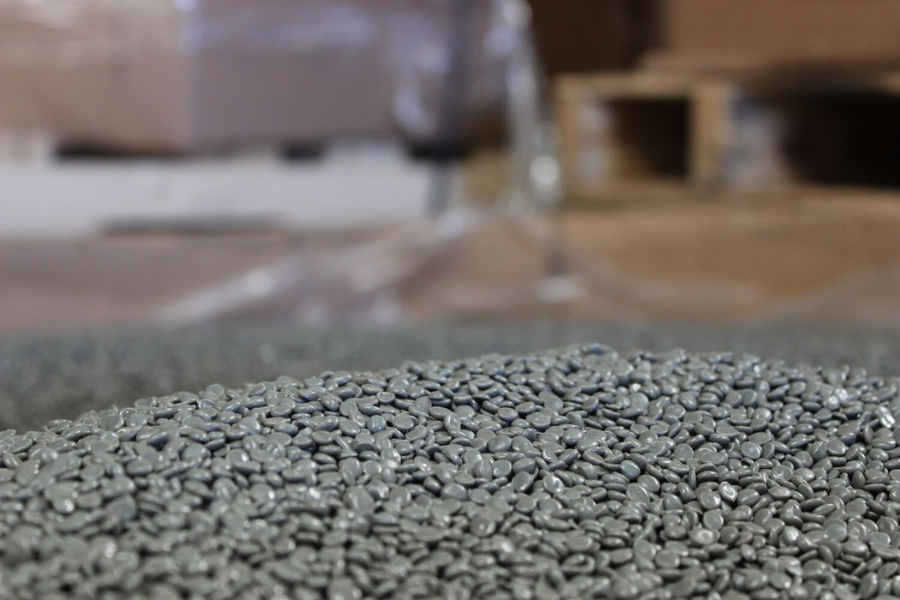
ADS’ plans for improved efficiency include automating material handling, pelletizing upgrades and expanded storage capacity. | Courtesy of Advanced Drainage Systems
Advanced Drainage Systems is in the midst of multiyear, multimillion-dollar recycling debottlenecking efforts that include upgrading recycling equipment and improving materials handling capabilities, an executive said.
The largest plastics recycler in North America, Advanced Drainage Systems (ADS) manufactures plastic pipes, septic systems and other wastewater management products. Hilliard, Ohio-headquartered ADS purchases over 1.10 billion pounds of virgin and recycled resin annually from 400 suppliers, with its plastic feedstock split roughly 50-50 between recycled and virgin material.
In a recent interview with Resource Recycling, Kristen Rinehart, vice president/general manager of recycling for ADS, explained the details behind the company’s ongoing recycling investments, which are mostly focused on HDPE.
Meanwhile, the company recently released its financial results for its 2023 fiscal year, noting that lower polyolefins prices helped increase profits even as executives anticipate a challenging sales environment for its water management products.
Numerous material-handling investments
ADS now has a number of recycling operations under its ownership.
ADS Recycling, which encompasses operations that used to be known as Green Line Polymers, recycles post-consumer HDPE bales at facilities in Clarion County, Pa. and Waterloo, Iowa. ADS Recycling also includes post-industrial plastics recycling plants in Pandora, Ohio and Cordele, Ga.
When ADS acquired Jet Polymers in December 2021 for nearly $50 million, ADS picked up two PP recycling facilities in Georgia and Alabama.
Finally, in 2019, ADS acquired Infiltrator Water Technologies (IWT), which makes PP septic products, in a huge deal worth over $1 billion. IWT had – and continues to operate – a PE and PP recycling facility called Champion Polymer Recycling at its campus in Winchester, Ky.
All told, ADS converts about 360 million pounds of HDPE and 130 million pounds of PP per year into its products, including both post-consumer and post-industrial grades, according to the company’s annual report. The company is the biggest single end market for post-consumer color HDPE.
The recycling operations are currently the focus of “debottlenecking” investments.
“You’re always improving the safety of the environment when you take away the interaction of fork truck traffic and pedestrians.” –Kristen Rinehart, ADS vice president and general manager of recycling
During a May 18 conference call with investors, Scott Cottrill, the company’s chief financial officer, noted that the company’s “investment initiatives are focused on growth in regions like Florida and the Southeast, and increasing investments in productivity, automation, as well as debottlenecking our recycling operations.”
In an interview, Rinehart provided more details on the recycling investments, pointing out they are slated for both ADS Recycling facilities and the pipe extrusion plants that receive feedstock from ADS Recycling. ADS Recycling sends recycled plastic to 35 pipe production facilities in total.
Much of the work involves automating material handling. Recycled resin is often stored and shipped in boxes, which require staff to move and load onto trucks. Additionally, boxes can break or tip, tying up resources for cleaning up pellets, Rinehart pointed out.
To address that bottleneck, ADS is investing in overhead conveying systems and storage silos, she said. That will increase capacity by allowing the company to ship via tankers or train cars, and it improves facility safety.
“No. 1, you’re always improving the safety of the environment when you take away the interaction of fork truck traffic and pedestrians,” she said.
The silos also improve operations at the pipe plants, she said. As ADS has increased pipe production lines, the warehouse space available for storing resin there has decreased. That can make it hard to receive boxes of material. Silos alleviate that concern.
“It’s really the most efficient use of the space under your roof in the manufacturing plant,” she said, adding that silos automatically convey the resin to the extruders, too, avoiding production slowdowns.
Processing equipment improvements
The improvements are focused on recycled HDPE going into piping. Rinehart noted that IWT, which recycles PP into septic system products, is further along with silo storage and efficient freight movement because of its smaller number of facilities in closer proximity to each other.
The material handling and storage projects will allow ADS to maximize its internal recycling and blending capacity.
“[The debottlenecking] opens up capacity for us so that we can provide not just more recycled material to our plants, but actually we’re working on improving the quality, the consistency of our material, so that the pipe plants can run that material very easily,” Rinehart said.
“We actually want to increase the ratio of recycled material to virgin.” –Kristen Rinehart, ADS vice president and general manager of recycling
After those projects, ADS will tackle processing line upgrades at ADS Recycling. ADS plans to upgrade some older extrusion and pelletizing lines that have become a capacity constraint. Wash lines are also targeted for upgrading, although that project is a little further out, she said.
The pelletizing upgrades will position ADS to increase the percentage of recycled resin it uses in its products in the future. “We want to continue to not just grow with our pipe demand,” Rinehart said, “we actually want to increase the ratio of recycled material to virgin.”
She noted that pelletizer lines, including auxiliary equipment, can cost at least $3 million.
“It’s not an inexpensive investment, but the company is very serious about expanding our capacity in the recycling space,” she said.
The majority of the capital projects are expected to be completed by 2028. Rinehart said she doesn’t have a total investment estimate to share, noting that ADS is still getting quotes across the full scope of projects.
Net sales and profits rise
Meanwhile, ADS recently disclosed its financial results for the company’s 2023 fiscal year, which ended March 31, 2023.
ADS reported net sales of $3.07 billion during that period, up 11% from the prior year. The company’s gross profit was $1.12 billion, up 40% from the 2022 fiscal year, according to a press release. The company also published numbers for its fiscal year fourth quarter. During the quarter, ADS tallied net sales of $618 million, down 9% year over year, and gross profit of $222 million, up 17% year over year.
For both the fourth quarter and full fiscal year, ADS said higher prices for its products and “favorable material cost” helped increase profitability. Favorable feedstock pricing last year was a reversal from the 2022 fiscal year, when high recycled resin prices held back company profits.
According to RecyclingMarkets.net, color HDPE scrap prices last year were nowhere near the record high prices they hit in 2021. They fell sharply starting last summer and have only started in the last few months to inch back up.
Looking forward, ADS sees challenging business conditions in the residential and nonresidential construction markets. According to a financial presentation, company executives expect sales and profits to decrease. In anticipation, the company during its fiscal fourth quarter decreased manufacturing and transportation costs.
“We will continue to work cost levers in order to maintain our profitability commitments while also managing our overall network and capital investments so that we are in a favorable position as the market rebounds,” Scott Barbour, president and CEO of ADS, said in the press release.
A version of this story appeared in Plastics Recycling Update on May 31.