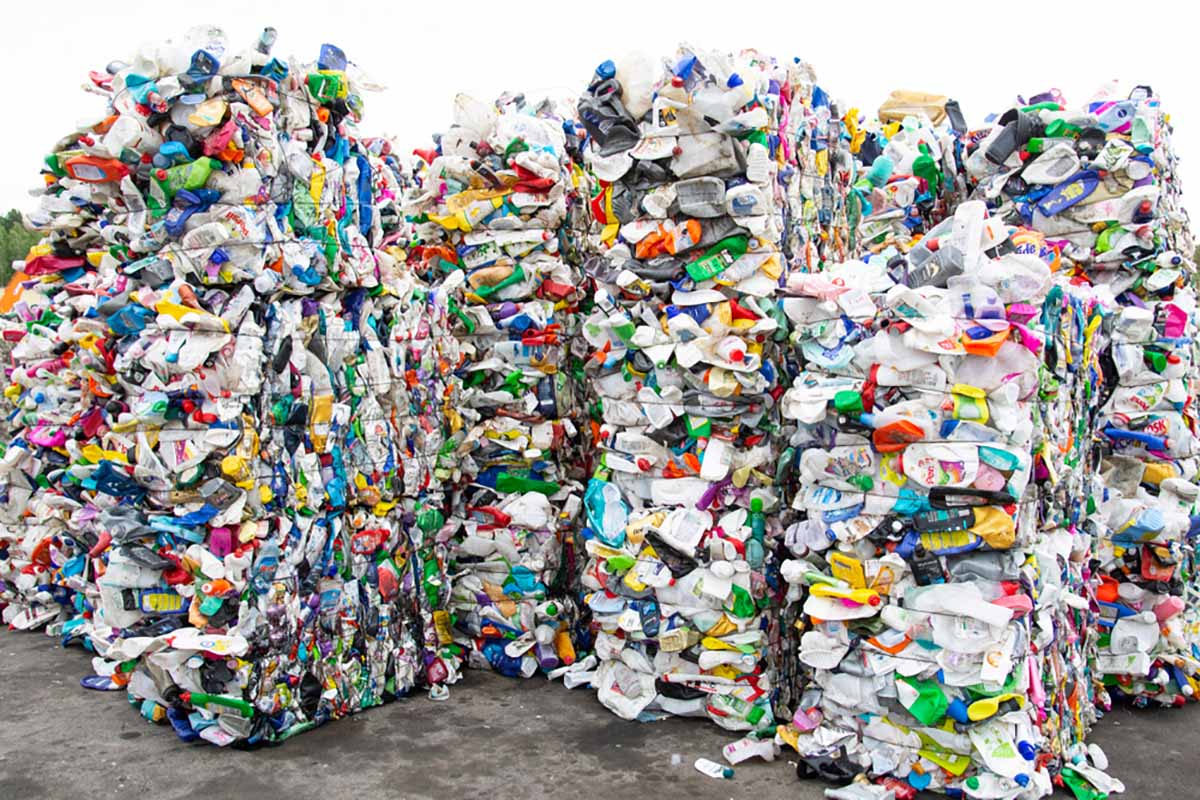
Waste Management issued its September 2020 “Report on Recycling” to identify gaps in U.S. plastics recycling infrastructure, among other goals. | Natallia Boroda/Shutterstock
A recent report from the nation’s largest waste and recycling hauler outlines MRF infrastructure and reviews the current state of reclamation capacity for key recovered plastics.
Houston-based Waste Management (WM) issued its September 2020 “Report on Recycling” to identify gaps in U.S. plastics recycling infrastructure, among other goals. The report, which is based on research and data-gathering from consulting firm Resource Recycling Systems (RRS), was brought about after advocacy group As You Sow called on Waste Management to disclose more information about its plastic management.
After As You Sow last year filed a shareholder proposal looking to compel the publicly traded waste giant to share information, Waste Management and the advocacy group undertook what both describe as “in-depth engagement.”
As You Sow issued a release this month expressing hope that the report “will serve as a valuable first step in a broader conversation with regulators, packaging producers and consumer brands about policies and practices required to rapidly increase the amount of plastic recycled in the U.S., especially those for which there are existing markets.”
Snapshot of company MRFs and upgrades
WM reported that it operates 49 MRFs, a figure that includes four facilities that opened or will be opening this year.
The report breaks down these MRFs into categories based on recent and planned investments. Beyond the four brand new facilities, 20 of them received optical sorter or screen upgrades within the past two years. An additional 12 are planning investments in the next three years, and 13 have no upcoming plans for upgrades.
The company plans to consolidate recycling tonnages at its upgraded MRFs, according to the report.
“Barring any long-term changes in market conditions and recycling volumes, including impacts of COVID-19, WM anticipates processing 91% of our single-stream tons at the 73% of our MRFs where [we] will have improved processing capabilities as a result of investments in construction and upgrades by 2023,” the report states.
Recent upgrades include an “extensive facility upgrade” that cost $6.5 million in 2019. This project brought in non-wrapping screens, new optical sorting and robotics technology, new conveyors and more. This project improved outbound paper quality by reducing OCC in the mixed-paper stream from 25% to less than 3%, and it also cleaned up the aluminum and PET streams, bringing the company higher commodity prices. Overall, that unidentified project yielded an $11 increase in the value of the blended ton.
Other upgrades include “relatively small” projects costing between $1 million and $3 million. Despite their lower price tag, these projects “can have an impact on the volume and quality of material recovered,” the report states.
One such project was an isolated optical sorting system upgrade at an older Waste Management MRF. This increased the PET capture rate from 94% to 98%, the company reported.
Important regions lack PET processing
Of the big three resins, the analysis found that the PET reclamation sector has the most consistency. PET reclaimers “tend to be well established in the marketplace,” the report stated.
But the areas where PET generation is the highest do not always align with the existing PET processing footprint.
For instance, the Southeast and Southwest account for 55% of the country’s PET processing capacity, meaning material generated and collected in those regions have a nearby home. But few PET reclaimers exist in the heavily populated Northeast, the Mid-Atlantic and the Midwest, according to the report.
Overall, the U.S. generates about 7.3 billion pounds of PET containers and packaging per year, of which about 1.9 billion pounds are recovered for reclamation. The U.S. has the capacity to reclaim nearly 2.6 billion pounds.
There are some 27 PET reclaimers operating in the U.S., according to the report.
The largest end markets for recycled PET are fiber (47%), food and beverage bottles (21%), and sheet and film (19%), with smaller percentages going into strapping, non-food bottles and other products such as engineered resin.
HDPE reclaimers can take in more
Moving to the HDPE recycling sector, the Waste Management analysis found that though there are numerous reclaimers, they tend to come and go as supply and demand fluctuates.
The report found there are about 7.5 billion pounds of HDPE containers and packaging generated in the U.S. per year. Reclaimers process about 1.3 billion pounds of the resin per year, and have the capacity to handle about 1.8 billion pounds per year.
HDPE reclamation is also divergent by region, with some of the major generating regions having relatively low capacity. For example, the Southwest generates 16% of the country’s HDPE but only has 5% of the reclamation capacity for the resin.
Overall, there are 28 reclaimers processing HDPE in the U.S., the report stated.
Major end uses for HDPE include non-food bottles (37%), pipe (33%), lumber and decking (8%), with smaller amounts going into lawn and garden use, automotive, film and sheet, crates and buckets, pallets and more.
PP becoming increasingly attractive to sort
Finally, PP reclamation is still a relatively small sector, although it has increased in recent years alongside PP generation in the material stream.
“More reclaimers are processing PP, and the commodity value of this resin has made it attractive for MRFs to sort out of their inbound feedstock,” the report found.
Reclamation and capacity are strongest in the Southeast U.S., the report found, where there is a larger concentration of manufacturers that use PCR. The region “relies heavily on PCR for their manufacturing industry, contributing to their overall economy,” the report stated.
Overall, the U.S. generates about 3.7 billion pounds of PP containers and packaging per year, of which 420 million pounds are recovered for reclamation. Reclaimers have the capacity to handle about 504 million pounds of the material, according to the report.
There are 10 PP reclaimers that handle as much as 60% of the PP recycled in the U.S., according to the report.
A version of this story appeared in Plastics Recycling Update on September 10.