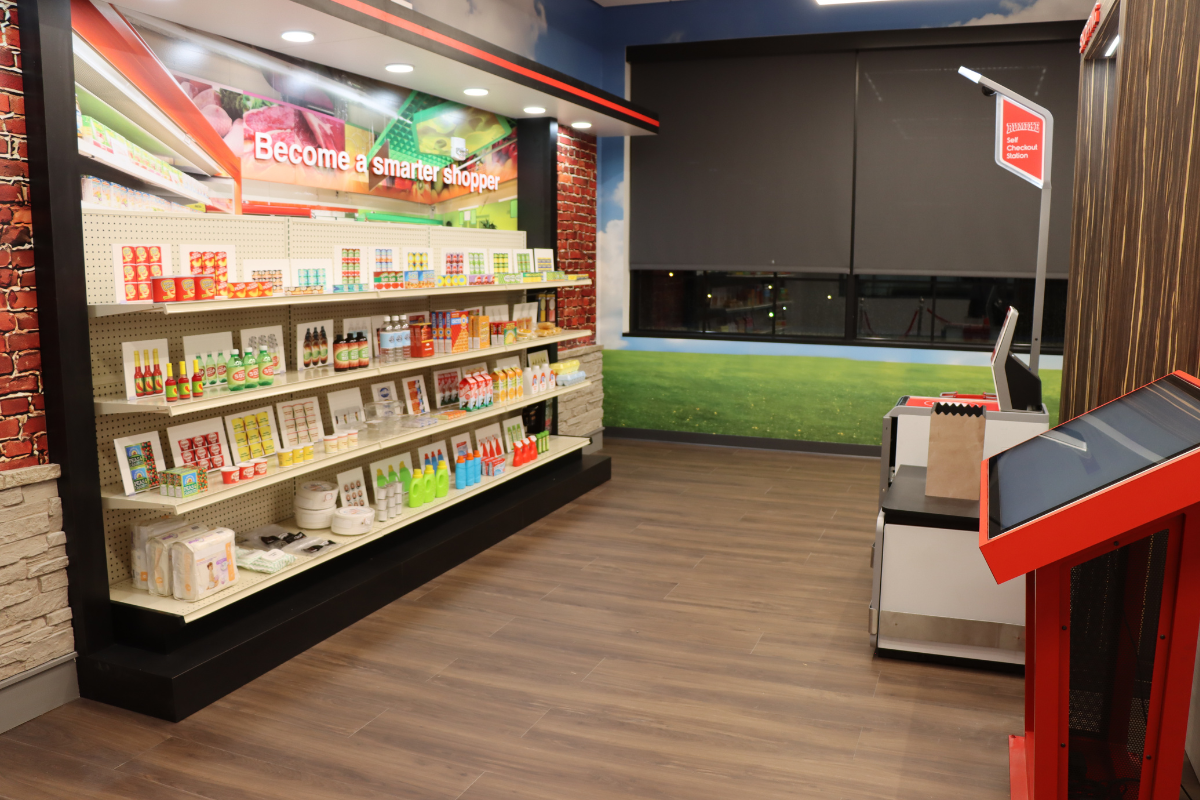
The new recycling center in Ohio combines vast processing capacity with community outreach and education, company leadership said in an interview. | Courtesy of Rumpke
Understanding customer needs has shaped the new Rumpke Waste & Recycling facility in Columbus, Ohio, and will help increase incoming volumes, according to company leadership.
For example, Rumpke works on optimizing local infrastructure in response to community needs, Jeff Snyder, vice president of recycling at Rumpke, told Resource Recycling.
“If a municipality is recycling every other week, how can we get them to weekly or increase cart size? The size of the cart is critically important,” Snyder said. “We continue to work with dropoff programs – if you don’t have curbside service, where can you take the materials?”
Municipalities also may require education on how recycling can help manage growing volumes of consumer waste, Snyder said. For example, some customers would prefer a smaller recycling bin. “It’s not always what the recycler wants but what the customer needs” that prevails, Snyder said.
“Financial barriers are a real thing here in Ohio,” Snyder said of the obstacles to recycling adoption.
“Two and a half years ago when we started to look at building a new facility to replace the current facility, which is 16 years old, we decided to go all in in the City of Columbus,” Snyder said. “We wanted to build something sustainable for the city long term of a size that we can evolve new commodities in the future, and handle the volumes the city would provide us.”
Rumpke’s 15 recycling facilities service Ohio, Kentucky, Indiana, Illinois and West Virginia.
With Rumpke opening up the facility on Aug. 6 – and the company describing it as the largest MRF in North America – Plastics Recycling Update spoke with company leaders to learn more about the equipment, design choices, downstream buyers and more.
Designed to meet buyers’ needs
The 226,000 square foot facility services 50 of Ohio’s 88 counties, accommodating 50 trailers at a time, Snyder said. With the new facility, processing capacity has increased from 160,000 tons to 250,000 a year, and the speed has doubled from 30 tons per hour to 60, according to the press release.
“It’s critically important to have a high recovery rate of recyclables, and this is designed to recover 98% of recyclables, which is a very high number in our space,” Snyder said.
The facility has 19 optical sorters, which Rumpke uses to start the two- and three-dimensional sorting of plastics from paper fiber. Rumpke also utilizes AI, Snyder said, and has no manual sorting on the container side of the plant.
Snyder said the plant is designed to have 97-98% uptime, compared to a typical rate in the low 90s, and facility manager Logan Miller credited the increased uptime to redundant processes.
“If one is down, we can take the feed to another one,” Miller said of the four balers and dual sorting lines. “And if a bottle doesn’t get captured, it goes through multiple times, gets recirculated. It’s a complete redundancy.”
“Recovery rate was so important to me, to increase the volumes we’re sending to ADS or Eastman,” he said. “And the other thing is the ability to make a superior product for the market. We want to provide the best product they can possibly buy. We’re not including other products in there.”
Eastman prefers opaque or colored PET as feedstock for its first methanolysis plant, which breaks down PET into its molecular components to make virgin-quality resin. Eastman said in a late July earnings call that it would work to expand its feedstock slate.
“A color grade (bale) is going to have a thermoform or two, some cups,” Snyder said, adding that the ability to sort all materials has resulted in an increase of more than 300 tons being recovered each month, including small-format plastics such as pill bottles made of HDPE.
Education, collaboration are key to increasing volumes
Collaboration has been a big part of the project from the start, said Amanda Pratt, senior vice president of communications at Rumpke.
“We’re very close to the Ohio State University campus, and we want to make sure it has the resources for the communities, to work with the students with engineering and AI projects, and with the business school,” she said. “We hope to open this up to more universities and schools in the area, and to show pathways to careers in the industry.”
“A big part of this project was building out the 3,000-square-foot education center with exhibits, where we walk people through making choices of packaging at the grocery store that are more sustainable,” Pratt added. “We want to provide that realistic, interactive experience.”
Rumpke also worked with educators and the Center of Science and Industry in Columbus, whose experts provided concepts Rumpke employed in the center to show that recycling efforts make a difference, Pratt said. The building also features a career center for Rumpke’s programs for commercial drivers license, customer service, sales, leadership and continuing education.
“If you’re walking through our education center and our MRF – if you’re not energized about recycling, it’s almost impossible not to be,” Snyder said. “It’s truly an experience and definitely will get you on board as to why recycling is important.”
Miller added that it “reveals what’s behind the curtain in a very attractive manner.”
The education center starts with a simulation of a grocery store, Miller said, where, for example, a fifth-grader can learn to make decisions on what to buy. “You’re using your dollar to vote for those packaging choices,” he said.
The next stop is at the recycling bin, where visitors can play a fast decision-making game and test their knowledge of the system. After that comes the truck, where visitors can move a wheel or push a button to dump the truck into a trommel, then move the trommel to show how it breaks up material. Next is “At the MRF,” which features “magnetic magic” and an eddy current, and visitors can test their skills against the speed of a machine. Then visitors see life-size bales of fiber, aluminum and PET, with an explanation of why the bales are a certain size and weight, who are the end users and what they are making with the bales.
“It’s a way for visitors to get their hands on the process,” he said. “We’re creating a full-circle effect to show what happens to waste from start to finish, and the real product it’s made into, to show that the circular loop is real.”
This transparency also translates into community outreach, Snyder said, with Rumpke conducting “nonstop” campaigns about why recycling is important and combating negative perceptions.
“Sometimes there’s not a lot of synergy or interest in the community, and there are articles in media bashing recycling, and that’s what people are clicking to read. People aren’t wanting to read about a successful industry,” he said.
“If we can get people in the plant to see it, they believe what they see. People who think things all go to a landfill will come into the plant and see the process, then say, ‘I can’t believe I spent 20 years thinking recycling is a joke.’ Getting people into the facility helps gain that trust, and I haven’t seen a scenario where that doesn’t work.”
Miller added that for the “neighborhoods that are not participating, we can either go a farther distance to get more materials or we can talk to our neighbors.” For example, due to having increased capacity, Rumpke is now having discussions with a nearby area of about 5,000 residents that doesn’t offer recycling.
“This capacity is enabling us to up our sales goals,” he said.
Engaging with municipal suppliers
Rumpke also conducts quarterly “Recycling Roundup” sessions, where the “MRF-shed” – comparable to a watershed, composed of the solid waste districts that contribute to MRF input – hears from end users about what happens to their solid waste.
“It’s a day dedicated to educating them so they’re at the forefront, and it creates a lot of synergies, talking about recycling and energizing them to go out into the community,” Snyder said, adding that more than 90% of the material stays in Ohio. “If you teach them, they’ll do it.”
“It’s really powerful to have someone besides Rumpke talk to them about it,” he added.
The new facility has 48,000 square feet of tipping floor space, encompassing three tipping floors, with one designated solely for commercial input. Miller added that the goal is to run more volumes than any other facility in the country.
“The third (and smallest} tip floor is beneficial in that it’s almost a mini-MRF,” he said. “It has a sampling station meant to alleviate the painstaking task of auditing materials and giving feedback to customers.”
AI can generate a pie chart of the material from the second tip floor, providing fast, qualitative feedback so customers can improve their recycling programs, he said.
“The mini-MRF is a huge asset, and we’re going to continue working on that so we can tell people exactly what’s in the material, so they can improve their programs,” Miller said.
The facility is built to accommodate future needs as well, with two overhead cranes currently used for maintenance, but later they can help change out equipment more efficiently. Rumpke also can reprogram its optics with partner Machinex, to suit changing recycling feedstock.
“We know the stream is ever evolving on the fiber and container side, so we realize that we have to have the ability to pivot,” Miller said. “Otherwise you end up being at the mercy of the material that comes in.”
Multifamily challenges
As with any area, a continuing challenge for Rumpke is servicing multifamily housing. Although about 85% of single-family homes have access to recycling, only 37% of multifamily homes do, according to The Recycling Partnership.
“It’s great that people are talking about it finally,” Snyder said. “Multifamily is an area where we as an industry have not done well yet.”
Getting apartment complexes to participate in recycling faces such barriers as cost, logistics and property management buy-in.
“Central Ohio is very aggressive about diversion, creating zoning changes where newbuilds are mandated to provide recycling,” Snyder said. “A lot of buildings have only one chute, so people on the third floor have no ability to separate.”
However, new zoning prevents future issues with newbuilds, he said, and a small company in town performs valet recycling services for many complexes.
“If residents are willing to pay for luxury valet services, we know that they’re willing to pay and that the limitation is something else,” he said.
Rumpke aims to give residents the power to let the landlord know they want the service and to realize they can help make the change, he said. To this end, Rumpke can provide money and containers to help start the program, as a sort of trial for the property manager to see that resources are available and they’re not alone in the effort.
The biggest action Rumpke takes, though, is communicating that multifamily housing is a limiting factor for the community.
“Recycling is not a privilege, it needs to be accessible for all,” Snyder said.
A version of this story appeared in Plastics Recycling Update on August 7.