This story originally appeared in the December 2016 issue of E-Scrap News. Subscribe today for access to all print content.
Running a shredder efficiently at a recycling facility has never been harder. Difficulties are tied to an increase in regulations, higher energy costs, increasing operational costs and lower commodity prices in some industries.
Although many new shredding technologies and approaches are available to operators to help them overcome challenges in this area, it’s also critical to bring innovation and investment to the safety procedures associated with these machines. Ultimately, the discussion around shredding systems is not just technical or procedural – it also has a moral component. Nobody should have to learn that a family member or loved one is coming home from the facility with a serious injury – or that the worker is not coming home at all.
We as an industry know better and can do better when it comes to shredder safety. To help lift the dialogue on this point, the following article will provide a detailed look at the specific danger zones that exist in the shredding realm and offer best practices on how to make sure threats such as fire, crushing, electrocution and others are minimized to the maximum.
Moving materials mindfully
While there are many risks associated with shredder operations and maintenance, the employees that may be facing danger most often are those operating mobile equipment in support of the shredding line. A poor or congested facility layout can lead to a higher chance of vehicle collisions, pedestrian accidents or exposure to falling or ejected material from the shredding system.
To avoid those issues, pedestrians should be routed to specific pathways with railings to isolate their interaction with moving vehicles and equipment. Appropriate signage and site policies must support such separation.
Likewise, vehicles need rules of engagement for areas in which they operate. For example, a tall feed conveyor may have pieces hanging or falling off. “No go” zones are needed to ensure vehicles don’t end up in danger zones around the equipment. Some operations will use large material handlers and grapples that have their own extra considerations. These vehicles can have risks such as dropping material too far from a target accidentally, tipping over due to operator error and being hit by pile storage slides. These material handlers should have dedicated positions, properly designed conveyor-loading zones, designated clear spaces, and extra operator training for proper safety performance.
Lock-out logistics
Lock-out-tag-out procedures and training specifics are part of federal Occupational Safety and Health Administration (OSHA) requirements (29 CFR 1910.147) when it comes to operating most shredding equipment. This essential safety procedure involves isolating the power or energy to the shredder or associated equipment prior to performing maintenance. Operators must also document the specific LO/TO procedures for each piece of equipment and train any affected individuals.
An example of this type of safety activity can be seen at the infeed conveyor to a shredder – it will likely need isolation when maintenance activities are planned for within the shredder chamber. Such steps ensure material cannot fall on anyone in the area inadvertently. The LO/TO points must all be clearly labeled and have a proper hasp to accept an approved locking device. Procedures should also include steps that test the effectiveness of the lock-out prior to work commencing. It is important to note that other forms of energy besides electrical may also require isolation – air, hydraulics and stored energy are examples.
While a good training program and a company culture of “safety first” can bolster the effectiveness of a LO/TO program, opportunities for human error may still remain. Adding secondary systems to high danger zones, such as shredder chambers, can be an inexpensive investment with high safety rewards.
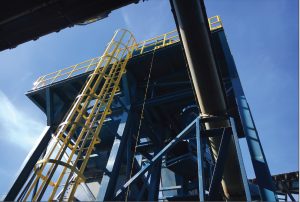
Danger lurks in high-elevation areas. Adding maintenance access platforms at appropriate points along the shredding line can greatly reduce the risk of accident.
Also, limit-switch sensors are common on many shredder and baler access doors, but it is important to have a harder-to-defeat model with a coded magnetic non-contact switch to make it difficult to fool the sensor. In addition to a door sensor switch that does not permit shredder operation when an access hatch is open, a captive sequential key interlocking system is another inexpensive investment to help prevent the unthinkable.
These captive key systems work by having a special key in the control panel that is needed to open the shredder hatch. Once the key is removed, control power for the shredder is interrupted. The key is then taken to the shredder door, where it must be inserted and turned to allow another special key to be released from the latch. The operator then takes the released key into his or her possession during maintenance while the key that came from the control panel is held captive in the open latch until the door is closed and the key from the maintenance operative is replaced.
These additional levels of safety should be seen as insurance policies and absolutely are not a substitute for a robust LO/TO program.
On guard
Much like LO/TO, the guarding of machinery is specified in local and federal regulations and is also enforced by OSHA. Guard devices are required to isolate employees and visitors from moving parts than can pinch, crush, cut and cause other types of injuries. For example, an expanded metal guard covering a rotating shredder drive shaft must be present and placed in a specific location.
In addition, conveyors generally require belly pans or return roller guards, and they too are covered by a specific OSHA standard (29 CFR 1926.555). Machine guards should be affixed in such a way that specific tools are required for removal. Some manufacturers will add limit switches to critical guards, a safeguard that will not allow the system to run when guards are not in place.
Even though a site may have exceptional guarding, the unexpected can still happen, which is why multiple emergency stops should be spread throughout a shredding system. These “e-stops” are another inexpensive addition that can minimize safety threats and enable faster response to a system backup, jam or fault. Not all e-stops are created equal, however, and systems should follow governmental guidelines. The best units have redundant contacts and are also monitored to allow notification to the operator of which section of the plant has been stopped – this reduces downtime in the long run in larger plants where it may take time to realize which e-stop has been activated. If the e-stop cord or button is going to be moved, it is important that a qualified safety professional evaluate the risk and effectiveness of any modifications.
The maintenance factor
Many accidents in the shredding industry unfortunately happen with maintenance staff or contractors working on the equipment. At the same time, many accidents can occur because equipment has not been maintained properly. Examples of maintenance-related hazards can be hydraulic hose breaches due to abrasion, fires caused by leaking oil, shorts and arc flashes due to loose connections, and pieces falling or breaking off a machine.
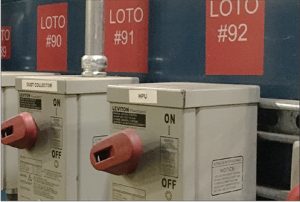
Lock-out-tag-out procedures are required under federal regulations. The systems can be bolstered by proper training and a company culture that prioritizes employee safety.
Besides having a documented preventative maintenance program that meets manufacturer specifications, experts also recommend a TPM (total productive maintenance) program and associated boards. TPM systems generally delegate simple inspection or low-risk tasks to operators or maintenance helpers. Examples include inspection of a hydraulic power unit for leaks, checking the oil level in a sight glass, greasing certain items and checking belt tracking. Inspection sheets can be located on multiple small boards throughout the plant and are typically reviewed by management daily. Overall, TPM programs can remove some load from a maintenance team and enable those specialists to focus on more urgent tasks.
Developing metrics to measure preventative maintenance percentage of timely completion and mechanical availability can also be a good enabler to a long-term theme of effective maintenance.
Poor procedures or lack thereof can lead to unsafe conditions when staff members are working on their shredding systems. One of the most prevalent issues is lifting and rigging, since most parts on a shredder will be heavy – anyone performing a lift should be properly trained in techniques. Certain items to focus on are appropriate load rating and inspection of rigging, planning lifts and respecting the lifting capacity of the crane or lifting device, reviewing the ground conditions for a level and stable lifting base, and isolating the area from pedestrians.
A stunning example of the need for training is that of the common lifting threaded eye bolt: This critical component may lose up to 70 percent of its rated strength when a load is applied at angle that is 45 degrees of vertical. A better choice in this case would be swivel hoist rings, which are rated at full listed capacity for all 180 degrees of load applied.
Many departments often decide to fabricate their own jigs and special tools for lifting certain elements and wear parts. Take care to ensure a professional engineer has verified their safe lifting ability or has sourced them from the equipment manufacturer. In addition, keep in mind that high elevation areas may require man lifts for maintenance activities such as belt, bearing and motor changes. Adding maintenance access platforms during the system-design phase can reduce accident risk as the team will be able to access elevated areas more stably.
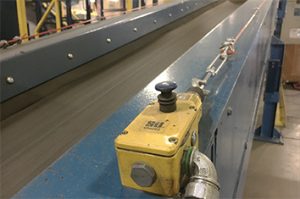
Multiple emergency stop buttons should be located throughout the shred system. Many of these units can be programmed to quickly alert a manager that a certain section has stopped running.
Lastly, use care to ensure OSHA confined-space policies are applied and followed properly. A shredder interior is usually in this category and requires extra protocols when accessed – important aspects to consider include an escape plan, extra PPE and an air monitoring device.
Steps for fire prevention
Fires are prevalent in the recycling industry for a variety of reasons – worn shredders, inappropriate material in the feed and heat buildup are just a few. Fortunately, many new technical solutions exist to prevent and suppress blazes caused by these situations. However, preemptively undertaking a fire-response plan can illuminate potential gaps when it comes to fire department access, ample water supply, bulk-storage standards for piles, and fire water runoff capture strategies. Operators may even consider inviting the local fire department to the facility for a walk-through.
Whether used after hours or during operation, new types of infrared monitoring services or special multi-band flame detectors can save a facility. A larger footprint operation may benefit from a monitoring company that uses advanced cameras and software to detect smoke and heat and call the fire department. Smaller companies or those that need to directly monitor the shred line hoppers – tire shredding operations, for example – may want to invest in a packaged system with flame and heat detectors that initiate specific actions, such as shutting down the line, applying water to specific zones and sounding alarms.
Also keep in mind that certain machine faults can cause fires. For example, a high-pressure hydraulic line breach could atomize hot oil or an over-temp bearing may ignite grease or surrounding materials. In the case of hydraulics, oil-tank-level sensors can effectively be used to shut down the system if rapid oil loss occurs, and a simple bi-metallic heat detector can also safely shut down hydraulics. Some insurance companies may even recommend special hydraulic oils that are less prone to flash fires.
Finally, developing a plan B for handling fires is prudent and not always expensive. A minor investment in a portable foam cart or just extra extinguishers can absolutely pay off.
Electrical safety
One of the most serious safety risks in any shredding operation will be the electrical supply and systems. Most shredders run on higher voltage, three-phase power at or over 480 volts. This level of power can cause violent explosions known as arc flash events that are almost always fatal. These events can be caused by something as simple as an employee accidentally dropping a tool or cover into an open electrical enclosure. The dropped metal item may connect several phases or phase to ground, creating a short and the associated explosion.
Furthermore, when an employee is shocked by high voltage, death can occur due to the incredible current that will flow through. Thus, staff must be qualified to properly and safely troubleshoot and access panels. Under no circumstances should individuals work on live panels or switchgears without following OSHA and National Fire Prevention Association standards for arc flash PPE – these standards call for special suits and visors. Investing in a qualified electrician when repairs are needed is a good safety investment.
In addition, anyone who works on the electrical gear can be put at risk if the panel and source labeling are not accurate. Each panel should have proper labeling, and the labels should note any circumstances where multiple sources of voltage are present in the same enclosure. As mentioned earlier, proper machine maintenance is a must, and this would include inspecting for loose conduit and connections. One effective method: Contract an inspection company to use infrared thermography to scan loaded switchgear for temperature differences. These scans can show hot spots that indicate loose or poor connections and other issues that can be proactively repaired.
Safety comes from the top
Most of the scenarios highlighted in this article have simple and inexpensive remedies. Such safety steps include vetted procedures, comprehensive training, scanning, bolt-on devices, best maintenance practices and some modern engineering controls.
Higher level investments such as maintenance platforms and flame detectors can be budgeted for and integrated into an operation over time. However, none of these techniques and devices can replace a top-down company culture of a safe work place.
This is not a trivial journey. Company cultures are developed over time based on what is allowed and expected. I urge you to make safety your top priority. It is a prerequisite for success in our industry – and is simply the right thing to do for the employees that underpin every operation.
Rafael Reveles is an engineer and president of Converge Engineering, the recently launched engineering services business of Sims Recycling Solutions. He has 17 years of experience designing and building scrap processing systems and can be contacted at [email protected].