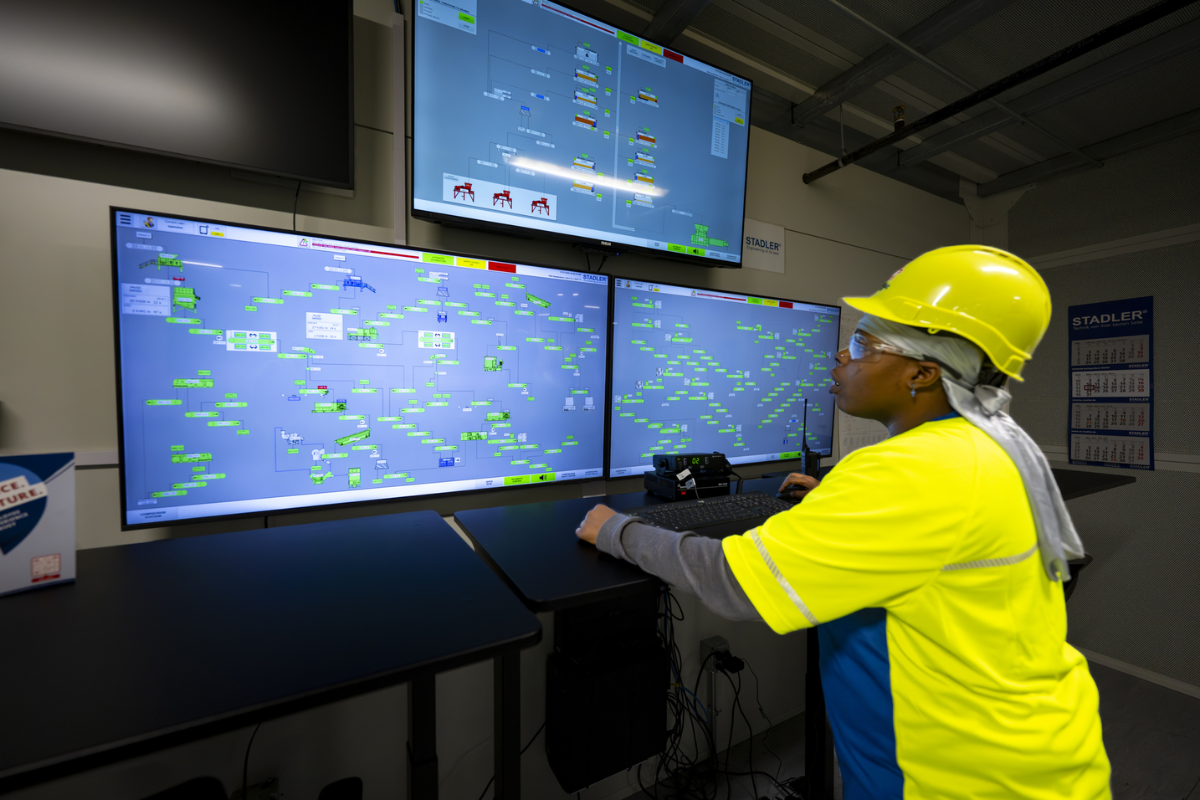
The hauler has been pre-buying post-consumer bales from across the Midwest for several months for the complex, which features a Polymer Center and the Blue Polymers resin production plant. | Photo courtesy Republic Services
Republic Services officially opened its Indianapolis plastics recycling complex this week, marking the hauler’s entry into the recycled plastic resin market and continuing its expansion from supplying bales to processing and converting the plastics reclaimed within.
The new Midwest site houses a Republic Services Polymer Center and a Blue Polymers resin plant, the latter of which is a joint venture with plastics distributor Ravago.
Although the Indianapolis Polymer Center is already producing PET flake, “I wouldn’t suggest that that flake is absolutely on-spec today, so the material we’re producing today will probably go to market as wide-spec,” Pete Keller, vice president of recycling and sustainability at Republic Services, told Plastics Recycling Update.
The company is starting to ship the flake to pelletizers and bottle preform manufacturers for certification, which takes about 30-60 days, Keller said. The Blue Polymers plant has purification, extrusion and pelletizing capabilities and later will add blending and compounding services. The site’s technology also can differentiate between food- and non-food-grade polymers, he said.
The facility is designed to run 24/7 but won’t be at that rate for now, Keller said, adding that over the next two months the company will work to ramp up production, ultimately expecting uptime of around 80-90%.
The site is the first of four planned projects to be completed, each consisting of a Polymer Center and a Blue Polymers resin plant. The first Polymer Center opened in Las Vegas in late 2023, and its companion Blue Polymers location is under construction in Buckeye, Arizona, and is scheduled to start up late this year.
The company plans to announce the third site, in the Northeast, in the next couple months, with groundbreaking in June or July and startup in late 2026 or early 2027. The fourth site will have “more of a South focus,” Keller said, and may be announced later this year, with expected startup about 12 months after the third site. In addition, the company may consider adding two more complexes if demand supports it.
The Las Vegas center began supplying PET flake to Coca-Cola in January 2024 and has a long-term offtake agreement with Circularix.
Each pair of facilities will be able to produce 175 million pounds or 80,000 metric tons of recycled plastic annually, according to a press release. That capacity is split 50/50 between PET and polyolefins, Keller said.
Although Keller did not directly disclose what portion of output was contractually obligated, he said the Las Vegas center is sold out, and “we’re kind of sold out here in Indianapolis.” The company reserves perhaps 20% of the PET to offer to “different customers that may be making investments that are novel or unique.” And the entirety of the HDPE and PP flake goes to Blue Polymers, he said, adding those volumes are sold out as well.
Although clear, hot-washed PET flake used in beverage bottling is the focus for Republic, the new facility appears to be bolstering post-consumer polyolefins markets.
Pre-buying contributes to tightening bale market
Republic began buying bales about eight or nine months ago, Keller said. About 60% of the feedstock requirements originate from Republic’s collection operations or what Keller called the company’s “recycling shed,” which reaches throughout the Midwest and extends into the Southeast, from Minneapolis to Memphis, the Carolinas to Michigan.
That leaves about 40% of bale supply to come from third parties. “We haven’t necessarily struggled with finding that third-party volume,” he said, though “we have to offer something.” That something could be a higher price, ease of doing business or consistency, he said.
This is common in relationship-based recycled commodity markets, where a buyer may prefer to sell not necessarily to the highest bidder but to customers who not only will actually pay for delivered loads but also will return to buy more. Consistency in supply also is key to buyers, since recycled material quality varies far more than virgin resin and can significantly affect performance and appearance.
Over the past five to seven years, Republic has shifted away from sorting curbside recyclables into mixed plastics bales and focused on producing color PP bales, Keller said. And while Republic is “certainly” bringing PP bales in to be processed in its Polymer Centers, it also is handling mixed plastic bales for certain customers to be batch-processed, he said.
Since Republic’s Indianapolis site was announced in October 2023, regional bale distributors have expressed concern about the increased pull for post-consumer plastics bales and the impact on prices. Although bale pricing can have many factors, supply and demand are the biggest drivers.
For example, post-consumer bales of natural HDPE have attracted particular attention in recent months, tipping over the $1 per pound level, which was last seen in October 2021, according to RecyclingMarkets.Net data.
While spot pricing factors into how Republic sorts its bales, “we can’t lose sight of our business,” Keller said. For example, agreements with municipal customers often are indexed to a published price, so “we still have to carry that all the way back through to the customer.”
Transportation also figures into how the company sorts plastics – not just the literal miles between supplier and buyer, but also whether the route offers a profitable backhaul or fronthaul, in the case of inbound material, he said.
While the Las Vegas Polymer Center uses a dedicated transportation model rather than a pool of trucking companies, the Indianapolis site has a hybrid system. With the heavy back-and-forth trucking traffic in the Midwest, “there’s just a lot more opportunity here to put those channels together than in the West,” Keller said, and with a big focus on the total landed cost of materials, Republic is always looking to optimize freight rates.
The site also has rail capabilities, he added. Nova Chemicals cited similar logistical considerations for its new LLDPE film processing plant near Indianapolis, which opened last month.
Developing end uses
In addition to separating out in-demand natural polyolefins, the facility can color-sort into white, red, orange, yellow and “other,” which is largely blue and green, Keller said.
“We think over time we can figure out something useful to do with that (other) material,” he said. “And when I say ‘useful,’ it can go into something that’s not gray or black,” which opens up more potential end markets.
In the end, “we want it to go back into packaging, so that that color sortation will allow us to do interesting things over at Blue with that material.”