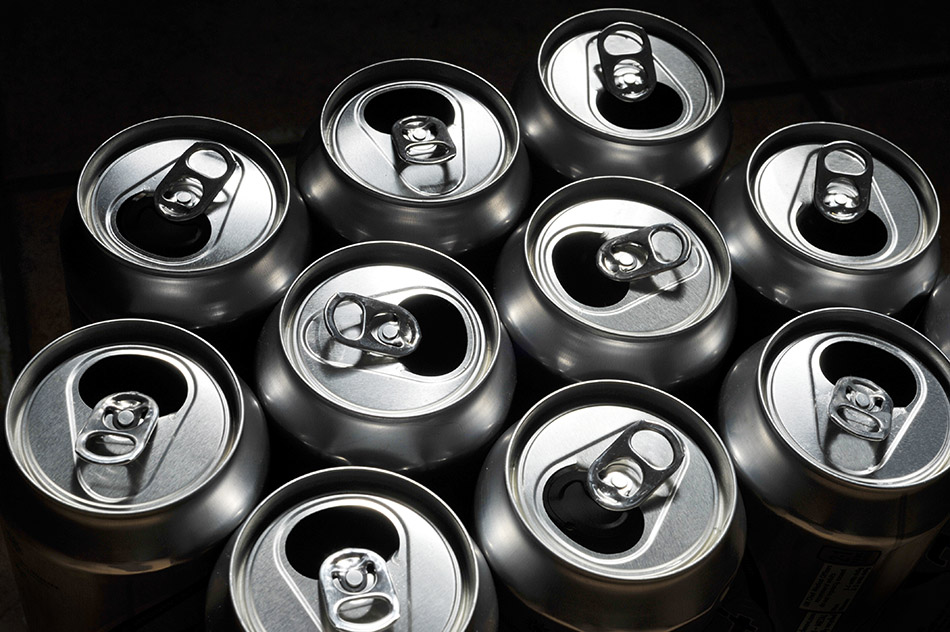
Recent research determined that in 2019, UBCs made up 12.5% of potential revenues in MRFs in bottle bill states and 33% of potential revenues in MRFs in non-bottle-bill states. | Graham Corney/Shutterstock
Robotics and additional eddy current separators are key to maximizing sortation of used beverage cans, according to MRF operators, researchers and other experts.
UBCs are a high-value, highly recycled commodity, but even with their roughly 50% recovery rate, there is substantial room for improvement. And in a recent virtual event, experts elaborated on increasing successful sorting of these aluminum materials within recycling plants.
The event, hosted by the Can Manufacturers Institute, was framed around a recent report the organization commissioned looking at various aspects of UBC recovery. Completed by Gershman, Brickner & Bratton (GBB), a solid waste management consulting firm, the study examined UBC composition in MRFs. The research found that UBCs made up 0.4% of a MRF’s inbound stream in states with container redemption laws and 2.2% of the stream in states without them, said Corinne Rico, project manager at GBB.
That may seem small, she added, but aluminum, by weight, is the most valuable recycling commodity on the market. In 2019, UBCs made up 12.5% of potential revenues in MRFs in bottle bill states and 33% of potential revenues in MRFs in non-bottle-bill states. That’s more potential revenue than any other single commodity, she pointed out.
But UBCs can get lost in the MRF in a number of ways, Rico explained, stating that although the information about these losses is limited, current research suggests an average MRF could be losing up to 25% of UBCs during the sorting process.
The importance of maximizing aluminum recovery has been highlighted during the coronavirus pandemic, as was evident at Eureka Recycling, a nonprofit MRF operator in Minneapolis.
Aluminum prior to COVID-19 was about 1.5% of the stream by weight for Eureka’s MRF, said Kate Davenport, co-president of Eureka. Now, it’s risen above 2%, she said on the webinar.
Technology drives recovery
A substantial quantity of UBCs never make it to the MRF in the first place. About 13 million metric tons of metal went to disposal in 2018, according to information presented by Jon Powell, vice president of materials recovery investment firm Closed Loop Partners. Of that, about 1.2 million metric tons was made up of UBCs.
That number, combined with the value of UBCs, is enough to raise eyebrows in the investment community.
“When we look at 1.2 million tons of material that’s missed, at current commodity values, that’s a billion-dollar opportunity that’s being missed,” Powell said, noting his organization has made investments in both collection and sorting of UBCs.
Equipment upgrades, specifically eddy current separators and robotics, are key to reducing UBC loss within the MRF, said Rico of GBB. Most MRFs have eddy current separators, but fewer have robotic systems that use artificial intelligence and visual identification technology to target materials. Used in tandem, the efficacy of these “can’t be understated,” Rico said.
GBB looked at adding an eddy current separator on a MRF residue line and a robot on the fiber line, and it found that the increased revenue that would be gained by capturing UBCs in these areas could cover the cost of the equipment purchases in about two years, Rico said. With just the additional eddy current unit on the residue line, the MRF could pay for the equipment in roughly one year.
Jeffrey Lacey, a senior staff scientist with the Idaho National Laboratory, elaborated on the factors hampering greater UBC recovery. The laboratory has a large material processing facility where it recently began researching municipal solid waste.
Once a can reaches the MRF, it can get physically distorted in multiple ways that will redirect it to the disposal stream. When a can gets flattened, sorting equipment will send it along with residue line or fibers.
Machine-learning sorters, or artificial intelligence, are one tool to help capture these UBCs. These systems are advancing visual imaging technologies to “where it becomes interesting and powerful,” Lacey said.
“We can train them not just to recognize materials but also to make complex decisions,” he said. For example, on a MRF sorting line, the operator can tell the machine to prioritize certain materials to target.
Additionally, the machine-learning advances are allowing imaging systems to identify features of objects they can recognize. The system may be trained to visually differentiate between steel and aluminum cans, for example, or even between different alloys of aluminum.
“The technology is available, it is working well and it’s a great opportunity,” Lacey said.
Robotics in action
Facility improvements in Florida and Minnesota demonstrate the value – and the logistical considerations – of adding robotics and eddy current separation equipment.
Single Stream Recyclers in Sarasota, Fla. runs optical sorters on its fiber lines to recover the flattened cans in the paper stream.
John Hansen, co-owner of the facility, said the MRF has a decent capture rate with this system. But if the optical sorter is adjusted to more aggressively target aluminum cans, it tends to remove paper from the stream as well, something the facility wants to avoid.
The facility is currently working to add eddy current separation equipment to complement the optical sortation on that fiber line, Hansen said. The goal is to increase the capture rate for aluminum cans as high as possible.
That latest effort comes after the facility added 14 robotic arms over the past year. Those were added to increase product quality and reduce labor costs, Hansen said.
“We also understood that when we did do this, that at the end of the day we were going to capture more UBCs and high-value items,” he said.
The robots are spread out through the plant, largely performing quality control sorts on the fiber and container lines. Out of the 14 robotic arms, 13 are targeting UBCs, Hansen said.
The final robot is the quality control arm for the UBC line. Aluminum cans are recovered at the end of the container line after all plastics have been ejected. UBCs go through an eddy current separator, and then the quality control robot targets any non-UBC materials that remain on the line.
“As everybody understands, these high-value UBCs have to be super clean,” Hansen said. “So we use the robot to pick any residue, any paper that might have gone up there, as well as off-spec aluminum – your aerosol cans, things of that nature.”
The UBC quality control robot is performing between 70 and 80 picks per minute, Hansen said.
Although the robots have been very effective, Hansen said using these systems comes with challenges. Starting up the robot is a logistically intense process, requiring various infrastructure improvements to the line. Single Stream Recyclers installed about three robots per weekend, Hansen said, looking to minimize downtime. Starting on Friday, MRF employees would work alongside AMP Robotics employees to get the robots installed, so that by Monday morning, the facility would ideally be back up and running with the robots in full working order.
Some key challenges and considerations were related to space requirements – whether there was headroom height for the robot, whether the setup allows the robot to drop picked material directly into a gravity bin that moves it into a baler or whether it needs to be moved via a conveyor belt, and more.
Adding eddy current systems
In 2016, Eureka Recycling was looking to upgrade its facility as it was anticipating a substantial growth in inbound volume. While looking at upgrades, Eureka wanted to increase efficiencies and improve material quality, said Davenport.
The facility installed what Davenport described as a “scalping screen,” a screen set at five to six inches, and Eureka added another ballistic separator. These improvements are geared toward capturing flattened aluminum cans as well as small paper, Davenport said.
Additionally, the facility decided to install two additional eddy current separators. These were chosen in part because the existing eddy current system was not sufficient to handle the projected 10-tons-per-hour increase in throughput.
Material goes through the screen and ballistic separator, then through the fiber and container sorting lines. Containers then run through a magnet, the first new eddy current separator, a manual sorting station, and then the second new eddy current separator.
“That system has worked effectively. We’re essentially pulling out aluminum at the beginning and the end of the container line,” Davenport said.
Before the improvements, Eureka estimated between 3% and 5% of its fiber stream was aluminum that ended up there as a contaminant. After the upgrades, the facility has seen that figure drop below 2%, Davenport said.
“It’s not perfect, but we cut that loss in half,” she said.
The facility is now looking at further improvements, including robotics to remove aluminum and PET bottles from the fiber line.
More stories about metals
- Tariffs on Canada and Mexico take hold
- Aluminum giant shares expansion plans
- How a national deposit could drive can recovery