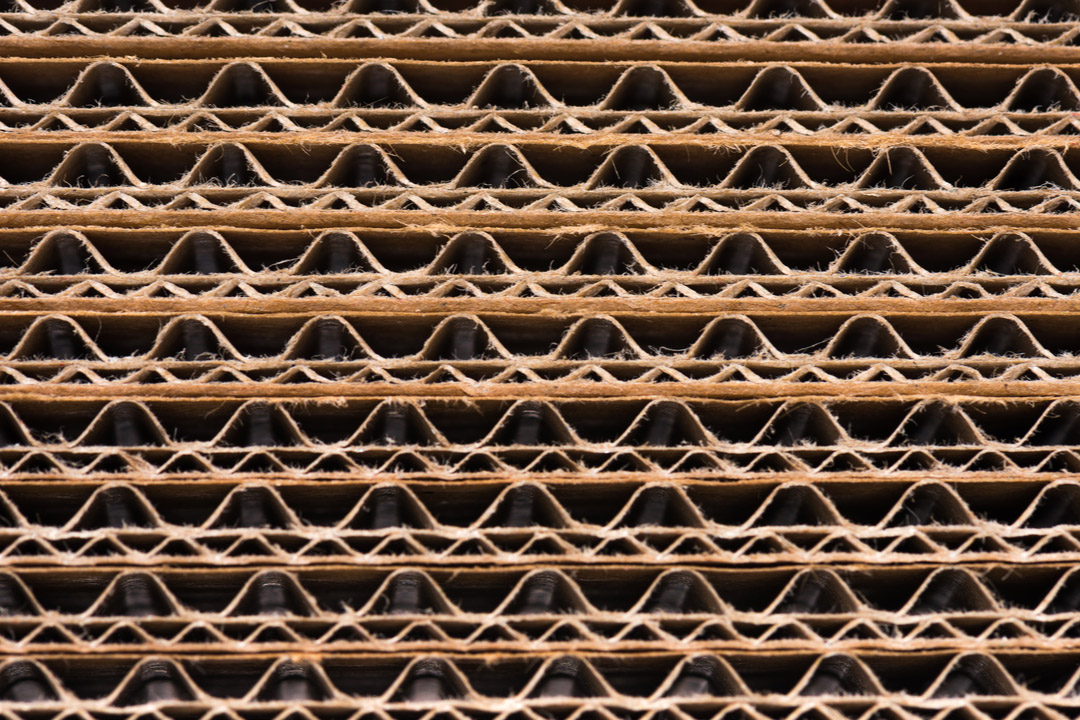
North American fiber end markets saw stronger demand and expect declining costs in the near term. | DenisNata/Shutterstock
Major North American recovered fiber end users saw stronger containerboard demand during the third quarter of the year, according to recent earnings calls. Most are also projecting declining recovered fiber costs through the end of the year.
These are some takeaways from earnings releases of the continent’s largest publicly traded paper firms that use recycled feedstock.
“Very strong demand throughout the quarter led to all-time quarterly records for containerboard production, total box shipments and shipments per day,” said Mark Kowlzan, CEO of Packaging Corporation of America, in the company’s Oct. 22 earnings press release. The previous production record was set just last quarter.
Because of the strong demand, even with record quarterly production of 1.3 million tons of containerboard, the company wasn’t able to hit its inventory targets, Kowlzan added. The Lake Forest, Illinois-headquartered company reported corrugated packaging shipments were up 11.1% over the same quarter in 2023.
Memphis, Tennessee-headquartered International Paper similarly benefited from a “moderately improving box demand environment,” CEO Andy Silvernail said in an Oct. 31 earnings press release.
The company sold 772,000 short tons of containerboard during the quarter, up 14% from the same period a year earlier. And its economic downtime at mills dropped from 458,000 short tons of downtime during the third quarter of 2023 to 138,000 short tons during the same period in 2024.
The company’s recycling division sold 532,000 short tons of recycled commodities during the quarter, down 4% from the second quarter of the year but flat year over year.
The North American paper giant is in the final stages of merging with European packaging firm DS Smith. During the earnings call, Silvernail said he anticipates the deal will close during the first quarter of 2025.
Input costs during the quarter were higher year over year, in part because OCC cost roughly double what it did during the same quarter in 2023. But International Paper projects the recent decline will mean lower costs through the end of the year. Feedstock costs “are expected to be lower driven by recovered fiber and wood costs,” the company stated in a financial filing.
Hartsville, South Carolina-based Sonoco reported a similar outlook, anticipating North American economics “will be positive in the fourth quarter as contract pricing has been reset and input OCC costs are lower.”
Graphic Packaging CEO Mike Doss said he anticipates the company’s massive Waco, Texas, recycled paper mill will start up during the fourth quarter of 2025.
“Once Waco is up and running, we’ll be able to service the entire North American market with the highest quality coated recycled paperboard from two locations in Michigan and Texas,” Doss said during the company’s Oct. 29 earnings call.
Carrying a $1 billion price tag, the company’s Waco facility has been in development since early 2023. The mill is replacing several older Graphic Packaging facilities and will also bring a net capacity increase. It comes after a similar ambitious project that installed new recycled paperboard equipment in Kalamazoo, Michigan.
Outside of North America, Chinese paper giant Nine Dragons on Oct. 22 released its 2024 fiscal year annual report, covering the 12 months that ended June 30. The company is publicly traded on the Hong Kong Stock Exchange.
Nine Dragons reported it consumed more than 14 million metric tons of recovered fiber throughout the year. It has a goal to hit 16 million metric tons by 2030.
The company reported its total production capacity across all products totaled 24.8 million tons per year. That includes 13.4 million tons of linerboard, 3.7 million tons of medium, 2.6 million tons of coated duplex board, 1.7 million tons of printing and writing grades and 3.4 million tons of specialty paper and pulp products.
In the U.S., where the company maintains operations in Maine, West Virginia and Wisconsin, the company’s capacity totaled 1.3 million tons per year as of the 2024 fiscal year. That includes 900,000 tons of grades for printing and writing and specialty paper products, as well as 400,000 tons per year of recycled and wood pulp capacity. Out of 25,410 full-time employees, 541 are in the U.S., or just 2% of the company’s full workforce.
The company anticipates both “opportunities and challenges” in the 2025 fiscal year, which is now well underway.
“The United States is returning to cutting its interest rate after four years, while the Chinese government has launched a batch of policy measures to stabilize the economy, expand domestic demand and promote consumption,” the company wrote. “It is believed that with the intensive implementation of the relevant policies, consumer confidence will be further boosted by the combined efforts of all parties and the internal impetus of consumption, which will in turn promote the growth of demand in the packaging paper industry.”
However, it added, the “competitive pressure of zero tariff on imported paper, the increased supply of new capacity from the peers, the necessarily gradual recovery of economic and consumer confidence and the complex and volatile international situation have all added uncertainties to the current business environment.”