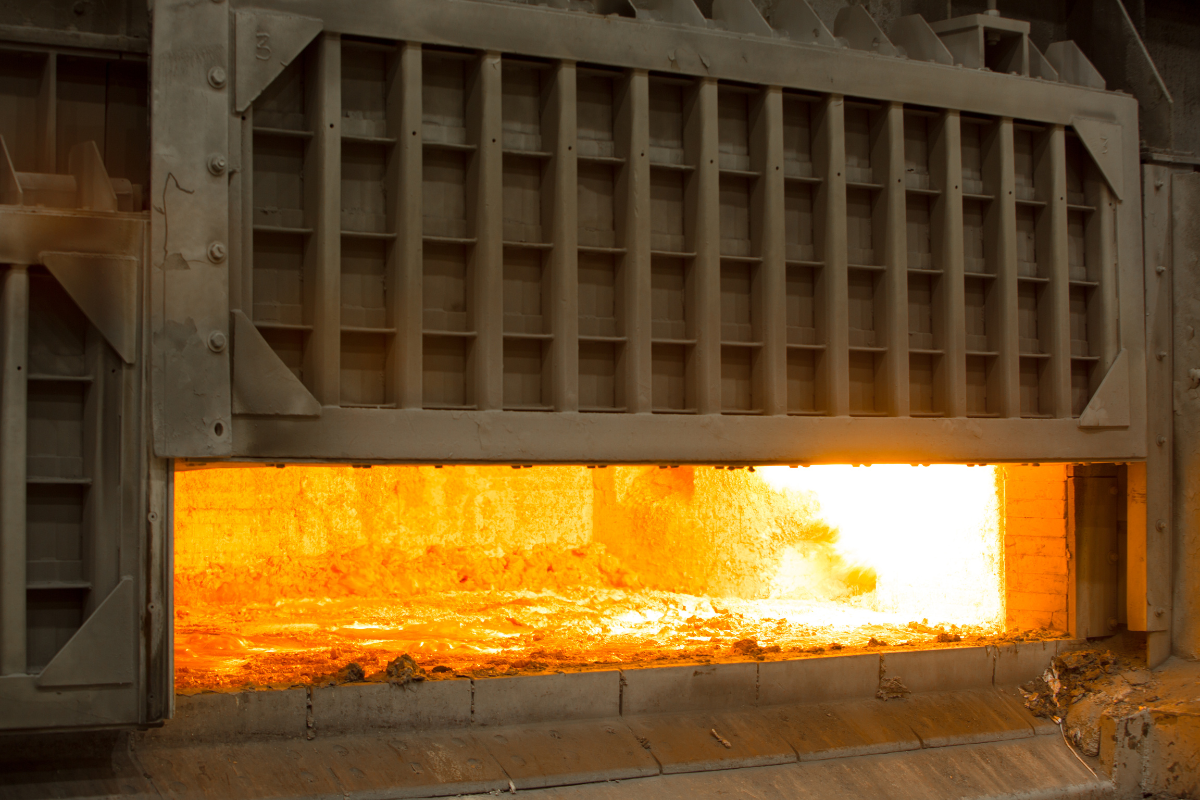
An example of an aluminum recycling furnace. | Courtesy of Constellium
A secondary aluminum company has begun licensing a technology to reduce impurities in molten recycled aluminum, according to the REMADE Institute.
The REMADE Institute, a research organization funded partly by the U.S. Department of Energy, announced that a REMADE-funded R&D contractor, Phinix LLC, has begun licensing its scrap aluminum purifying technology to an unnamed recycling company.
In an interview with Resource Recycling, Subodh Das, CEO of Clayton, Mo.-based Phinix, said his company’s technology retrofits existing aluminum recycling furnaces and allows them to reduce the level of impurities so the scrap can be used in the desired end applications. The technology works on UBCs and other forms of aluminum scrap.
Phinix provided a general license, which means it can still offer the technology to other aluminum recyclers, he said. He’s under a non-disclosure agreement and can’t identify the licensee.
“The idea is to diffuse the technology to as many secondary aluminum scrap processors as possible,” he said.
Pure aluminum is used in a very limited number of demanding applications. Das explained that most aluminum in commercial use contains six elements in varying proportions: copper, iron, magnesium, manganese, silicon and zinc. Other than aluminum, the main elements in UBCs are iron, magnesium and silicon. Iron and silicon are present in bauxite, the virgin source of aluminum, and higher levels of magnesium are added to produce the rigidity needed in the can lids and tabs.
But the amount of each in scrap may not match what’s needed in the recycled-content product, so aluminum recycling companies will typically dilute the alloys by adding virgin aluminum, which is expensive and carbon intensive, Das noted.
Phinix’s technology, for which the company has applied for a patent, reduces the level of the alloying metals in molten metals to produce a recycled aluminum that meets virgin specs for use in beverage cans, vehicles or other uses. Das’ company is working to scale up testing on all types of furnaces.
“For us to be useful, we want to try that in all commercially available melting practices,” he said.
The technology stems from a research project funded by REMADE starting in 2020. The project, titled “Selective Recovery of Elements from Molten Aluminum Alloys,” involved Phinix LLC, Worcester Polytechnic Institute, Kingston Process Metallurgy, Smelter Service Corporation and Certified Flux Solutions LLC. According to REMADE, the research project is still in progress, led by Das and overseen by REMADE’s tech team.