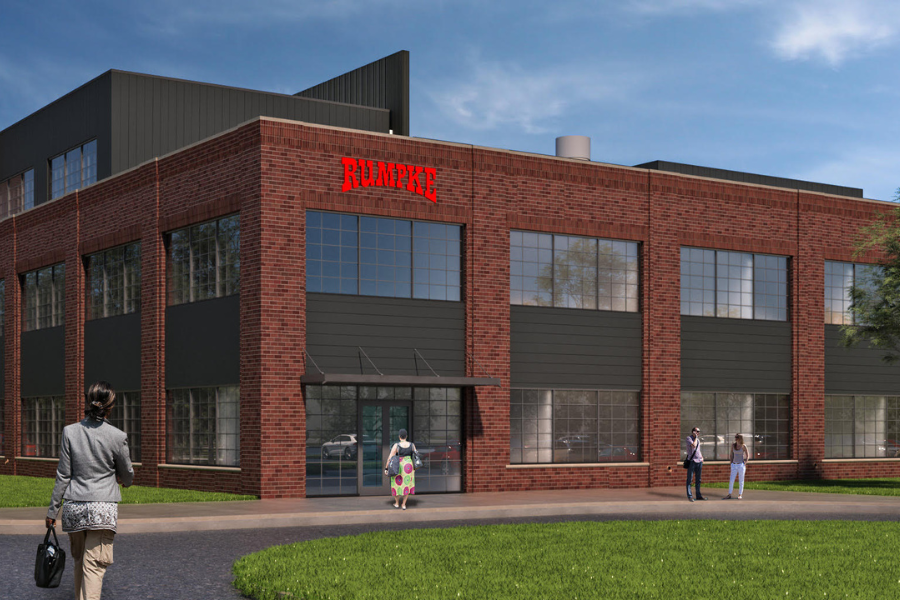
A rendering shows the entrance of the planned Columbus MRF. | Courtesy of Rumpke Waste & Recycling
A sprawling MRF under construction in Central Ohio will provide Rumpke Waste and Recycling with plenty of room to spread out – spread out recyclables on the belt, that is. That strategy can help automated sorting technologies work more effectively.
“Burden depth is huge if you’re trying to get your recovery rate up,” Jeffrey Snyder, Rumpke’s director of recycling, told Resource Recycling.
His goal is for the 223,000-square-foot, tech-heavy Columbus MRF to achieve a 98% or higher capture rate.
“For me, it’s about capturing the things that I say put in the bin,” Snyder said. “If you make a decision at your house to put a recyclable in the recycling bin, then I feel like it’s Rumpke’s responsibility to make sure it gets into a recycled state.”
It’s been one year since Rumpke Waste and Recycling first announced its project to build a massive MRF in Columbus. Around the anniversary, Snyder talked with Resource Recycling about what has changed with their project, which broke ground in February 2023, and what remains the same. He also further explained the strategy behind the use of technology in the plant.
Originally conceived as a 200,000-square-foot MRF, Rumpke is now planning a 223,000-square-foot facility. Snyder said the company added office space for training, career development, university student research and public education.
The estimated project cost has also shot up about 80%, from around $50 million to $90 million. Snyder said the increase is a combination of several factors, including the addition of building square footage, the decision to add more sorting technology than originally planned, longer lead times and cost inflation.
As a result of the decision to add sorting equipment, when it opens in June 2024, the MRF will have a sorting capacity of about 60-65 tons per hour. A year ago, the planned capacity was 50 tons per hour.
Spreading out the container for the opticals
Working with its equipment supplier, Machinex, Rumpke decided to add more ballistic separators, trommels, artificial intelligence capabilities and other equipment than originally planned, Snyder said.
He noted that current plans call for the use of ballistic separators and optical sorters to perform 2D/3D sorting for which traditional MRFs, including those owned by Rumpke, often use rotating disc screens. Ballistic separators and opticals aren’t plagued by the tangling, maintenance and wear issues experienced by older star screens, he said.
“To use different technology to separate paper from containers was really important to me,” he said.
All told, the MRF will sport 19 optical sorters, a huge number under one roof, with some units performing three-way sorts (with eject-down, pass-through and eject-up fractions). On the container lines, instead of having humans provide QC on outbound commodities, optical sorters will catch the commodities missorted by earlier sorters and return them to the front of the container lines.
Jeffrey Snyder, Rumpke’s director of recycling | Courtesy of Rumpke Waste & Recycling
Although the facility won’t initially use any robotic arms to sort recyclables, it will lean hard on AI cameras to identify and catalog materials. Of the 19 optical sorters, 11 will have AI cameras in front of them informing their sorting decisions, Snyder said. The AI identifies items by evaluating their shape, size, color and other visual characteristics, allowing the optical sorter to differentiate between a PET thermoform and PET bottle, for example.
All sorting technologies perform best when burden depths are low, Snyder noted. High burden depths – or having recyclables piled on top of each other – is the reason older MRFs aren’t recovering as much as newer plants today, Snyder said.
To help spread material out for effective sorting, the Columbus MRF will divide the container stream onto two container sorting lines running in parallel, he said. As a result of space between materials on the belt, Snyder doesn’t immediately see a role for robotic sorting.
“I’m not putting robotics in this MRF to start, and the reason is I feel like I have so much technology and so much less burden depth on the lines to allow the NIR separators to do what they’re supposed to do,” he said. “I don’t know where I’d put a robotic arm where I’d gain benefit in the sorting process.”
Although Rumpke still plans to hire eight to 10 people to work on presort, the front end of the line will be designed differently from most presort lines today, Snyder said. Instead of dumping material directly on the belt for pre-sorting, the material will first enter a trommel, which will separate items into three different size fractions. Outputs of the trommel will then go to presort. As a result, the material will be more spaced out and easier for staff to see as they go about removing unwanted and potentially dangerous items, such as batteries.
Marketing benefits
Snyder said the Columbus MRF will be able to produce commodities for a variety of markets, including those that don’t even exist yet.
In terms of plastics, the MRF will be able to provide grades that many other MRFs can’t, he explained. For example, it will produce clear PET, color PET and PET thermoform bales. The plant will be able to ship natural PET bales to reclaimers that want only clear plastic for sale back into beverage bottle markets but currently have to sort out colored plastic.
The plant will also have excess space in anticipation of the opening of new markets in the future.
“I’m not just building the facility to have bunkers for what I’m sorting today; I’m building the facility to have two extra bunkers on the container line,” he said, adding that it would allow the addition of aluminum foil, PS, mixed metal-paper containers (think Pringles tubes), as examples.
The facility is also adapted to a changing materials stream, with more online purchases leading to greater volumes of small corrugated boxes in curbside bins. Rumpke has added optical sorters aimed at removing those containers from the mixed-paper stream.
A former fiber buyer for Pratt Industries, which recycles OCC and mixed fiber into 100% recycled corrugated boxes, Snyder said leaving the OCC in mixed-paper bales won’t bring MRFs higher prices for those bales, but it will reduce the amount of valuable material headed to their OCC bales, which fetch higher prices than mixed paper.
“I’m trying to create value for the MRF,” he said.
While much has changed about the project, the timing hasn’t, Snyder said. Machinex is still targeting mid-October for equipment installation, and the target date for opening is June 1, 2024.
Snyder is excited about the potential that comes with designing a new plant from the ground up.
“We have an opportunity to do it the right way, from education to tours to sustainability jobs,” he said, “to have the most technologically … advanced facility in the country.”
More stories about MRFs
- Recycling facility fires expected to reach new high
- Haulers feel effects of lower recycled commodity prices
- WM report suggests 2025 goal is out of reach