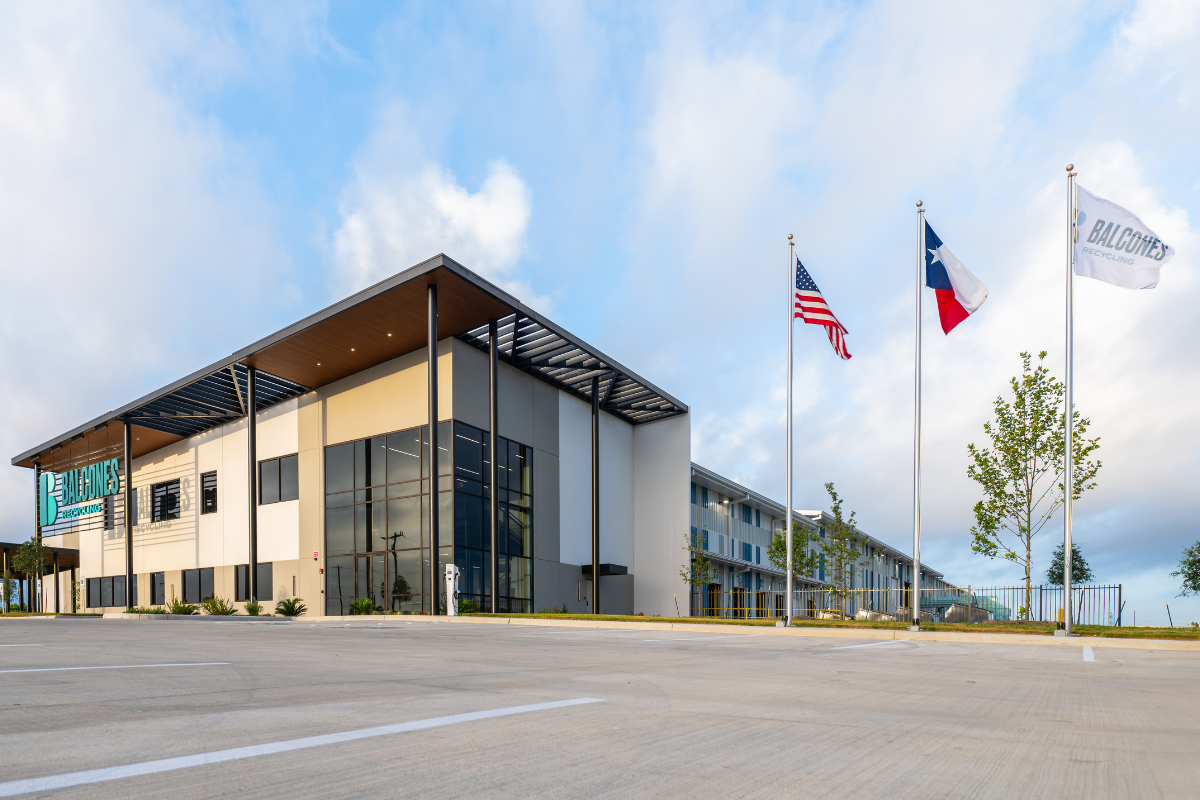
Balcones Recycling opened a $68 million MRF this month in San Antonio, Texas, capable of processing 50 tons per hour of municipal recyclables. | Courtesy of Balcones Recycling
Balcones Recycling has completed a new sorting facility in San Antonio, featuring AI-equipped optical sorters and an innovative experiment to deal with a common MRF contaminant.
Balcones, which is part of the Circular Services umbrella of investment group Closed Loop Partners, this month held a grand opening for the San Antonio facility. The MRF has been in the works since 2021, when the city put out a request for proposals for companies, asking for bids on a 15-year municipal contract.
In April 2022, the city selected Balcones, and the company began developing the $68 million facility. It selected CP Group and decided on a 50-tons-per-hour system, which translates to about 15,000 to 16,000 tons per month or 180,000 to 192,000 tons per year. The contract with the city begins Aug. 1.
Previously known as Balcones Resources, Balcones and fellow Closed Loop Partners portfolio company Sims Municipal Recycling merged late last year and formed a single business, Balcones Recycling. Closed Loop early this year acquired Midwest Fiber, bringing that company’s operations into the Balcones family as well.
In an interview, Adam Vehik, president of Balcones Recycling, and Robb Espinosa, senior vice president of operations, described the MRF’s components, which include machinery to improve safety and an experimental project to remove plastic film that enters the MRF as contamination.
“We like to be on the leading edge of these types of decisions because you learn a lot,” Vehik said. With 17 facilities and many municipal contracts, any lessons the company learns can be deployed on a large scale, he added. “Sometimes it takes a little risk, but you do learn a lot from new technologies.”
Removing the presort for worker safety
The MRF, which handles residential and commercial material together, uses auger screens on both of its lines. That allows the MRF to omit a presorting area, Espinosa explained.
A traditional MRF might have a presort with a number of manual sorting workers at the very beginning of the material line. They are looking for any contaminants and are doing so before any sorting has been done. That can mean trying to locate contaminants when material is piled high on the conveyor line.
Auger screens provide an initial separation by size, creating “unders” and “overs” fractions that make the obvious contaminants easier to spot. In a video outlining the auger screen, CP Group noted that particularly dangerous contaminants like needles are filtered out through this initial size-sorting step, meaning safety improvements down the line.
Balcones was drawn to the idea of removing the presort, which Espinosa added is “probably the most dangerous position, in any MRF, for a human being in our industry.” The company also liked the auger screens because it found they require relatively low maintenance.
Next, the material passes by a series of more traditional screens, including glass breaker screens, an anti-wrap screen and a CP screen, which is used to separate two-dimensional and three-dimensional material.From there, the material goes through a series of optical sorters, which perform preliminary and secondary sorts targeting fiber. On the back end, Balcones has four optical sorters targeting containers and two additional optical sorters performing quality control.
Artificial intelligence in optical sortation
The optical sorters are using imaging technology called Vivid AI, supplied by CP division company MSS, which detects materials on the line and then directs the traditional air jets to send it into a given stream. It’s an alternative to using near-infrared imaging technology, and it’s a growing application of AI in the recycling space: MRF operator Rumpke recently installed AI-powered optical sorters at its new MRF in Columbus, Ohio.
For Balcones, choosing AI visioning technology over near-infrared came down to the material type the facility was looking to sort with those optical sorters.
“We’re not looking for a polymer or a color, we’re looking for objects,” Espinosa said. As an example, he noted buyers of used beverage cans are typically looking for upwards of 99% purity in that stream, so the MRF has to remove all sorts of contaminants that are aluminum but not UBCs – items like food cans, foil and larger objects.
Those applications are where “AI can do what NIR cannot,” Espinosa said.
He added the San Antonio MRF hasn’t installed any robotic sorting arms.
With the numerous optical sorters and AI imaging, Vehik said the equipment provides Balcones with a fully automated container line, which made it a particularly easy choice.
“That makes life a lot simpler,” he said. “We can in fact run that container line autonomously when the rest of the system is down.”
Experimental recovery of a contaminant
In announcing the facility, Balcones wrote the MRF will be “one of the first facilities of its kind with the capability to sort hard-to-recycle materials like film and flexible plastics.” That’s not to say the facility wants those materials, but their presence as contamination is a fact of life. So Balcones is trying one way of removing the plastic and potentially marketing it.
The company plans to install a type of vacuum system called a Venturi vacuum, which will extract the film from equipment on the line, and then to use MSS’s FilmMax technology to remove contaminants from the recovered film. It’ll then be baled and, ideally, sent to buyers.
If the experiment goes well, the process could help turn a contaminant into a marketable product.
“We’re exploring what type of market is out there for it,” Vehik said. “It’s a learning experience for us as well.”