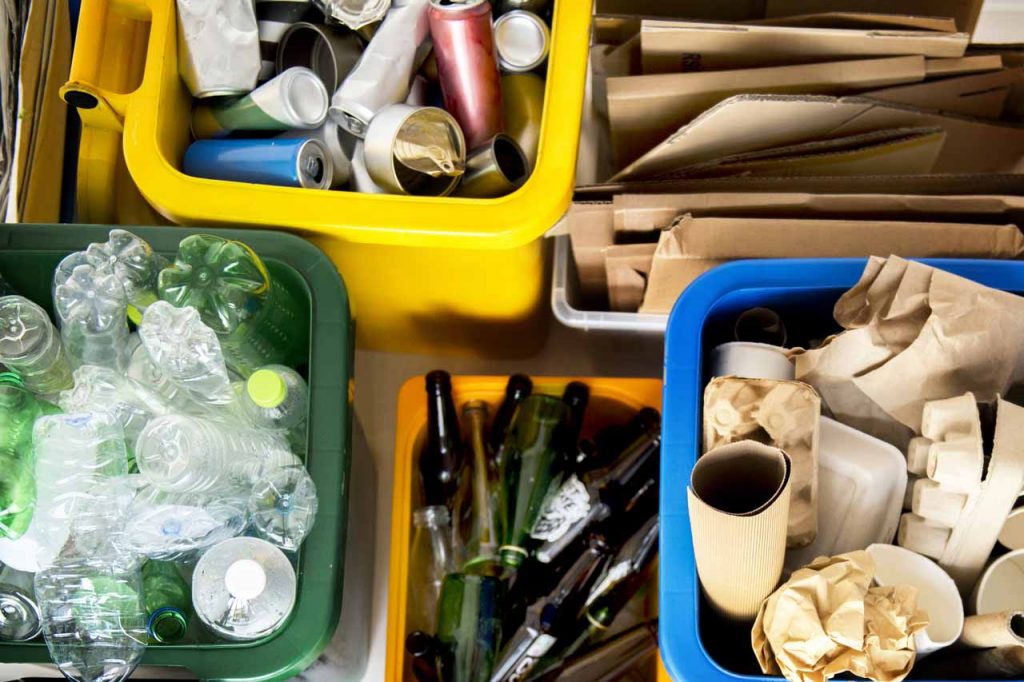
Residential recyclable materials have become an increasingly important feedstock for manufacturers since the coronavirus outbreak. | RawPixel.com/Shutterstock
As the coronavirus impacts continue throughout the U.S., manufacturers are highlighting the importance of curbside recycling as a feedstock supply channel. Meanwhile, processors are seeing changes in demand for their material as consumer spending shifts.
End users and recycled material processors spoke on an April 16 presentation hosted by the Southeast Recycling Development Council (SERDC). The presentation featured Waste Management, Pratt Recycling, Greif, KW Plastics, the Can Manufacturers Institute and the Glass Packaging Institute.
Waste Management, the nation’s largest hauler of recyclables, received an early indication that recycling would be vital during the pandemic, explained Susan Robinson, senior director of sustainability and policy at the company.
“We were reminded of our essential role in the packaging chain when our mill customers started calling us, asking what we were going to do to ensure we could keep their pipeline full of the essential products they manufacture,” Robinson said.
It was an important moment of realization for company leaders that Waste Management had to do whatever it could to help keep the country’s manufacturing sector moving forward, Robinson added.
Speakers on the webinar spoke on how the movement of material to manufacturers is changing because of the pandemic, and they made clear this reality extends across the spectrum of recycled materials.
Curbside material more important than ever
For Waste Management, the coronavirus impact has shifted the stream of material coming through the company’s MRFs: The facilities are seeing less material on the commercial side because so many businesses are shut down. Even as some residential programs have been cut or suspended, in programs that are operating residential recyclables have increased accordingly as more people are staying home.
That shift has implications for end users – in particular, it places greater focus on ensuring residential recycling continues, explained Shawn State, president of Pratt Recycling.
Pratt Recycling operates 18 sorting facilities and supplies recovered paper for five Pratt Industries paper mills (Pratt’s products are made of 100% recycled feedstock). Those facilities, State said, consume more than 2 million tons of recovered fiber per year. Pratt collects material from a variety of sources, including curbside programs as well as large commercial generators.
The residential sector has become increasingly critical for the company as the pandemic impacts have taken hold in recent weeks.
“Many businesses deemed non-essential are not open and not producing recycled fiber that is needed to run the mills,” State said. “So curbside recycling is important now more than ever.”
Pratt is the largest consumer of mixed paper in the U.S., and curbside recycling programs are where a majority of that mixed paper is generated, State noted.
A large and growing portion of OCC is also collected through residential programs, a shift that has occurred in recent years with the rise of e-commerce. The commercial sector shutdown has further increased that portion, State said.
Representatives of fiber manufacturers also noted it’s important to keep in mind that the coronavirus pandemic has come on the heels of reduced export demand due to China’s restriction on imports of certain recyclables.
The Chinese government decision shifted significantly global demand for OCC, leading to a glut of supply and a nosedive in pricing, said Greg Wall, general manager for the Southeast region of Greif, a major consumer of recovered fiber at its 15 U.S. paper mills.
The coronavirus has added “almost unimaginable” further challenges, Wall said, by constricting the supply of OCC required to produce packaging.
“The pandemic has shown how complex and interwoven our supply chain is,” Wall said. “A single broken link in the fiber portion of the manufacturing and distribution supply chain can become a bottleneck that limits the entire supply chain from functioning.”
Paper mills could be idled if they don’t have enough fiber to maintain operations, Wall said, adding that Greif is leveraging its logistics and relationships to minimize that potential.
State of Pratt added that over 75% of all paper mills in the U.S. use recovered paper in their operations.
Concerns about hamstrung deposit systems
Speakers also discussed the fact that most states with container deposit systems have suspended enforcement of the requirement that retailers redeem bottles. That phenomenon has impacted the container manufacturing industries by disrupting a key feedstock source.
Scott Breen, vice president of sustainability for the Can Manufacturers Institute, said roughly 40% of the recycled aluminum cans that container producers use comes from states with container deposit systems.
“Sadly, with coronavirus, we’re seeing less used beverage cans flowing through that existing circular system,” Breen said. He cited figures of a potential 50% to 80% decline in UBC flows in Michigan and California.
“That’s a big deal,” Breen said. “In California, they recycle 20 million cans a day, so if there’s that kind of disruption, that’s a lot of cans not coming back to us.”
Currently, the U.S. aluminum beverage manufacturing sector uses an average of about 73% recycled content in new cans. UBCs account for 43% of new cans, and the remainder is other sources of recycled metal and virgin metals.
“Given our high levels of recycled content, this drop in UBC flows means we won’t be able to make cansheet with the same kind of inputs as we have been,” Breen said.
Deposit material is also very prevalent in the glass bottle manufacturing sector. Scott DeFife, president of the Glass Packaging Institute, noted that about 60% of the cullet used in glass bottles and jars comes from deposit states.
DeFife added that much of the glass that makes it through the curbside recycling process currently does not go back into bottles and jars. Only 13% of material recovered through the curbside stream is making its way back into those products, he said.
Plastic bottle manufacturers also often prefer material from states with deposit systems, with curbside material frequently going into other markets. On the plastics side, for instance, curbside material often moves into textile, automotive and pipe markets, Waste Management’s Robinson explained.
That movement is changing due to the coronavirus.
“Since no one is buying carpets or cars right now, these industries are closing down and MRFs are having actually a hard time selling and moving some of their bottles and cans,” Robinson said. “So this could be a great time when we sync up that curbside supply with the plastic and glass bottles and cans from the demand side.”
Pandemic rearranges demand
KW Plastics, a Troy, Ala. plastics processor that describes itself as the world’s largest plastics recycling company, has seen plastics demand change firsthand.
The company has 350 employees directly tied to plastics recycling and KW has not laid off any of those workers, said Stephanie Baker, director of market development for KW Plastics.
But the company has seen fast changes in the numerous end markets it supplies.
The automotive sector has essentially shut down, and “we have seen that business come to all but an abrupt stop,” Baker said. Automotive manufacturers have floated plans to restart their plants in early May, but for the time being, that end market is closed.
At the same time, however, KW has seen demand increase for its natural HDPE recycled pellets. This resin goes into personal care products, household cleaning agents, detergents, soaps and more.
“We can’t keep that stuff on the shelves,” Baker said. KW anticipates shipping 9.5 million pounds of natural HDPE this month, Baker said,
“That is a significant amount for us in that particular resin, but, overall, that is significantly lower than what we would ship throughout our whole product line,” Baker said.
Baker said there has been a large uptick in brand owners making sustainability commitments in the past nine to 16 months, and those pledges have translated to more demand for using recycled plastic in innovative ways within product packaging.
But the coronavirus has shelved that work as companies prioritize responding to the current market.
“All of that has come to a stop right now as we are seeing our suppliers really scale back to producing the items, the products, that are essential right now,” Baker said. “They don’t have any room to introduce new products or new packaging right now.”
More stories about markets
- Denali reports recycling 7 million tons of organics in 2024
- ‘Operational readiness is high’ as Oregon rolls out EPR
- Pizza box demand declining, report says