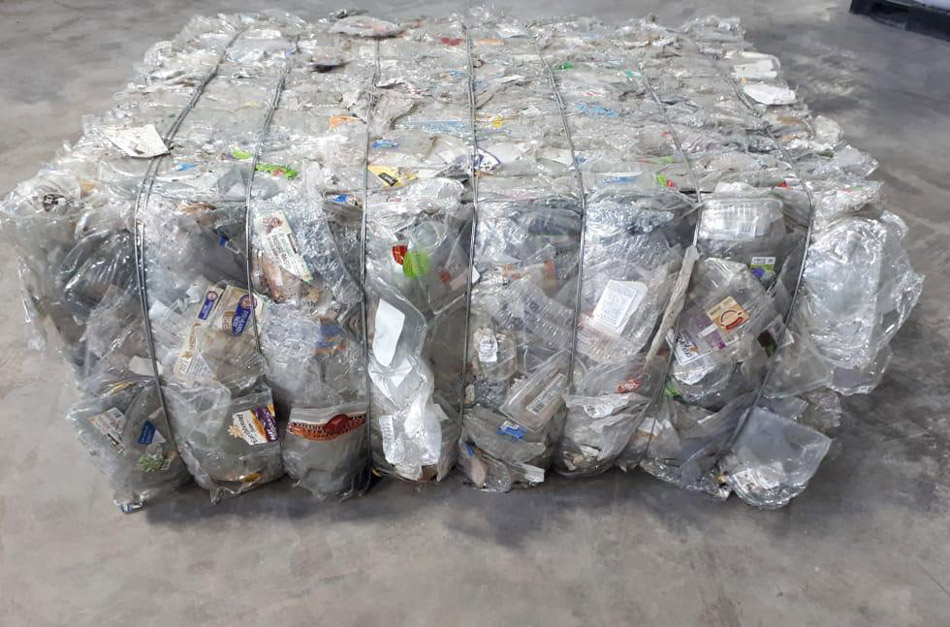
Green Impact Plastics will build a PET thermoform processing facility in California after reclaimer rPlanet Earth agreed to buy its output. | Courtesy of Green Impact Plastics
A Mexican company that developed a system to process post-consumer PET thermoforms will open a $7 million plant in the Los Angeles area. It’s now on the hunt for thermoform bales.
Green Impact Plastics is currently handling recovered PET thermoforms at a site in Ciudad Juarez, Mexico, said company owner Octavio Victal. He noted that since March, the operation has been dialing in its processing system in a partnership with California reclaimer rPlanet Earth.
The two companies recently ran a trial in which 1 million pounds of thermoforms, purchased from California materials recovery facilities (MRFs), were transported to the Juarez facility. Green Impact processed the plastic and then shipped clean flake to rPlanet Earth’s Vernon, Calif. site, where it was fed into rPlanet’s thermoform sheet production line.
Representatives from both companies told Resource Recycling they deemed the trial a success, and rPlanet Earth signed an offtake agreement with Green Impact. That has opened the door to higher output volumes in Juarez and a new facility in California, which is slated to open in the second quarter of 2020, according to Victal.
The $7 million California plant will be located in Vernon, approximately two miles from rPlanet’s facility. The site’s capacity will be 4 million pounds a month, and the existing Mexico plant is scaling up to a capacity of 2 million pounds a month.
“That will give us a nice 6 million pounds of capacity of thermoforms, which will all come back to rPlanet Earth to be turned into a food packaging product,” Victal said. “We are definitely thinking thermoform recycling is going to be the next big thing.”
Strategy for ‘a unique resin’
Though PET recycling is well-developed in North America, the existing infrastructure is focused primarily on bottles. As PET thermoform packaging – often in a “clamshell” format – has grown in use in the U.S., recycling companies have found the material to sometimes be difficult to integrate into the system.
Labels on thermoform containers are often paper-based and affixed with adhesives that make them difficult to separate from the plastic. The characteristics of the PET in thermoforms also differ from what’s seen in bottles. That can cause problems if thermoform resin is mixed with bottle resin at too high of a percentage.
“You’ve got to look at thermoforms almost as a unique resin,” said Joe Ross, co-CEO of rPlanet Earth. “You can’t just lump PET all into the same pot because the sheet to make thermoforms typically starts out with a much lower [intrinsic viscosity] compared with bottles. And because they’re in almost two different stratospheres, to blend them together and homogenize the IVs is almost impossible.”
Such recycling barriers have kept thermoform materials out of many local recycling collection programs. According to Bob Daviduk, rPlanet’s other co-CEO, the state of California has estimated that around 250 million pounds of thermoforms are sent to disposal in the state annually.
Leaders from rPlanet Earth and Green Impact Plastics celebrate the opening of Green Impact’s Juarez, Mexico facility this spring. From left: Bob Daviduk, Joe Ross, Octavio Victal and Juan Pablo Victal. | Courtesy of Green Impact Plastics
For stakeholders that make and use thermoform packaging, the lack of recycling has taken on added urgency, with lawmakers in California threatening to bring on policy that would outlaw packaging types that cannot reach certain materials recovery thresholds.
“In California in particular, the produce growers all have become very concerned,” Daviduk said.
Figuring out a process
In Mexico, Victal and his brother, Juan Pablo Victal, have spent a number of years working through the intricacies of thermoform processing. (Octavio Victal was also co-founder of a bottle recycling operation called Tecnopenales that closed in 2014.)
According to rPlanet’s Ross, Victal has developed a particular expertise on the thermoform front. It made more sense for rPlanet to partner with him than to try to figure out how to best handle the stream on its own.
“There’s all these trade secrets that Octavio’s learned with regard to the size of the flake, how to convey the flake, the wash line chemistry,” Ross noted. “We would have been literally spending five years trying to crack the code on what he’s already learned in his time doing it.”
Victal said his plant in Juarez is 32,000 square feet and uses machinery from Chinese manufacturers. He describes the setup as “a modified bottle wash line.” He noted it relies on an intensive filtration system to handle the pulp from labels and modified spin dryers to help reduce “fines,” the smaller pieces of material that can be problematic in processing.
The facility in Vernon, an industrial-focused city just southeast of downtown Los Angeles, will be 54,000 square feet and will be housed in an existing building. Green Impact is currently finalizing permitting details with the city and is working with an engineering group to get the space ready for equipment installation.
Victal said the company is leasing the building with an option to buy. And he noted the $7 million that will be needed for equipment purchasing is being provided by private equity. He said he also has approached industry group Closed Loop Partners for financial support.
Victal said rPlanet Earth is involved only through the offtake agreement for material – it is not providing funding for the new facility.
“We are using the offtake agreement to leverage our investors,” Victal said. “One-hundred percent of the material is already sold.”
Looking for thermoform bales
Victal said that with rPlanet in place as a buyer and processing plans set, the key now is securing supplies of material from MRFs.
He said he has been working with Plastic Recycling Corporation of California (PRCC) to connect with MRFs and help them see the value of investing in equipment and taking other steps to make thermoform-only bales.
“We’re making sure they understand there’s a market for it,” he said. “We want to flush out as much volume as possible.”
He noted that when the California operation comes on-line, the Mexico site might be able to start accepting bales from other regions of the U.S.
Daviduk of rPlanet said the the partners expect economics to drive the thinking of MRFs. Currently, MRF operators are often paying to send thermoform material to disposal, or they are lowering the quality of PET bales when they mix thermoforms with bottles.
Having a clear market “for those bales creates not a large revenue stream but at least a revenue stream that presumably will entice them to invest in more automated sortation,” Daviduk said. “It’s a good story – the fact that MRFs can say, ‘Instead of sending this material to landfill, it’s now getting recycled.’ That’s good for everyone involved.'”
More stories about plastics
- Greif streamlines operations through asset sales
- Nonprofit coalition explores challenges of film plastics
- Colorado Summit for Recycling taps trending topics