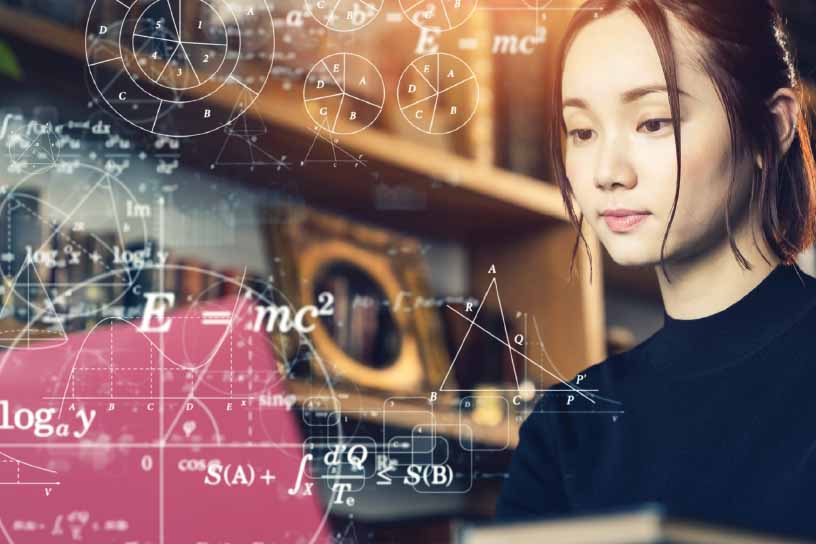
A state recycling association leader recaps an effort by students at the Colorado School of Mines to develop technological solutions to recycling aluminum cans with plastic labels.
When students from the Colorado School of Mines offer fresh perspectives on solving complicated recycling challenges, we listen.
Last semester, Recycle Colorado, the statewide nonprofit for the recycling industry, had the pleasure of working with 10 students on the problem of separating plastic labels from aluminum cans. It is often difficult to tell if your favorite canned beverage has a plastic label. These plastic coverings (while great for branding) cause sorting difficulties at our recycling centers and damage equipment at the aluminum mills.
Sophomores and juniors at the Colorado School of Mines applied their studies in engineering physics and metallurgical and material engineering to address this real-world beverage can recycling challenge. I coached these students on the overall problem and shared a variety of perspectives from Recycle Colorado stakeholders who participated in previous roundtable discussions.
The students addressed the issue from an engineering perspective but connected to it on a personal level. They raised awareness among their peers and family to remove plastic labels before recycling the cans – a whole other kind of education.
Technology for UBC sorting and label removal
The students were organized into two teams, and the results from both sides are compelling.
One team, calling themselves “Vincent Can Go,” combined the technologies of an optical eye, which detects PET, with an electromagnetic and dual-energy X-ray transmission sensor (DE-XRT) to detect aluminum.
The DE-XRT system might be better known for luggage inspections at airports, but the technology can also detect metallic elements such as aluminum. The DE-XRT unit is just slightly larger than a Monopoly box, making it feasible to add to a sortation line. The combination of the PET optical eye with the DE-XRT sensor enables a system to determine if a material is a combination of plastic on top of aluminum, thus allowing this layered material to be separated. The team’s simulation model showed that 2 volts was optimal for the speed necessary to properly sort the material, resulting in 90-95% accuracy.
Where one team’s part of the solution leaves off, the other team picks up. The “Restore 41” team engineered a multi-step solution to remove plastic from aluminum cans. This team’s design starts with wire brushing the cans. This process is designed to pierce the outer plastic covering, making it more vulnerable for removal.
Next, the cans are put into a large drum containing an acetone bath, which weakens the plastic. While in the drum, an agitator blade rotates the cans, ensuring even exposure to the acetone.
The third and final step is high-intensity water spraying. With the plastic already loose, the spraying process further removes the plastic covering. This team’s testing prototype showed an 80% success rate with the plastic getting partially removed. The hypothesis is that all the plastic could be removed with the appropriate industrial equipment.
This team noted the following: “Firstly, the removal procedure should take place after cans are crushed because the sharp corners facilitate far greater destruction of the labels. Second, the brush-spray combination is extremely effective on shrink-wrapped cans, and less so on adhesive-based (labeled) cans.”
The desired end result is a plastic-free can that can be sent to the aluminum mill and ultimately made into new aluminum cans, thus perpetuating the circularity of aluminum.
Project’s practical limitations
While these two teams’ ingenuity shows the way to future industry innovation, it’s also true adding these components to existing recycling facility operations would be extremely difficult. Retrofitting sort lines with limited footprints is challenging and costly.
Additionally, introducing a chemical process such as an acetone bath would require special permitting for hazardous chemical materials, as well as upgraded ventilation, new training, safety precautions and more. A chemical bath, in fact, may need to be housed in a separate facility altogether. Nonetheless, we have two unique engineering solutions thanks to the efforts of these teams.
In the time of COVID-19, the research and expanse of testing achieved by the students was commendable. Sadly, they were unable to visit a materials recovery facility to better familiarize themselves with existing operations and parameter constraints. Undeterred, these students created their own home-built “sortation” lines with a limited budget. For example, to simulate the agitation process of the acetone drum bath, they created a clear plastic drum affixed to a bicycle pedal. Additionally, their 3D modeling and creation of a combo optical eye with DE-XRT system was quite impressive.
And of course, there is much to be gained from fresh thinking on industry issues, even if the concepts cannot be immediately implemented.
All innovations need time to take shape and become integrated into standardized operations. The creative problem-solving of these two academic teams lends itself to further exploration. We welcome their energy and ideas as Colorado embraces clean tech in its pursuit of waste diversion goals and circular economies.
The notion of enhancing UBC recycling has national implications as well. Aluminum can be recycled indefinitely, which makes it an extremely valuable material to recover from the waste stream for both the environment and the economy, yet we are currently experiencing a national aluminum shortage. It looks like we’re missing out on some serious opportunities when we can’t recover the aluminum in our own country due to wrappings or coatings on the can.
Our industry’s collaborations with industry leaders such as Ball Corp., MolsonCoors and Swire Coca-Cola – companies that support innovative exploration from institutions like the Colorado School of Mines – are exciting and invaluable.
Laura Levesque is the programs director at Recycle Colorado, a statewide nonprofit organization that works on projects related to infrastructure and end markets for material recovery, reuse and manufacturing. She can be contacted at
laura.lc@recyclecolorado.org.
This article appeared in the March 2021 issue of Resource Recycling. Subscribe today for access to all print content.