This article originally appeared in the September 2017 issue of E-Scrap News. Subscribe today for access to all print content.
At most e-scrap facilities, a relatively bland gray metal box can usually be found lurking in the corner. It’s likely adorned with red, amber and green lights, but plant visitors nevertheless often walk by without even noticing its existence.
Though far less attention-grabbing than the rumble of a shredder or the shine of gold-plated circuit boards coming off the demanufacturing line, the unassuming box is the heart of a plant’s electrical controls system, which is vital to efficiency and automation. Getting to know what’s inside the electrical panel – and the wider network being steered by those switches and buttons – can help operators maximize the potential of their facilities, make quicker repairs and ensure employee safety.
This article serves as a primer to the electrical controls at the heart of mechanical processing.
Power play
Electrical controls influence the output of machinery and are capable of much more than turning on and off motors. Asking the right questions and specifying options with a machine order can help operators get the most out of this equipment component – and, by extension, the entire plant.
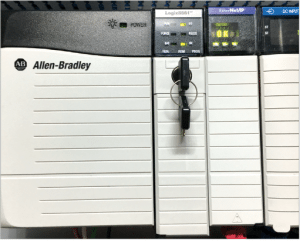
Programmable logic controllers (PLCs) use software to monitor key variables in an electrical system and enable appropriate reactions.
First, plant managers will want to have a good grasp on the specifics of electrical power sources. Most industrial plants run on three-phase power, which is designed to accommodate machinery requiring high horsepower. Most utility transmission lines have three sets of wires that deliver alternating current stepped down by a transformer to 208 or 480 volts (600 volts in Canada).
So what is the difference between single-phase and three-phase power? Envision a bicycle with one rider and a tandem-style bicycle with three riders. More power delivery is capable from the bicycle with three riders, and it’s the same with an alternating current (AC) motor supplied by three different wires, each with their own alternating current. As defined by Ohm’s law, a higher voltage can deliver the same power with less current (amps) than a lower voltage can. Using less current to do the same amount of work means smaller required conductors and switchgear, and this reduces controls costs.
Many induction motors are designed internally to take advantage of three-phase systems – the arrangement is simply able to deliver more power than the single-phase 110/220 volt electricity systems found in residences and offices. The frequency of the power is 60 hertz in North America, which means the current will alternate 60 times per second. These induction motors will run at a certain RPM when presented with three-phase 60 hertz power.
The next step is knowing what’s inside the actual control panel. This will help operators understand an electrician’s diagnosis during repairs, decide which spare parts are best to purchase, maximize the capabilities of the electrical panel, and explore opportunities for expansion or modifications.
Most control panels and systems begin with a programmable logic controller (PLC), which is a small computer that has been designed for high reliability in an industrial setting. It could be called the brains of the operation. The PLC runs simple visual software often referred to as ladder logic, which tracks a series of conditions in the plant (called “inputs” in the world of electrical controls) and then enables appropriate reactions (or “outputs”). The format is sometimes referred to in its abbreviated form, I/O.
An example of an input is a limit switch on a shredder access hatch that indicates a safe condition. Another input would be a rotation sensor on a conveyor pulley that demonstrates no slippage is occurring. The PLC interprets these inputs in several forms and will send outputs to other devices to cause a reaction, such as starting motors, changing their speed, opening and closing valves, and stopping or reversing a process. Often, many outputs occur together and usually in a certain order – this is what happens, for example, when a whole shredding line starts and stops.
More complex data elements, such as barcodes, belt scale weights and air quality, can also be captured by the PLC. This information can be stored and displayed as graphs or trend lines on a graphic interface, and this can be used for operations metrics or automatic operator notifications. Though few plants consistently take advantage of this capability, instantaneous data can provide a real operation edge and allow quicker decisions.
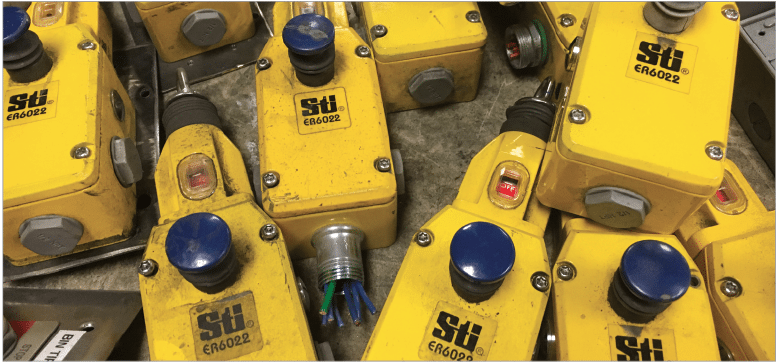
A well-designed electrical system will incorporate e-stop buttons or similar components that shut down machinery quickly to reduce material backups and worker injuries.
Components that lift motor efficiency
The most fundamental duty of the control panel is to start, stop and vary motor speeds. This is accomplished in several ways and is most commonly done with a motor starter, which is a set of contacts that are mechanically pulled in by a coil when energized. In the case of three-phase power, these starters will simultaneously connect three contacts together to transmit energy to the motor.
Most of these types of starters are linked to a component called a thermal overload module, which helps make sure the motor is shut off if too much current is drawn. These modules monitor the current to the individual starter and will interrupt the current to the coil, which will turn off that starter. For larger horsepower motors or motors with a large mechanical load, sending instantaneous full voltage directly to the motor can demand too much start-up power and overload circuits. Soft starters were developed to overcome this issue and are designed to regulate the voltage and amperage delivered to the motor and increase it over a short duration of time as the motor begins to wind up to its designed RPM. These types of devices extend the life of the motors by reducing start-up stress and are a must-have for large blowers, mills and certain shredders.
Another important tool within electrical systems is the variable frequency drive (VFD), or “freak” drive, as some affectionately call them. These solid state devices and are used to vary the speed of electric motors by varying the frequency of the three-phase power delivered to them. How is that possible? First, power passes through the VFD’s converter, which is made up of diodes and capacitors to turn the alternating current into direct current (DC) power. Next, an inverter turns the DC back into a synthetic AC power, but it does so at a specified frequency. There are multiple benefits to varying the frequency of power to motors. As frequency drops off from the default 60 hertz, so too will the RPM of the motor. For example, at 45 hertz, a motor will generally spin 25 percent slower and also consume less energy in certain applications. In some situations, over-speeding the motor up to 25 percent is needed and supplying voltage above 60 hertz for that task is easily accomplished with a VFD. Take note that once the motor is over-sped, motor torque will start to drop off and the VFD will generate more heat.
Slowing motors down is very helpful in controlling speeds of conveyors, shredders, air compressors and fans. The process of over-speeding motors, on the other hand, is useful on some types of shredders when more throughput is needed and the extra torque is not required for what is being processed. To use the VFD to vary motor speeds, operators use interfaces such as a panel-mounted knob, touchscreen menu or direct instruction in the background by the PLC. For safety reasons, workers should avoid opening the panel under load to access the VFD and should instead make adjustments with an interface, especially if this is a frequent need.
And speaking of safety, any control panel used for an industrial process or recycling application should utilize an emergency stop (e-stop) or power off (EPO) system. These safeguards will instantaneously shut down the system based on activation of a specially marked button or pull cord with “self-latching” functionality, meaning the button or cord stays mechanically activated once pushed until reset by the operator. In fact, many guidelines dictate that a separate reset button on the panel must be pushed before the line restarts. In an emergency, stopping a line quickly can prevent bad jams, material buildups, poor quality or, most importantly, injury.
Sufficient placement of e-stops is good practice and often required by regulators to minimize the time a worker must search for a button or other activator. For example, pickers on a conveyor can benefit from an overhead cable in certain situations.
Many e-stop systems are wired inside the panel in such a way that they are designed to be fail-safe. This means that if the contactor or switch fails, it will not allow the plant to run.
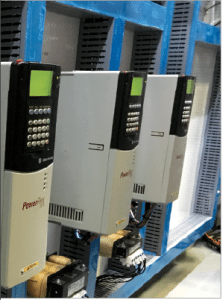
Variable frequency drives (VFDs) alter the speed of electric motors by adjusting the frequency of the power source. This can help to optimize machine functionality and energy use.
A special safety relay, often called a master control relay (MCR), can shut the line down by interrupting voltage feeding motor starters and similar devices in the control panel. For larger plants with many e-stops, it is possible to buy a switch type that has an extra set of contacts installed to be an input to the PLC, and this step allows the operator to identify the exact location of activation. Knowing which e-stop was pulled can save valuable production time. Most importantly, plant managers must encourage the operation staff to use the emergency stop system without hesitancy. In an emergency, a split second can make the difference of someone going home that evening or not.
Innovation leads to information
Technology in the industrial controls sector has evolved quickly.
For instance, many companies now offer remote machine monitoring services that deliver machine-efficiency data right to a manager’s computer or phone. A remote monitoring system will typically have a smaller, more specific type of PLC or microprocessor embedded in the control panel to collect inputs, outputs and data history, and then it can transmit information to a cloud service, allowing the operator to see details on shredder reversals, shutdown duration, machine utilization or tonnages processed. In some cases, the machine manufacturer can be given remote access and troubleshoot or change parameters while saving the time and expense of a visit.
Machine feedback can also be used to allow the recycling line to regulate itself by use of extra programming in the PLC and additional sensors. One example is the case of monitoring a belt scale post shredder. A time-weighted moving average of the weight processed can direct the shredder to slow down or speed up to ensure a consistent processing rate occurs.
The user interface of the panel can be a powerful ally as well. It can display useful data, including fault history, trend lines of power usage, tonnage, sortation quality details and e-stop location activation.
To ensure the capabilities of the control panel are fully leveraged, the location of the panel should be carefully considered. Heat, dust and other realities of a processing plant can wreak havoc on a panel, especially if it’s not specifically designed for that duty. There are National Electrical Manufacturers Association (NEMA) ratings for electrical enclosures with the most basic rating being NEMA 1, which indicates the product is suitable for simple indoor installations. For recycling operations, a higher degree of enclosure, such as a NEMA 4, may be required. There are also standards for the size of the enclosure and the amount of switchgear contained. Designing in extra capacity upfront can be useful so that the system can handle future changes to the wider operation.
An area worthy of exploration
Certainly, the complexities and options in the realm of electrical controls can become overwhelming for a plant operator who already has many responsibilities and limited time for new projects. But exploring opportunities in this area can lead to more efficient use of a facility’s expensive processing line and also increase safety while reducing downtime.
It may be tempting to walk by the control panel. However, those that use controls to maximum effect will find upsides in terms of both profit and productivity.
Rafael Reveles is an engineer and president of Converge Engineering. He has 18 years of experience designing and building e-scrap and metals processing systems and can be contacted at [email protected].
Converge Engineering (convergeengineering.com) is a UL 508A listed panel building shop and e-scrap shredding and materials-recovery solutions provider.