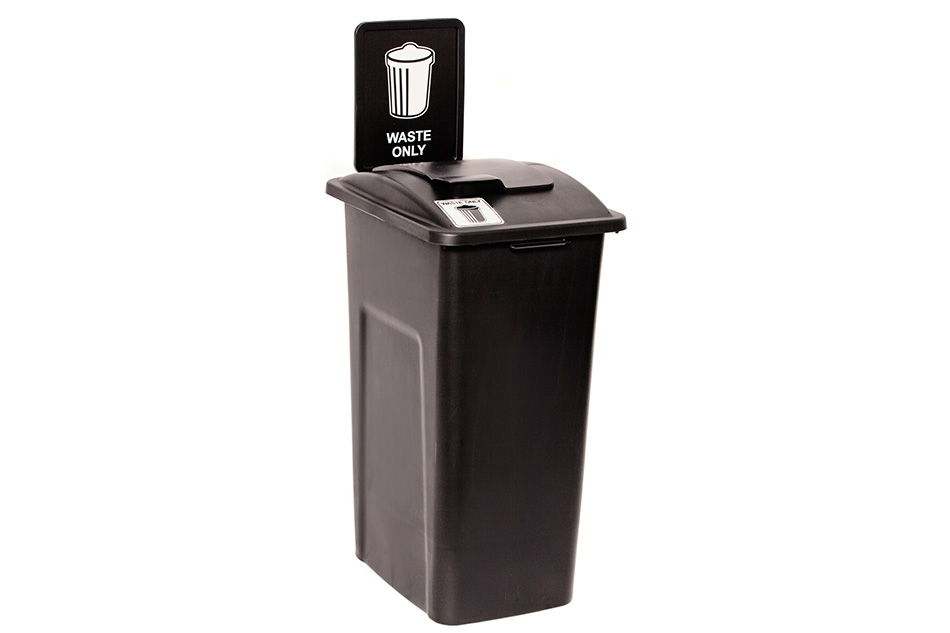
For injection molding, Busch Systems is now taking in at least 44,000 pounds of post-consumer plastic a month. | Courtesy of Busch Systems
Garbage and recycling container maker Busch Systems recently announced it has developed additional products made from 100% recycled plastic. An executive explained how the Canadian company continues to boost recycled content.
Barrie, Ontario-based Busch Systems has been molding containers with recycled plastic for about a decade. The end user has steadily increased its use of recovered polyolefins over the years and, in mid-April, announced a significant expansion of its containers made with 100% post-consumer polyolefins.
“We a sustainable-based company, so for us it makes sense to be able to help close the loop,” said John Lajner, operations manager for Busch Systems. “It’s our goal to use [recycled plastic] in everything we manufacture.”
Lajner explained how the company has been able to use more recycled PE and PP, as well as lingering limitations for post-consumer material. Founded in 1985, Busch Systems manufactures garbage, recyclables and organics collection containers used by businesses, institutions and governments.
Stable, high-quality supplies
Around 2005, the company began buying recycled plastic lumber and using the material in its outdoor public container stations. Around a decade ago, Busch started using recycled plastic in injection-molded containers at up to 25% recycled content, Lajner said.
A key to growing the percentage since then has been finding consistent suppliers of higher-quality recycled polyolefins, he said. Post-consumer plastic used by Busch Systems for injection-molded containers comes from Ontario’s Blue Box program, a curbside collection system that’s funded by both municipalities and producers and serves nearly 13 million Canadians.
Sorting and cleaning technology used by reclaimers handling Blue Box material has improved, allowing them to better separate HDPE from PP and remove contaminants such as paper, which can clog injection-molding machines, Lajner said.
By working with a number of suppliers to obtain plastic with better melt flow properties, Busch Systems was able to boost the number to 50% recycled content. The first 100% recycled container actually came as early as 2014, but it was a very limited production run, Lajner said.
More recently, by purchasing higher-quality plastics from a particular supplier (Lajner wouldn’t disclose the company), the company has produced a number of different products made of 100% post-consumer plastics.
“We were fortunate enough to develop a good relationship here in Canada, and we now have a good supply,” he said.
For injection molding, Busch Systems is now taking in at least 20,000 kilograms (44,000 pounds) of post-consumer plastic a month, storing it in silos, Lajner said. That doesn’t count Busch Systems’ blow-molding operations, where post-consumer PE is also used. Additionally, the company uses post-industrial LDPE in rotational molding.
Overcoming hurdles
Challenges remain in using post-consumer plastic, including colors available. Busch Systems is working to incorporate more post-consumer material into lighter-colored containers, but post-consumer plastic tends to come in gray or dark gray colors, which limits their use to darker-colored containers, Lajner said. To make a yellow receptacle, for example, the company would probably have to use post-industrial plastic.
Odor from post-consumer plastic is also an issue, particularly when containers are used indoors. That being said, additives developed over the past decade or so have allowed reclaimers to improve the smell, including shifting it to a vanilla scent, Lajner said.
“It’s an ongoing development with us and our suppliers,” he said. “When you think you’ve got it all figured out, of course something else changes and you have new development that needs to go on, or there’s new demands from our customers that push you harder.”
As far as pricing, the post-consumer plastic is expensive, and there’s no cost advantage to use it over virgin plastic, Lajner said. However, according to Busch Systems, its prices for containers didn’t change when the company made the transition to post-consumer plastic.
“If there’s no commitment on our side as consumers of resin, then we’ll never clean up the oceans, we’ll never stop the landfills, we’ll never do all the right things that we should be working toward,” Lajner said. “Unfortunately, sometimes that’s not the cheapest way to do things, but, ethically, it’s the right way to do things.”