, what the equipment will do is keep all the critical materials, in the format we really want it, in a protective bubble and remove all the material around it,” Hayward said.
That makes it possible for the equipment to not only produce pCAM, but pCAM made to client specifications, he said.
“If our client wants 8-11 pCAM and the black mass at the front end is 6-2-2 shredded battery, we can generate the pCAM the client wants because we have the ability to dose and be extremely accurate on the offtake,” Hayward said.
As the units are modular, they’re easy to scale up or down. Hayward said the company has multiple size options that can process anywhere from 728 metric tons per year to over 3,000 metric tons per year.
Seeking growth
Green Li-ion raised $22 million in funding in March 2023, making its to-date funding total over $38 million, and will soon have a working commercial operation at a plant running at an Aleon plant in Oklahoma. Hayward said the team is also working to make the technology usable with some other lithium battery chemistry, such as lithium ferrophosphate (LFP) batteries.
“We definitely want to continue to expand,” Hayward said. “Our model is being able to license our tech to the market. We want to share it. We saw the transition of going from the traditional to sulfate recycling, and we really want to help the market with the transition to be able to recycle directly to pCAM. For that to happen, we want to get our tech in front of as many recyclers and manufacturers as possible.”