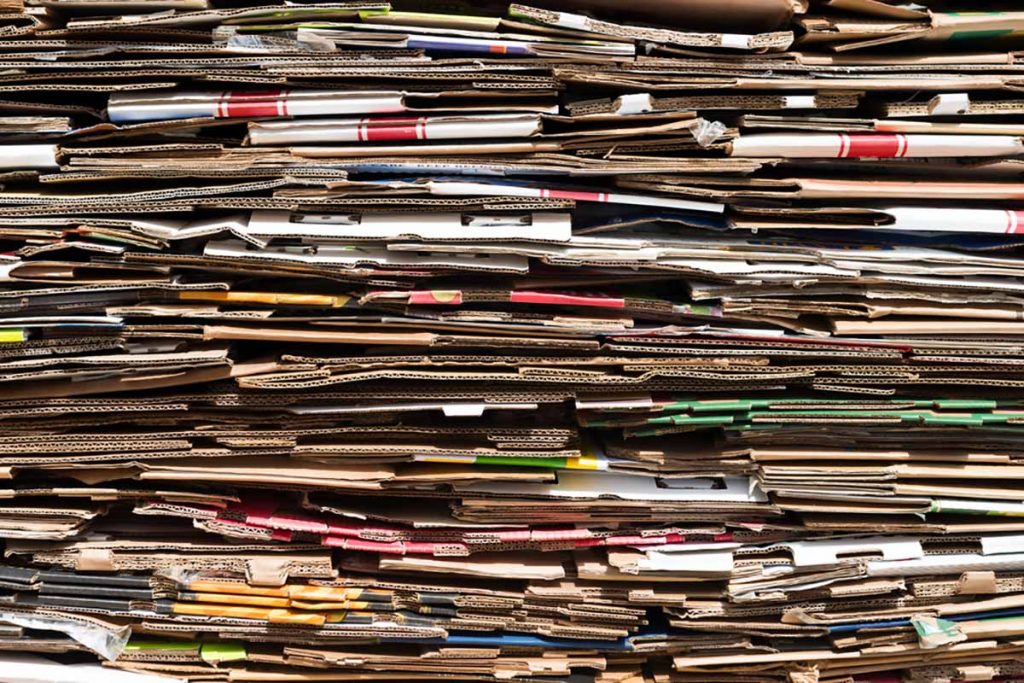
Even though OCC bales are currently selling for unusually low prices, many producers are seeing their savings offset by increased costs in other areas. | Kenishirotie/Shutterstock
Recycled paper product producers may be enjoying the lower OCC prices as 2022 comes to a close, but those giant manufacturers are still facing higher inflationary pressures in other areas, several executives recently noted.
During a Nov. 1 call with investors, Robert Coker, CEO of packaging producer Sonoco, was asked whether low OCC prices would continue to give his company a cost-reduction benefit early next year. OCC is the biggest driver of cost in the industrial products division, he noted, but it’s not the only one.
“At this point in time, we have got a lot of inflation. We spent a lot of time talking about OCC, but all the chemical starch, diesel, labor – there is just a lot of inflation still out there,” Coker said.
The following are some other market and capital investment takeaways in recent financial reports and earnings calls from large publicly traded manufacturers of corrugated boxes and other paper-based packaging.
OCC prices down but other costs are higher
In its third-quarter financials presentation, Quebec-headquartered packaging and tissue producer Cascades quoted OCC at about $33 U.S. per short ton in November, down from about $109 in the third quarter and $137 per ton in the second quarter of 2022.
The presentation noted that mills have solid OCC inventories and have been reducing their production levels to meet demand. Those factors, combined with lower export demand, have driven down prices for OCC. Cascades anticipates the “favorable market dynamics to persist” through at least the end of this year.
Cascades’ presentation also noted that sorted residential papers are cheaper than they were in prior quarters and a year ago, but higher-grade fibers, including sorted office paper, remain elevated. The average index price for white recycled papers in the third quarter was up 60% year over year.
And virgin pulp prices remain high, with U.S.- and Canada-sourced pulp selling for about $1,620 per short ton during the third quarter, up 23% year over year and 7% from the second quarter.
“As we have highlighted in the past, these unrelenting cost headwinds have had an important impact on our tissue results,” Mario Plourde, president and CEO of Cascades, said during a Nov. 10 conference call with investors. “The same can be said about virgin pulp.”
In the packaging business, he expects that, in the near-term, the lower feedstock costs will counterbalance lower sales volumes.
Other major companies also discussed the market dynamics, which are favorable in some ways but not in others.
Steve Scherger, chief financial officer of Atlanta-based Graphic Packaging International (GPI), told analysts in an Oct. 25 conference call that OCC in the fourth quarter may be cheaper on a year-over-year basis, but the benefit is being more than offset by GPI’s higher costs for other inputs, such as paperboard chemicals and energy.
International Paper (IP), one of the world’s largest paper and pulp companies, has seen some of the same dynamics play out.
In its quarterly financial report, the company said its corrugated box sales in North America were lower in the third quarter, driven by overall decreases in consumer spending and reductions in retailer inventories. Like other companies, IP has raised prices for its boxes and containerboard products, however, propping up sales margins in a higher-cost environment.
In its quarterly presentation, IP also noted the lower OCC prices have helped, but the benefit has been overshadowed by higher energy, distribution and other costs. In terms of costs of manufacturing inputs in the third quarter compared with the second quarter, OCC prices were down 10%, but virgin wood was up 1%, natural gas was up 17%, electricity was up 21% and chemical composite was up 6%. Recycling of OCC relies on a lot of natural gas.
In a recent interview with Resource Recycling, John Grinnell, vice president and general manager of packaging products manufacturer Greif, noted the volatility of markets.
“These are challenging times for everybody and ours is a market that bounces back and forth between too little supply and too much demand, then the opposite, which is where we are now,” he said.
The Delaware, Ohio-based company recently opened two additional recycling facilities to help feed its mills. The move was done with an eye toward the long-term, however, not any short-term market dynamic.
“As an integrated system from recycling material at paper mills to converting we look at this with a long term perspective and with the knowledge that even if maybe the incremental supply isn’t immediately needed, in the long term it will be important to us,” he said. “We worry less about the month to month and more about the year to year.”
Focus on facilities footprint changes
Companies provided updates on several capital investments that are expected to boost domestic fiber recycling markets.
Greif’s Paper Packaging and Services (PPS) business recently announced two investments in its recycling operations: a new 81,000-square-foot facility for collecting, processing and baling paper in Florence, Ky., and the doubling in size of a paper recycling plant in Nashville, Tenn. to enhance efficiency and support accelerated growth.
“The paper fiber recycling plants are located in close proximity to Greif operated paperboard mills as well as other containerboard and recycled paper product manufacturers, and where greater growth opportunities are possible,” Grinnell stated in a press release.
In an interview, he said that “both Nashville and Kentucky are pretty rapidly growing metropolitan areas with a lot of opportunities for fiber, so we felt like those were good investments for us to make to be able to grow our secure supply of material.”
About half of the fiber Greif collects through its recycling business is sent to the company’s containerboard mills, and the rest is sold to other producers of paper products, according to a press release. In the interview, Grinnell said Greif’s paper and packaging business “is almost wholly a recycled-content business.”
Meanwhile, Cascades is still working to convert a mill in Bear Island, Va., from producing newsprint to making containerboard for corrugated boxes. After the conversion, the mill will take in OCC and mixed paper and produce up to 330,000 short tons of containerboard for conversion into corrugated boxes.
The estimated date of completion and total cost have changed. In late 2021, Cascades was estimating that the project would open in December 2022 at a total cost about $125 million. But in a recent press release, Plourde said that commissioning of certain key equipment has been delayed by supply chain constraints, and the revamped plant is now expected to open in the first quarter of 2023.
Additionally, according to the company’s latest financial presentation, Cascades has spent about $318 million on the project, which is now estimated to cost between $470 million and $485 million total, with inflation to blame for the higher cost.
GPI, meanwhile, noted in a press release that its new Kalamazoo, Mich. coated recycled board machine is ramping up, allowing the company to meet increased demand for recycled paperboard packaging. The company consumes about 1.4 million tons of recycled fiber per year.
GPI’s $600 million line in Kalamazoo will be able to recycle about 500,000 tons of recovered fiber into coated recycled board (CRB) per year. The project is capacity neutral, replacing four older lines the company is planning to shut down. But the new system is also more water and energy efficient than the older lines it’s replacing.
The CRB machine was commissioned in February and produced its first CRB for sale that month. In the third quarter, during many days, it operated at its target of 1,500 tons per day, according to a GPI presentation.
During the third quarter, Sonoco marked a milestone in its Project Horizon. The company converted its No. 10 paper machine in Hartsville, S.C. to produce uncoated recycled board (URB) during the quarter. The machine has a targeted annual production capacity of 180,000 tons.
The project also involves shutting down two older, less efficient machines in Hartsville.
“Project Horizon is expected to drive significant annualized cost savings as production ramps through 2023 and beyond,” according to the company’s third-quarter financial report.
Paper producer Domtar is planning to enter the packaging business by converting a Kingsport, Tenn. paper mill to produce 600,000 tons of recycled linerboard and corrugated medium annually. In its quarterly report, filed earlier this month, the company said the project is on track to be completed by the end of 2022.
Atlanta-based paper and packaging producer WestRock, which consumes about 5 million tons of recycled fiber per year, announced on Nov. 9 that it reached a deal to sell its interest in RTS Packaging to its joint-venture partner, Sonoco, for $330 million. The transaction includes selling WestRock’s Chattanooga, Tenn. mill, which supplies URB to RTS.
Additionally, WestRock signed an agreement to sell its URB mills in Eaton, Ind. and Aurora, Ill. to Ox Industries for $50 million. A press release noted that URB is not a priority product for WestRock but it is for Ox Industries, a manufacturer of recycled paperboard products.
More stories about markets
- ‘Operational readiness is high’ as Oregon rolls out EPR
- Pizza box demand declining, report says
- Paper operations close in Georgia, Texas