This article appeared in the May 2021 issue of Resource Recycling. Subscribe today for access to all print content.
Over the last year, demand for recycled fiber has been strong, and that’s meant strong pricing for companies and communities moving the material to market.
But what should we expect once the pandemic-shaken supply chain finds equilibrium? According to a leader at recycled paper mill operator DS Smith, manufacturers’ appetite for recycled fiber will stay at elevated levels, in large part because e-commerce will drive a need for packaging.
DS Smith is headquartered in Europe but operates two paper mills in the U.S., and the company has pushed further into the U.S. market in recent years. In addition to its mills, located in Georgia and Pennsylvania, the company operates multiple U.S. box-making facilities and recycling facilities, focused on fiber-based packaging and recovery of old corrugated containers (OCC).
In an interview in March, Toby Earnest, director of recycling at DS Smith North America, discussed the impact of disruptions in fiber supply related to COVID-19 as well as the future of the recycled fiber market.
The following transcript has been edited for brevity and clarity.
RR: How has the pandemic impacted supply and demand of the recycled paper your company relies on?
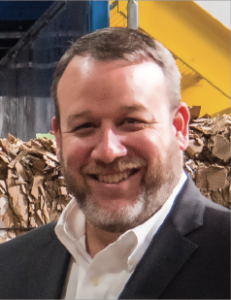
Toby Earnest
Toby Earnest: The pandemic has created a lot of volatility in the recovered fibers market. We’ve seen supply decreases from the industrial, commercial, hospitality, and restaurant industries. Those sectors were hit hard. They’re coming back a little bit now and have been back on the comeback trail for a little while. We’ve seen grocery experience a goods spike, and of course the e-commerce business has spiked quite a bit since the recovery from the pandemic.
The addition of our recycling operations in North America has kind of positioned us to help use our robust supply chain to capture some of those recovered fibers in the market needed to fuel our essential paper mills and other paper mill partners.
We announced our paper recycling facility in Reading, Pa. just about a week before the pandemic and lockdowns and restrictions took place. Having that recycling facility kind of gave us a circular economy trifecta – we have a paper mill in Reading, Pa. and also a packaging facility there, all within a mile or two of each other.
That circular economy trifecta also allows us to recover fibers from our packaging facility, other packaging facilities in the area, along with some distribution centers and other fiber streams. We bring those into the recycling plant for processing and we send those to our paper mills, and they generate paper and send it back to the packaging plants to produce the essential packaging products for our customers.
So a lot of changes have happened over the last 12 months due to the pandemic, but we feel like we’ve evolved and adapted well within the market.
Is it mostly OCC you’re using, or other grades?
At our mills, it’s mostly OCC.
Are materials recovery facilities (MRFs) a significant channel for sourcing recovered fiber at DS Smith?
It is one of the streams that we use. We try to work with those larger facilities, the Waste Managements, the Republics. We try to work with them because we operate in the cities they operate in. So I think it’s being a part of that community; we need to be a part of that solution as well.
What has it been like sourcing OCC during the pandemic? Are you having any trouble getting enough material?
I think negotiating a new reality around recovered fibers has been a challenge for everyone. It is difficult. OCC is now a global commodity, well-sought-after in the U.S. as well as across the world.
DS Smith, here in the U.S. and in Europe, we’ve leveraged some of our established customer relationships, our supplier relationships, our supply chain relationships, to help weather this storm. I think we’re going to have to keep doing that.
We’re going to have to continue to find ways to find synergies in the supply chain in total to keep ahead of OCC demand, because from everything I read and the people I talk to, the demand itself is expected to increase worldwide every year through 2025. Our circular business model is helping build bridges to get to that reusable OCC.
One of the big trends we’ve seen in OCC has been a shift from commercial to residential generation as businesses closed and people have spent more time at home. What does this mean for quality? Have you seen quality change as more material comes through the residential stream?
In terms of quality of collections at the residential level that are going into these MRFs, I think the collections are better due to that e-commerce shift and things that DS Smith is doing as well as other industry leaders.
Recyclers are committing more resources – whether it’s human resources or mechanical resources – to their processes because this is now a very valuable supply stream for the paper industry, and a much needed one. I think that the residential collection and MRFs are better because of companies like DS Smith designing unwanted recyclable items out of the packaging.
I think the quality is probably a little better going into the MRFs. As a country, do we do a fantastic job of capturing all that material at the MRF level? Probably not as good as they do in Europe.
That’s interesting to identify the design stage as a critical component of ensuring quality at the MRF level.
We call it “circular packaging design principles” at our level. All of our designers have been trained in this area, to look for new ways to take away non-recyclable items, whether it’s plastic or other chemical properties. Everything they can do to make the product more recyclable at the end of the day.
On the design front, although corrugated is still a huge component of the e-commerce system, we’ve seen some of these companies move into other areas, using plastic packaging for certain items, for example. Is that a concern, e-commerce packaging moving into plastic?
No, I think we see a trend moving more toward fiber-based materials. I think the design upfront, the closed-loop circular economy approach to what we’re doing is intriguing to our customer base and they want to be involved with it. It really all starts upfront with the design. We work tirelessly on the front end both to educate our customers on the sustainability aspects and on how the design of this product will impact them throughout the entire product life cycle and supply chain of what we’re offering.
Do you tie the projected OCC demand directly to the e-commerce trend?
Absolutely. We work hand in hand with a lot of those major customers.
We’re up 44% year over year just in that e-commerce sector. Initially during the pandemic, volumes were down, but once lockdowns and restrictions eased and we made adjustments, growth has been fast and furious. For us, we’re seeing it. We’re feeling it. Projections say the packaging market as a whole is set to grow 3.3% in 2021. We’re going to be a part of that growth.
DS Smith previously predicted significant growth in the U.S. corrugated market in the years to come, and the company expressed interest in expanding its presence in the U.S. That was before COVID hit. How does the pandemic impact that growth?
We absolutely plan to grow in the U.S. market. I think the market is right for us to grow here, and our CEO has stated many times that we want to grow in the U.S. market. The packaging is going to be up 3.3% in total, and I think the U.S. market is primed to get a large percentage of that. It’s kind of a ferocious growth in packaging for the U.S., and I think DS Smith definitely wants to be a part of that growth and has plans in place to make that happen.
So the underlying trends that were driving that growth before the pandemic, they will still be there afterwards?
Absolutely. I think our customers that we widely hold in the European market that have a presence in the U.S. market want us to be a bigger part of the U.S. packaging base.
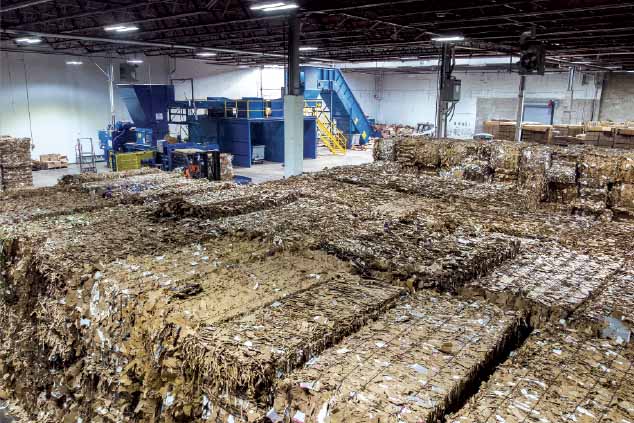
DS Smith recently opened a fiber recycling plant in Reading, Pa., giving the company a mill, packaging manufacturing facility and recycling site all within two miles of one another.
What are some differences DS Smith has seen when it comes to corrugated trends in the U.S. versus Europe during the pandemic?
There’s a lot that’s actually the same. The spike in value of OCC during the pandemic, the effect of lockdowns and COVID restrictions, and just the effect on recycling infrastructure and the impact on supply chain, the shift in demand for packaging due to e-commerce.
All these things are pretty similar to what we see in the U.S.
I think one of the biggest differences is probably the lockdowns and restrictions. On the East Coast, non-essential businesses came back a little faster I believe. Some countries in Europe are still experiencing the effects of lockdowns and restrictions in 2021. Germany is having a really tough time right now, and for the most part Florida is wide open. Some of the states up and down the East Coast, restrictions aren’t as hard as they are even out on the West Coast or in Europe at all.
At the start of 2021, China officially banned imports of all recovered fiber. Does this impact your operations? Does it present an opportunity to bring in material displaced by that market shift?
From a fiber standpoint, China moving out of the market has created opportunities for other countries.
A lot of the companies that were heavily involved in China have now moved to India, to Malaysia, to Thailand, some of the other countries surrounding China, and have put a lot of infrastructure in place to provide pulp from OCC and recyclable products back into China.
That trend – and Chinese imports going down – started that in 2017 when Chinese officials announced that they were going to do it and not take any more recycled fibers into the country. I think our industry was well aware that that was coming. It’s kind of been factored in all along. We knew it was coming. We saw the decreases in export from Europe and the U.S. every year. They started out in 2017 taking 25 million tons. That number decreased to 18 million tons in 2018, 11 million tons in 2019 and in 2020 they took just about 5.5 or 6 million tons. And now they’re not taking any.
But that was the plan all along. We all saw it coming. We all saw the infrastructure that was being developed around the world to help compensate. Even in the U.S., there’s been investments from Asian companies. We saw that increased investment with Nine Dragons and some of the other companies.
The fiber need is still there. Whether they’re taking it directly into China or not is not paramount to what’s really going on. The fiber need is still there, and that growth is still there. If you’re going to grow packaging 3.3%, you’re going to have to have the fiber.
Export figures from the first months of this year have shown material is still moving, even without China taking in much.
It’s going everywhere. It’s going to India. It’s going to Southeast Asia. It’s going to Latin America. Like I said, this is really a global commodity, and it’s going everywhere.
Colin Staub is the senior reporter at Resource Recycling and can be contacted at [email protected].