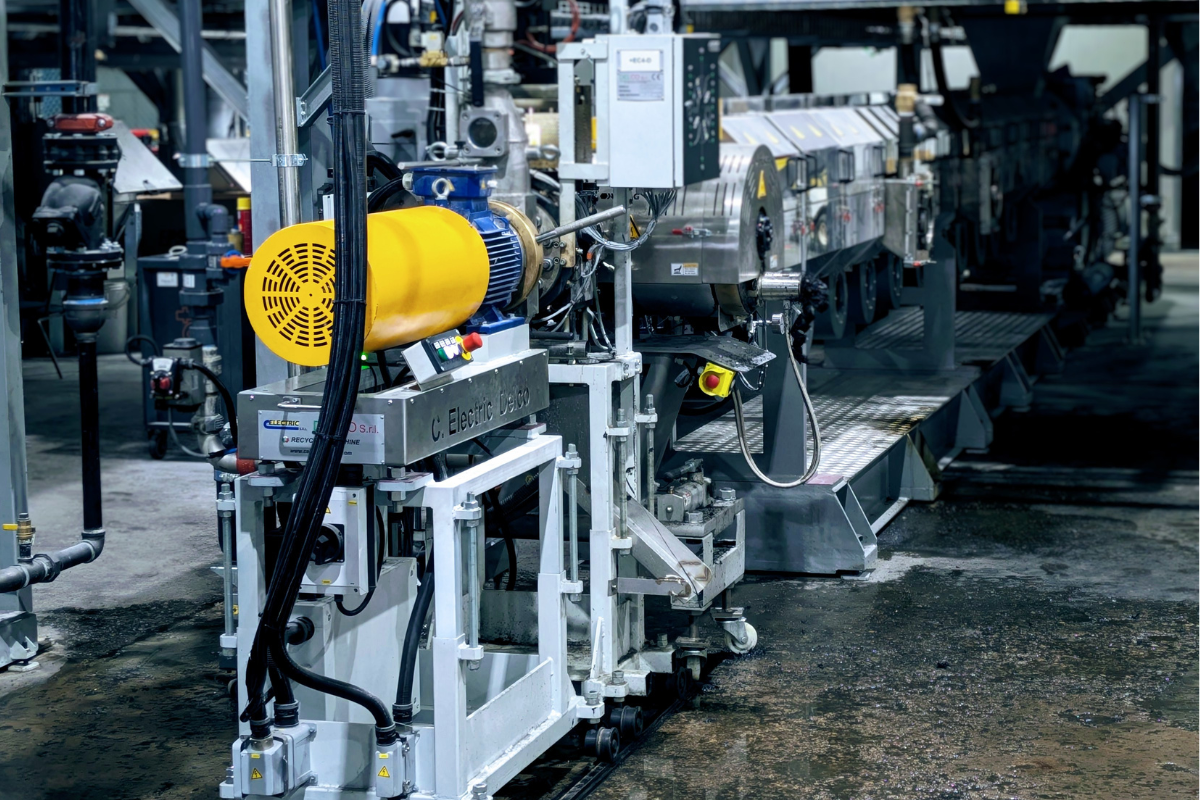
Plastic Recycling, Inc. has invested a total of $17 million of dollars into extrusion lines and labs to create recycled ABS and PS compounds from e-plastics. | Courtesy of Plastic Recycling Inc.
Midwest-based Plastic Recycling, Inc. is looking to provide compounds for OEMs and automotive manufacturers that fit a wide range of specifications and just happen to be made from e-scrap.
The company is offering three new polystyrene and three new ABS compounds from recycled electronics. Marco Meloni, PRI’s chief operating officer, told E-Scrap News that the goal is to “work together with the OEMs at the origin of the products, not just offer them an alternative material.”
“We can substitute virgin today, but now we can also start working at the origin, when the molds are not even done,” he said.
President and co-owner Brandon Shaw said PRI got interested in e-plastics five years ago because “we saw this opportunity with no domestic solutions.”
“We’re trying to be that domestic solution to solve this worldwide problem,” he added.
Meloni said the vision started by asking what the difference is between a recycling operation and a virgin operation, and “it was the knowledge, the know-how, the equipment and the staff – so we got that.”
First came a $10 million investment into two new extrusion lines, one with a single-screw extruder and the second with a twin-screw extruder. The lines have automatic feeding systems, pre-blenders, post-blenders, automatic screen changers and more. The project added 70 million pounds of new capacity. PRI also invested about $3 million on a well-outfitted lab. Along with other tweaks and changes, the company has overall spent about $17 million on the project.
The compounding lines, which are fully automated, allow PRI to create “consistent, repeatable, really high-level resin that fit the biggest volumes and opportunities of the brand owners,” Meloni said.
Now the company is vertically integrated, taking in e-plastic bales from electronics processors and handling the rest – sorting, shredding, extruding and compounding – in-house. PRI added more employees, Meloni said, including scientists to do research and development.
“We are not just recyclers, we are compounders that choose recycled streams,” Meloni said.
Shaw noted that the compounding improvements represented the final investment step, but it was important to start at the beginning of the process and make improvements all the way through.
“First you need to purify the stream to turn into the pellets,” he said. “You can’t just invest in one.”
PRI’s 600,000-square-foot Indianapolis facility had the space to add the new equipment without needing to add square footage. The company’s overall volume is about 220 million pounds across its nine plants. It also handles food-grade polypropylene.
Looking forward, Meloni noted that an ever-present goal is to improve quality while reducing the quantity of additives needed, “to stay competitive but also sustainable.”
“We want to be a real player in the feedstocks for all injectors at the highest level – OEMs, Tier 1s, brand owners,” Meloni said.
To do that, Shaw said the company plans to increase overall capacity, with a focus on e-scrap collection and extrusion.
“There’s so much material here in the U.S., and with all these Jan. 1 export restrictions, people are just calling us left and right,” Shaw said, referring to the Basel Convention amendments that recently came into effect.
While the automotive industry has been very receptive to the new compounds, it’s a little more complicated with OEMs, Shaw said. They have mandates around recycled content and are seeking recycled resins, but “the bad thing is there’s still not a lot of the molding done in North America.”
However, with the trade restrictions and potential tariffs, Shaw said PRI does see the possibility of onshoring molding, putting the company in a solid position to provide its pellets. And with Meloni’s experience with European markets, PRI is also considering selling abroad.
“This problem isn’t just in North America, it’s international,” Shaw said. “The biggest thing is how do we partner with these brands that have these sustainability commitments? They make this waste that’s put out in the system – how do we help them close the loop on that?”