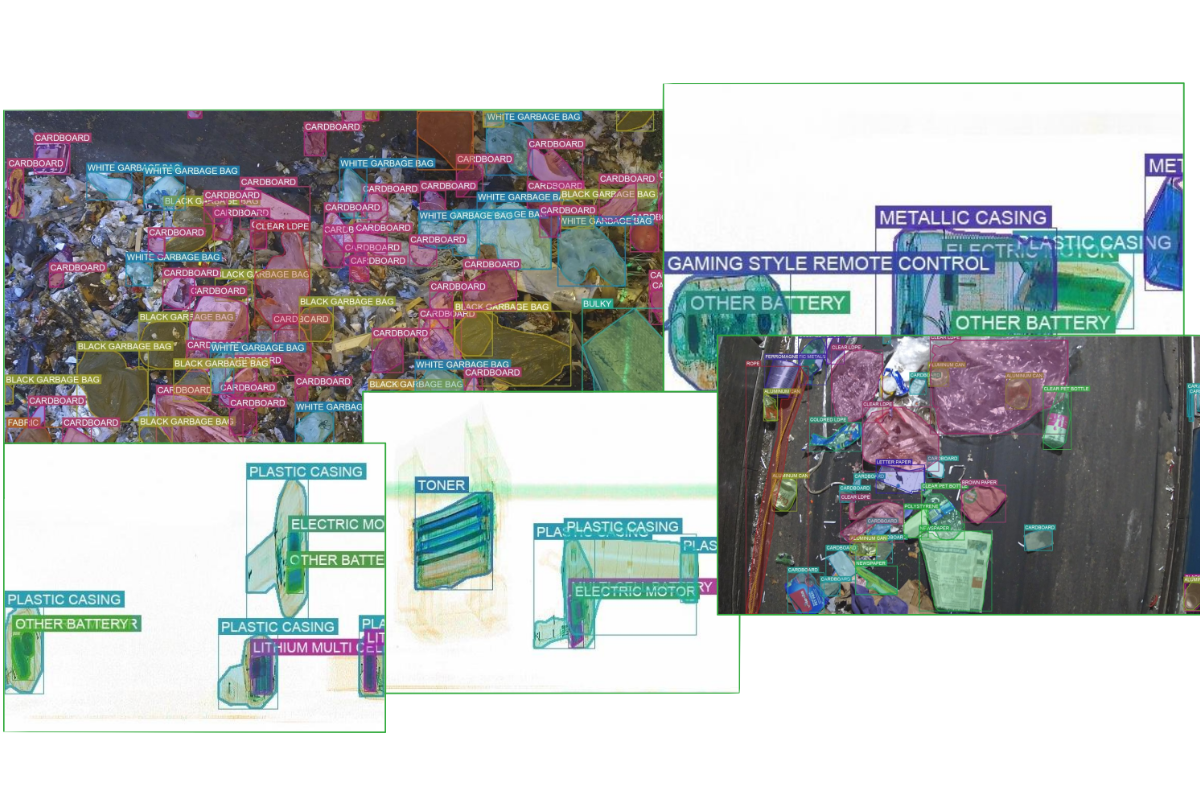
BinIt’s Visia system can combine cameras, X-rays and artificial intelligence to spot batteries hidden under or inside recyclable material streams. | Courtesy of BinIT
A young technology company’s imaging system combines cameras, X-rays and artificial intelligence to allow recycling facility operators to peer into their waste streams and remove the hidden menace of lithium-ion batteries and other hazards, the company’s CEO said in a recent interview.
The idea seems to be catching on: BinIt’s system is up in or slated for a dozen facilities, and the company announced Monday that it received $6.4 million in seed financing from multiple investors to continue meeting existing customers’ needs and expand to more facilities.
CEO Raghav Mecheri called the technology a solution to the biggest problem facing the recycling industry today.
“Whatever you might be or whatever type of facility you might operate, at the end of the day these are a massive fire risk,” he told Resource Recycling last week, referring to batteries and similar items. “Being at the forefront of stopping battery fires at MRFs is probably the thing that excites us the most.”
‘True material visibility’
Recycling facilities experience thousands of fires every year, and rechargeable batteries are among their chief causes, according to a recent report from the National Waste Recycling Association. MRFs of all kinds are a perfect storm of battery risk thanks to their frequent crushing and baling of cardboard and other materials that easily obscure wayward devices from workers and automated sorters alike.
BinIt gets around that problem by reaching beyond the visible spectrum of light. Like an airport’s baggage scanner, the system, named Visia, can use X-rays to peer through fiber, plastic and even some metal and identify the unique signatures of batteries, sharps or other items. It then alerts facility personnel, such as by app or with a laser that spotlights the offending item on a conveyor.
Mecheri said the system has a greater than 95% capture rate and continues to learn, gaining experience from all of its locations. When facility managers combine BinIt’s visible light and X-ray capabilities, they can get a comprehensive picture of what’s flowing into the building.
“We describe ourselves as the first true material visibility business,” he said. “That’s proven to be a game-changer for customers.”
Among those customers is evTerra, an e-scrap company with locations in Atlanta, Chicago and Las Vegas. Jeff Gloyd, who was then evTerra’s president, spoke on the partnership with BinIt during last year’s E-Scrap Conference in September. He left his position at evTerra in October and joined BinIt’s team earlier this month.
Unlike municipal recycling facilities, e-scrap facilities may want to keep the batteries and other hazardous objects that pop up in their streams, but they also want to separate them before a spark or flame erupts, he noted.
“It’s batteries, it’s propane tanks – which somehow end up in our waste streams all the time – and it’s toner cartridges,” Gloyd told the conference crowd. The search and removal process is typically manual, time-consuming and prone to everyday human mistakes, he added, and BinIt offers a better option.
“If you factor in downtime and risk and any injury that could happen to a potential employee or something, the ROI is pretty short,” Gloyd said in September.
Working toward growth
BinIt’s roots reach back to Columbia University in New York City, where Mecheri and several partners first began working on an AI-assisted waste-sorting system in 2019. Mecheri graduated in 2022; his freshman-year roommate, James Bollas, is BinIt’s co-founder and chief technology officer.
The team came to see recycling as one of the most important sectors, Mecheri said, and after graduation they set about visiting every MRF they could, doing odd jobs like fixing internet connections to make themselves useful while they observed the industry and its problems.
The Visia system launched in January 2023, initially using only visible-light cameras. But again and again facility managers asked for a way to see through piles of material. Witnessing a battery fire firsthand was “a kick in our backside,” Mecheri said.
In the short term, Mecheri hopes to grow from a dozen customers to at least 30 by the end of the year. Past that, he wants facility managers to see more potential in the system than just snagging batteries. With a complete and detailed view of material streams, “there is massive scope for optimizing operational decision-making,” he said.