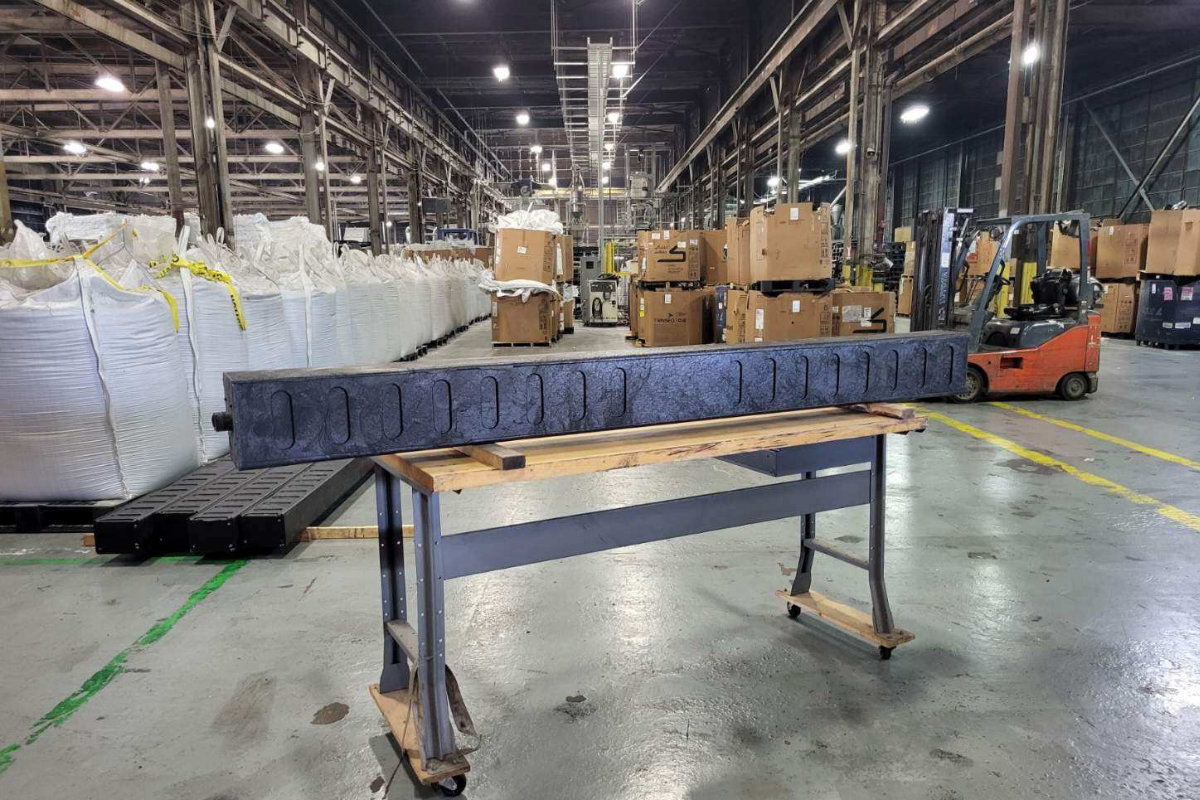
A Triton Tie at the Granite Peak Plastics campus in St. Louis. | Courtesy of Triton Ties
Granite Peak Plastics foresees its newly unveiled railroad tie product eventually providing a market for all of the plastic reclaimer’s post-consumer PE.
The St. Louis-based plastics reclaimer on Oct. 11 announced the release of Triton Ties, a glass-fiber-reinforced composite railroad tie. Greg Janson, CEO of both Granite Peak Plastics and Triton Ties, said the ties, which are intended to replace wooden ones, are currently undergoing evaluation by railroads.
Janson explained the ties are made of a proprietary resin formula that includes post-consumer polyolefins and glass fibers. The washed and recycled plastics could come from mixed bulky rigids, small rigid containers, and films and flexibles.
Granite Peak has two buildings at its St. Louis campus, including a 70,000-square-foot building that houses its plastics wash line and a 60,000-square-foot building that holds a new extrusion and low-pressure injection molding system for making Triton Ties. This building also houses an existing post-consumer plastic recycling system.
Janson said the Triton Ties system involves an extruder feeding plastic into a low-pressure injection molding system. He calls the continuous-feed system “precision extrusion,” because it precisely meters the different ingredients for the ties and introduces the glass fiber reinforcements in such a way that they maintain their integrity.
“Because of the continuous feed system, we end up with a very consistent tie,” he said, adding that the blend can be changed with the push of a few buttons.
The new, custom-designed equipment, which was installed earlier in 2023, can also be switched over to melt filter and pelletize post-consumer PP, he said. In fact, it’s currently working 24 hours a day, five days a week pelletizing plastic.
Because of that flexibility, the capital investment will bring in revenue until the Triton Ties market develops, he explained.
A Triton Tie undergoes in-house testing for strength and stiffness.
“That allows us to have our existing plastic business while we patiently develop the rail tie business and really deliver the product that the customer wants,” Janson said.
‘Will be a huge market’
Triton Ties is not the first composite railroad tie containing recycled plastic to hit the market. In 2016, Janson helped develop a recycled-content railroad tie now produced and sold by a completely separate company called Evertrack. His goal at the time was to create a market for mixed polyolefins. Janson said he sold his equity stake in Evertrack in 2019, and after the expiration of a non-compete agreement, began work on Triton Ties.
He said the PCR polyolefins market is most successful in vertically integrated enterprises that buy plastic by the pound and sell by the part. Examples include Advanced Drainage Systems (ADS), which recycles HDPE into drainage products, and KW Container, which recycles PP into paint cans.
The federal government has also signaled support for recycling post-consumer polyolefins into infrastructure applications. Earlier this year, the National Academies of Sciences, Engineering and Medicine published a report that called recycled plastics “an underutilized resource,” and it pointed to railroad ties as one promising end use for post-consumer plastics.
For its part, the Triton Tie has already undergone internal and third-party testing, and railroads are currently doing their own evaluations.
The product needs to meet the railroads’ specifications, and the product must be consistent, he emphasized. “We want to be very thorough and very patient with this part and make sure we’re giving the customer what the performance of the part requires,” he said
“Regardless of its environmental attributes, it has to perform,” he said.
Still, the environmental benefits are substantial, he said. Each mile of track has about 3,250 ties. That would mean consuming 276 tons of plastic would be needed for a mile of track supported by Triton Ties. The ties also save thousands of gallons of creosote and reduce harvesting of hardwood trees. While they have a higher upfront cost, the Triton Ties are estimated to last substantially longer than wooden ties, particularly in high-moisture environments (50-plus years, compared with 10 to 20 years in high-moisture environments for wooden ties), saving the railroads money over the long term, he said.
Janson said his goal is to build a plant that would be open in the St. Louis area by the third quarter of 2025, consuming 85 million pounds of recycled plastic and producing half a million ties per year. That many ties would negate the need for nearly 1.2 million gallons of creosote and the cutting of 125,000 hardwood trees. Overall, 23 million wooden railroad ties are replaced in North America every year.
“This will be a huge market,” he said.
Eventually, Janson anticipates Triton Ties consuming all of the PE that sister company Granite Peak produces, he said, adding that Granite Peak would sell PP resin to outside customers.