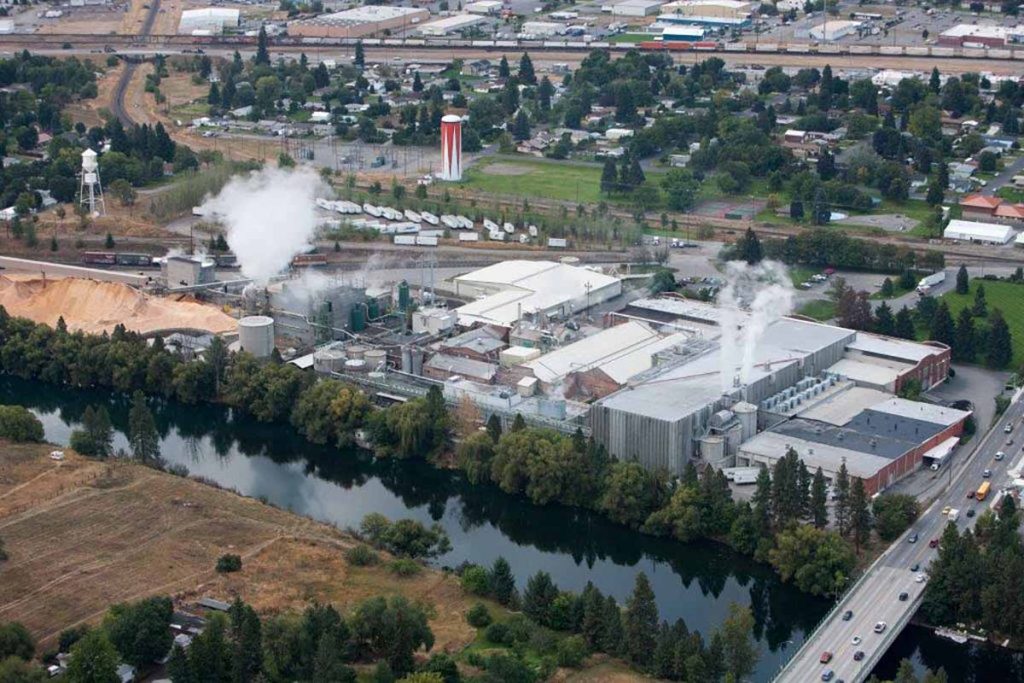
Inland Empire Paper Company operates a 110-year-old paper mill that uses recycled fiber near Spokane, Wash. | Courtesy of Inland Empire Paper Company
A Pacific Northwest paper mill has begun producing new grades of paper made from recovered fiber, a response to changing end markets and growing customer interest in recycled content.
Inland Empire Paper Company recently announced the new packaging sheet made from 100% recycled fiber and lightweight bagstock paper made from at least 30% recycled fiber.
The products will lead to an uptick in recovered material consumption at the Spokane, Wash.-area pulp and paper mill, which has long used recovered fiber but has used less over the years due to quality concerns.
A surge in to-go food sales and e-commerce, both driven by COVID-19 regulations, led the mill to roll out the new products.
“There was a significant change in consumer behavior that was forced because of the pandemic,” said Doug Krapas, environmental manager for Inland Empire Paper, in an interview. “It created potential market opportunities to evaluate and see if we could find a niche in those markets.”
Resurgence follows downturn in recycled paper use
Inland Empire Paper installed an integrated recycling facility at the mill in 1991, allowing it to bring in recovered fiber feedstock. The mill can process up to 350 tons per day of recycled paper products, including newsprint, magazines, shredded office paper and more.
“We did that in response to an increased demand for recycled paper in paper products,” Krapas said. That demand initially stemmed primarily from California, which was an early implementer of recycled-content requirements for printing paper.
In the early days of the mill’s recycled fiber use, recycling programs mostly required source separation, generating a clean stream of recovered paper. The nationwide movement toward single-stream recycling has been accompanied by a “decrease in quality over time since that installation in 1991,” Krapas said.
The EMPIRE bagstock is a recent addition to the company’s product line and contains 30% recycled content.
Declining fiber quality has led the company to source material from across the country.
“Trying to find a higher-quality product has been one of our challenges at this facility,” Krapas said. “That’s one reason we go 1,500 miles to find the highest-quality product we can.”
The quality problems also led the mill to simply use less recovered fiber over the years. From 1991 through 2009, about 60% of the company’s paper was made with recycled content; now, that figure has dropped to between 20% and 30%, Krapas said. And the mill doesn’t buy much material from single-stream programs anymore, he added, looking instead for higher-quality recycling supply streams.
Over the years, there have been discussions at the company about potentially increasing the amount of recycled content in products, said Andrew Moyer, who handles technical sales and customer service for Inland Empire Paper.
“A lot of these questions have been kicked around for a long time,” he said. “I don’t think we necessarily had the customers who were interested in doing more recycled content.”
But over the past year, the pandemic-driven trends were accompanied by an uptick in interest in recycled-content paper grades, Moyer said. Inland Empire Paper was hearing from its customers, which are operations that take in paper and convert it into packaging.
“They’ve specifically asked for anywhere from 30% to 40%, to 100% recycled content,” Moyer said.
“I feel like it comes directly from consumer demand, and those converters who understand consumer demand,” he added.
More stories about fiber
- Plastic-to-paper switch brings complications, panelists say
- Recycled fiber capacity tracker publishes final report
- ‘Continued strong demand’ driving recycled fiber market