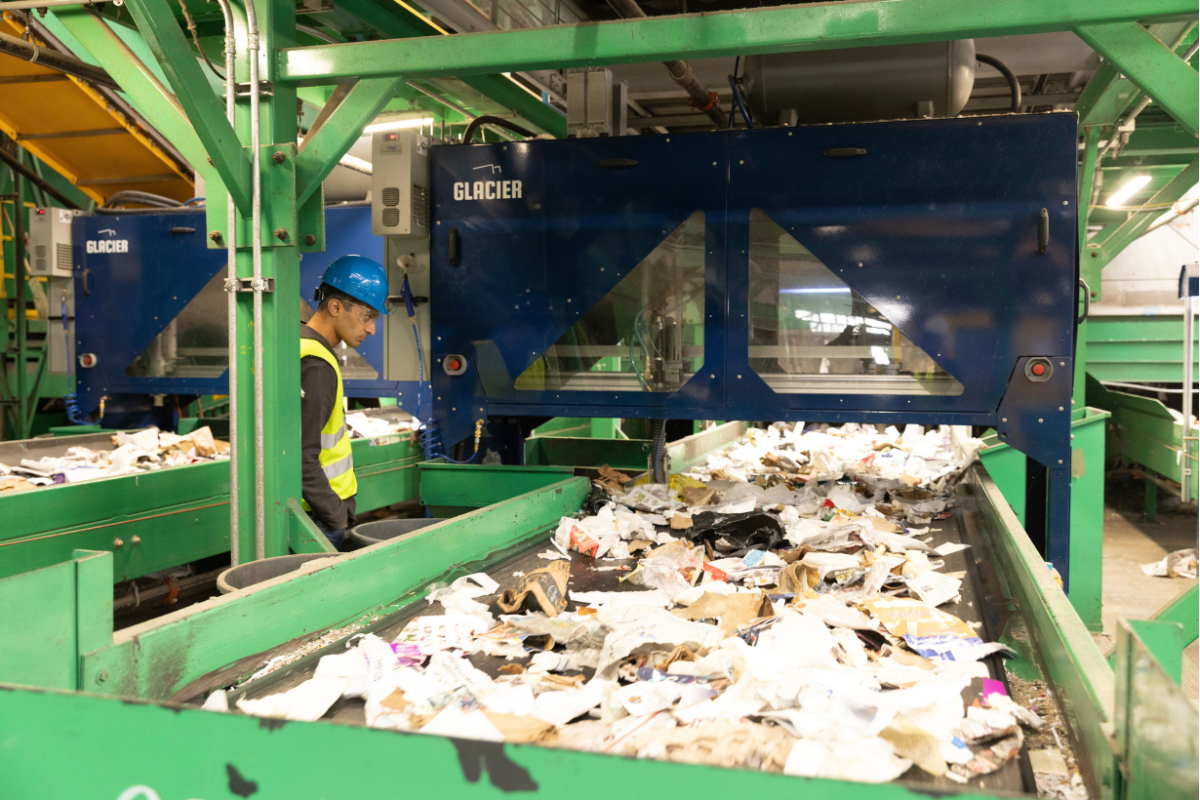
Robotics from Glacier can be made to fit any belt width and can target more than 30 distinct materials. | Courtesy of Glacier
The co-founders of emerging sortation robotics supplier Glacier say their robots provide an immediate quality benefit with a small footprint: They can be placed anywhere a manual sorter would be stationed.
Founded in 2019, tech startup Glacier on March 6 announced it received $7.7 million from New Enterprise Associates (NEA) and Amazon’s Climate Pledge Fund, an investment arm of the e-commerce giant. Glacier is an emerging player in the MRF robotics industry, and its latest funding brings the company’s total capital raised to $13 million so far since its launch.
In outlining its investment, Amazon wrote that Glacier’s technology “can help improve the quality of recycled content so that more post-consumer material is available for use in new packaging. Longer term, it can also enable recycling for more types of packaging and materials than are not currently recycled.”
With a staff of 22, the equipment supplier is based in San Francisco, where it also designs and assembles and tests its robotic systems. Glacier additionally works with a handful of contract manufacturers, who do tasks like welding frames and building motors within the robots. The company is currently working with about two dozen customers across 10 states, many of which are recycling facilities.
Resource Recycling spoke with Glacier co-founders Rebecca Hu and Areeb Malik to learn more about their compact robotic systems and why they are drawing investment attention.
Spurred by market strife
Both co-founders have backgrounds working in the tech space, and when they met, both were wanting to work more specifically on sustainability-focused ventures. They narrowed in on the recycling sector and began developing equipment for the sortation field, driven by a few observations.
The team saw opportunities in both customer demand and technological advancement. It was 2019, and the recycling industry was struggling in the wake of China’s pullback from the export market. Quality was key: MRF operators needed to reduce contamination and to do it quickly. In a lot of ways, Glacier launched because of the opportunities created by China’s National Sword campaign, Hu says.
“This industry that has done things a certain way for many decades, is actually at a moment when everyone is really excited to see what is out there and explore new technology,” she said.
Additionally, the market challenges lined up with advancement in artificial intelligence (AI) capabilities, to the point that Malik and Hu determined they could have a substantial and immediate impact in that part of the industry by using emerging technology. There was a clear opportunity to take AI and robotics and “start applying it to the sortation challenge,” Malik said.
Hu added that working to enhance the abilities of the existing MRF infrastructure was an accessible way to quickly bolster the recycling system, as opposed to moving upstream to tackle consumer recycling habits, for example.
“The immediacy of the potential impact was really appealing,” Hu said.
Compact robots allow for quick boost
Glacier’s interest in immediate improvement also played into the choice to supply robots, as opposed to other sorting technologies. Malik noted that optical sorters are a strong technology, but that they can often require a full MRF retrofit to install. The robots Glacier supplies, on the other hand, can be dropped onto a quality control line without substantial facility changes.
“Any place in your facility that you have a sorting station, our robot can go in and provide that additional sorting power,” Malik said.
The company’s robots can be installed on conveyor belts of any width, Hu added, avoiding the need to double up with two robots to accommodate wider belts, for instance.
Glacier’s robots perform an average of 45 picks per minute, a metric the company calculates from units installed inside MRFs. But Hu explained that metric can be more complicated than it sounds: Sometimes it is reported as hypothetical picks per minute in a lab, sometimes it refers to how many times a robotic arm attempts to grab a piece of material off the belt. She noted that for MRF operators, the only thing that matters is the physical number of items the robot correctly puts in its proper location.
Hu added that although picks per minute is an important metric, she recommends MRF operators consider what they really need the robot to do, especially how many picks they actually need the robot to perform.
Ultimately, she proposed a couple variations on the metric: picks per minute per dollar spent and picks per minute per square foot the equipment occupies. Those considerations can help ensure a MRF installs the right system for its actual needs.
Glacier’s data analytics system is an equally important component of what the company offers. In fact, Hu says the team at one time considered focusing entirely on the AI system rather than robotics, but decided they wanted to also provide the tool (robotics) to put the AI data into action.
Besides enabling a general expansion of the company, Glacier’s recent funding will aid in building up the data analytics and material identification capabilities. It currently identifies 30-plus materials, including fiber, PET, HDPE, black plastic, thermoforms, aluminum, aseptic containers and more.
“We want to continue to expand that list very thoughtfully,” Hu said.
A version of this story appeared in Resource Recycling on Mar. 12.