This article originally appeared in the July 2019 issue of Resource Recycling. Subscribe today for access to all print content.
Since Star Plastics’ inception in 1988, safety has been the first priority. And this focus has been key to the company’s viability and growth. In short, safety goes hand-in-hand with quality, and we’re proud of our high-quality products created by safe, healthy and happy employees.
How can other recycling facility operators systematically address this critical issue? It takes a multi-faceted approach. At Star, we found five key areas to creating and maintaining a safe work environment, and those considerations are detailed below.
Make it central to company culture
New Star Plastics employees learn very quickly that worker safety is paramount at the company – and that it should be very important to them.
We do this by inserting safety into every aspect of the business, including regular employee trainings, company activities and celebrations, quarterly business reporting, and everyday conversations.
Ultimately, everyone is involved. While the management team spurs the creation and implementation of safety procedures and trainings, employees play an important role in bringing fresh eyes to the facilities. If an employee notices a potential safety hazard, they are encouraged to let their supervisors know, and managers are expected to run those concerns up the ladder. This has consistently led to the creation of improved policies, procedures and practices.
Further, we’ve found it’s important to celebrate safety milestones, publicly acknowledging successes and integrating workers in a fun way.
At Star, we reward our employees with safety breakfasts and branded Star gifts. For example, in celebrating five years of no “lost time incidents” at our Ravenswood, W.V. facility last fall, employees received duffle bags embroidered with Star’s new logo. We also display our safe-day counts on marquees throughout the plant and on our website – this makes it clear that we take pride in our employees’ positive habits.
In addition, we have a yearly safety slogan contest, with the winning phrase printed on calendars and banners, and the winner receiving a gift card. Around 100 of the calendars are printed and displayed prominently throughout the plants. Star also rewards employees for maintaining safe practices on a quarterly basis with bonuses and monetary raffles.
These steps all bring the topic to the heart of the company’s culture, ensuring that workers and managers alike really do put safety first.
Keep workers properly instructed
Mike Moran, Star’s Ravenswood site plant manager, describes the key to safety in manufacturing succinctly: “It all starts with good training.”
Over the years, we’ve developed policies, practices and procedures that ensure our employees are properly instructed on how to undertake their tasks in a way that minimizes risk.
As alluded to earlier, during orientation, new Star employees are taught the company’s safety policies, the procedures around their specific job functions, and the proper protective equipment and usage of tools required by their position. This includes becoming certified on various safety procedures and equipment operation.
In addition, company policies and practices are reviewed on a regular basis to ensure that safety is remaining central. Star is dedicated to continuous improvement in all areas – products and process, for instance – and safety is no different.
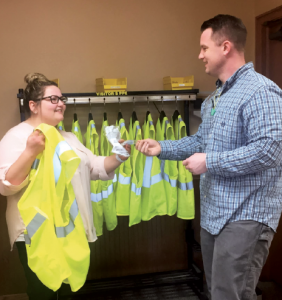
When safety is reiterated at a facility, it becomes part of the company culture, with conversations about best practices and expectations occurring regularly.
All employees also participate in monthly OSHA “refreshers,” with rotating topics scheduled throughout the year. Examples of these topics are respirator use and hearing protection, fire safety and prevention, lock-out-tag-out best practices, and other hands-on trainings. Workers also complete forklift recertification every three years, participate in site fire drills once a year, and run other emergency scenario responses.
It’s also important to note some company policies were created at the suggestion of employees, have been put into practice and are still used to this day. Years ago, for instance, a plant floor employee noticed that most of his co-workers regularly carried pocket knives (a normal practice in rural West Virginia), and they would occasionally fall out at inopportune times and lead to small cuts. A rule barring pocket knives from the plant floor was implemented, and the company saw a decrease in OSHA recordables.
Talk it up
This point may seem like a given, but constant communication with your team about safety is key.
The number of safety-related incidents, or lack thereof, should be a critical metric measured by management and reviewed in meetings involving leadership and employees alike.
At Star, managers discuss procedures and practices in every shift’s morning meeting and are always looking for feedback from employees for ways to improve company practices to prevent an incident. On a weekly and quarterly basis, managers go over any updates to safety protocols or corrective actions that may have occurred at the beginning of each shift.
If an incident occurs, a supervisor should complete an in-depth assessment of the incident and review it with all employees. When your employees have detailed information about the incident, they can learn from it and even contribute their experiences to help build a safer, more productive future.
When talking about safety, don’t limit your communications to purely inside the business. Companies can announce safety achievements or insights in the form of blog writeups, press releases or social media posts. At Star, we post press releases regarding our safety updates and achievements. It’s beneficial for our customers to get to know us and learn what kind of company we are. Our emphasis on employee safety reflects the sense of care embedded in our business, and that fact shows through to customers in our finished products as well.
Ultimately, everyone involved with the company needs to be comfortable and confident communicating about safety. This is another way to reiterate to employees that safety is a responsibility for everyone, not just those working on the plant floor.
Take a team approach
Several years ago, Star created a specialized Safety Team that includes a variety of management personnel. While safety is everyone’s responsibility, creating a dedicated team guarantees that a specific group of people is focused on maintaining a safe work environment.
The Safety Team performs EH&S walkthroughs of each plant twice a month, with focused attention on the work environment and equipment. They inspect multiple areas of the plants while reviewing a checklist to ensure they are viewing everything with fresh eyes. The checklist is an audit of housekeeping items regarding the work environment, mobile equipment, records and workstations.
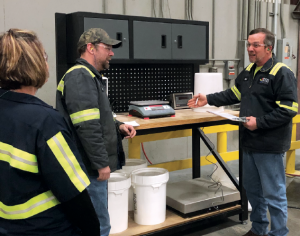
A dedicated safety team at an operating site can reduce worker injury risk by regularly inspecting workstations and formally reporting any problems.
Examples of walkthrough items include checking for clutter, spills or debris in the aisleways; inspecting lighting conditions; monitoring usage of personal protective equipment; and inspecting the condition and storage of tools. The walkthrough ends with the Safety Team listing any potential hazards, outlining the cause of the hazards and noting suggestions of corrective activity.
In the event an incident occurs, this team completes an in-depth assessment, taking the time to understand what happened, how it happened, and how it can be prevented in the future (this could involve equipment improvements, a procedural modification, or something else). If any changes are made, it’s important to be sure the details are then reflected in relevant employee trainings.
Back up aspirations with investment
Putting money behind your employees’ safety is the final component of creating a safe work environment.
This means looking at your current processes and equipment, understanding how they are being used, and analyzing whether they can be improved with new tools or a fresh coat of paint to protect the wellbeing of workers.
An example that resulted from a Star EH&S walkthrough was the addition of a pneumatic lift device at the material bagging station. Previously, the bagging operator was manually lowering filled bags from the bagger to the floor, stacking them onto the pallets. With the pneumatic lift, the pallet starts at the operator’s waist-height and is gradually lowered during the process. This removed the need for the operator to bend, greatly reducing the risk of back and shoulder injury.
Other common investments in safety are lighting and equipment layout improvements, the purchase of powered rolling systems or jib cranes for moving heavy objects, repainting safety lines and handrails, and the addition of laser sights on forklifts.
When you’re willing to put company dollars behind the safety of your employees, they will see that company profit is being invested back into the business for the betterment of their health and safety – essentially, it’s a signal you’re investing in them.
Safer workers, stronger business
Safety’s significance needs to be ingrained in every level of a recycling business. To do so, you must foster a working environment that values proper practices, making it clear that safety is the responsibility of every single person.
The obvious benefit is that fewer people are hurt on the job, which is a goal that should be front and center for every company in every sector. But beyond that, a dedication to safety brings secondary benefits in the form of lower turnover, more productivity, higher attention to detail, better-quality products, and positive attention from customers and the local community.
In other words, by building a culture of safety, you are building the business itself. This is the kind of structure that everyone – workers, managers, owners and investors – ultimately deserves.
Molly Ritchie helps lead marketing and brand development at Star Plastics. She can be contacted at [email protected].