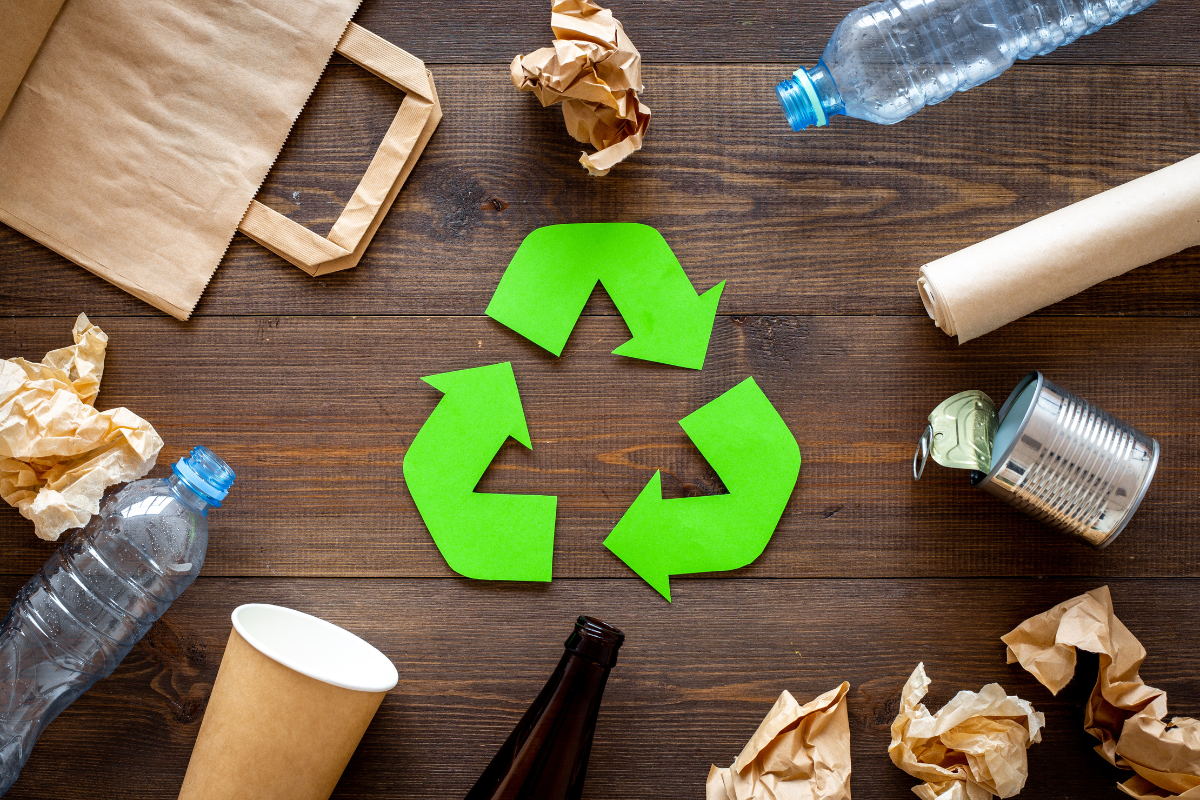
Traceability tools can act as a scorecard, providing proof that recycling works and helping counter an often one-sided narrative in consumer media outlets. | 9dream Studio/Shutterstock
Editor’s note: Learn more about traceability technology and many other topics at the 2025 Plastics Recycling Conference on March 24-26 in National Harbor, Maryland.
The increasing adoption of post-consumer resin is set against a backdrop of growing public mistrust and a frequent lack of clarity, but emerging traceability tools can provide transparency to build trust with consumers as well as supply chain partners.
Consumers participating in curbside recycling programs assume their materials are going back into the circular economy, then often see misleading media coverage of trackers gone awry and low plastic recycling rates, said Bill Robberson, president and chief technical officer of Kamilo. The company’s software uses geospatial technology to provide supply chain visibility and third-party confirmation of the recycled resin content in plastic products.
“For many people, the messages are contradictory,” he said during a recent podcast produced by the Association of Plastic Recyclers. APR owns Resource Recycling, Inc., which publishes Plastics Recycling Update.
Kamilo’s technology is hosted on a portal provided by Esri, a geographic information systems software company, and integrates information on shipments of bales, resin or products with GIS layers containing information on transportation systems, land use, natural features, utilities and more.
Robberson is among the panelists for “Leveraging Technology for Lifecycle Traceability” at the Plastics Recycling Conference, March 24-26 at National Harbor, Maryland. Stan Chen of RecycleGo and Ed Dominion of D6 will round out the panel.
Traceability acts as a scorecard of sorts, Robberson said, providing proof that recycling works and helping counter an often one-sided narrative: “In the eyes of much of the media, post-consumer plastic recycling is broken.” To this point, The Recycling Partnership in a recent blog post emphasized the need for industry to show the progress being made in recycling and offset “incomplete journalism.”
Increasing transparency also can enhance the growing number of extended producer responsibility programs for packaging, he said. “Without traceability, EPR policies risk becoming another loophole to be exploited by businesses, and that leaves us stuck in the same cycle in effective waste management.”
“Easy money is made in darkness,” even if the opacity is unintentional, he said.
Cost, proprietary data are top client concerns
Potential clients often think enhancing accountability will be a costly endeavor. “Traceability isn’t expensive from our perspective, but audits are, and they’re time-consuming,” Robberson said. And although many companies are making good-faith efforts at transparency, “a lot of them are self-certifying.”
Third-party standards are available, including PCR certification from APR, but companies may not have a clear vision of how to share that information with the public. And in the absence of mandated reporting, some companies may not feel compelled to share any components of their process, though Robberson said there’s value in providing transparency at any level.
“It’s a new world for a lot of people to actually expose yourself, even if it’s only internal, within the organization,” he said.
Any company has proprietary information that’s best left opaque, but effective traceability systems can enhance accountability without compromising trade secrets or a competitive advantage, Robberson added.
As an example, one municipality was reluctant to disclose the buyers for its curbside commodities, given its exposure to Freedom of Information Act requests. So Kamilo provided a redacted report, and much like many traceability systems, the client controls what information is ultimately shared and with whom.
“Advancements in traceability and attribution could be a double-edged sword for companies using plastics,” said George Gigounas, partner at global law firm DLA Piper. These developments could enhance the credibility and reputation of plastics producers and reduce claims or disputes from plaintiffs and regulators, and potentially help inform emerging workflows and technologies within the recycling industry.
But traceability could also enable plaintiffs who are intent on suing producers to make their allegations more specific as far as who produced the plastics that are creating pollution, Gigounas said. Likewise, the information gleaned from these systems could reveal inefficiencies and create vulnerabilities in environmental marketing claims.
“Overall, developments in traceability and attribution science and technology should be watched closely for both helpful progress and risks,” he said.
Gigounas and attorney Jesse Medlong, also with DLA Piper, will explore the topic further in “The Evolving Legal Landscape for Plastics” session during the Plastics Recycling Conference.
Ed Dominion, president and founder of RPET processor D6, views traceability as a tool to help with EPR programs and to help compensate for reporting gaps in trade data. With imported RPET becoming more prevalent, providing proof of origin as well as actual content becomes ever more vital, Dominion said. Imported material is “getting rubber stamps, but nobody’s actually going to the sites to audit it.”
Dominion’s Texas-based company operates globally and provides visibility throughout the chain of custody, from bale to shelf, to ensure transparency and sustainability at every stage, he said. Otherwise, in the absence of an enforceable U.S. law or code, “it’s kind of scout’s honor” whether PCR is truly post-consumer rather than regrind or even virgin resin.
D6 has integrated radio frequency identification technology to track recycled materials in a pilot project with Walmart and Sam’s Club, Dominion said.
Global supply chains, regulations are increasingly disparate
The fragmented nature of the global recycling industry – especially pronounced in the U.S., where states are implementing widely varying rules – lends itself to the need for accountability, according to a 2024 white paper from nonprofit Delterra and system change investment company Systemiq.
Without a reliable, centralized system, data varies among regions and organizations, the authors wrote, and these inconsistencies stymie attempts at adopting PCR and bringing recycling infrastructure to scale. One example of these inefficiencies, the authors added, is the growing list of missed sustainability targets.
In mid-2023, Delterra, headquartered in Washington, D.C., concluded a pilot project that used blockchain technology to promote data sharing and ethical sourcing for recycled materials. The company’s software creates a product passport for recycled materials, using bar codes and QR codes along with blockchain technology.
The future is now in Europe
Parts of the recycling landscape in Europe can be seen as a peek into what could later become common in the U.S. For example, mandatory digital product passports are being implemented in the EU, with industrial and EV batteries comprising the first sector and all other categories of consumer goods to follow by 2030.
Although the full rollout is several years away, “leading companies are getting involved early, particularly to leverage knowledge of their place in the value chain to understand and influence how DPPs will actually be implemented,” said Jon Powell, founder and CEO of Apex Catalytic, a specialty firm that advises companies and investment funds on sustainability challenges, including with new technology platforms. Powell led the “Enhancing Transparency in Electronics Recycling” panel at Resource Recycling’s E-Scrap Conference in October 2024.
In a recent webinar, Netherlands-based Circularise – along with representatives from chemical company Covestro Deutschland, appliance maker Electrolux Italia, Belgian flooring and insulation company Unilin – explored how the traceability platform has contributed to an EU project to help develop circular systems for rigid polyurethane foams.
Citing Deloitte data, Circularise’s Teresa Oberhauser, head of EU research and government relations, said 60% of procurement leaders have little or no visibility into their full supply chains.
For nearly four years, Circularise and several corporate partners have participated in the Circular Foam EU project, focusing on hard-to-recycle foam products. Rigid or slabstock foams used as insulation materials for household appliances and construction comprise a rapidly growing segment amid efforts toward energy efficiency.
For Covestro Deutschland, transparency is crucial for compliance with regulations despite the associated challenges, Dorota Pawlucka, global alliance manager, said during the webinar. As Covestro works to develop recycling technologies for polyurethanes, tracking its own products making their way into refrigerators and other products helps the company get the materials back to evaluate for recycling, she said.
The company benefits from seeing what happens to the rigid foams throughout the supply chain – for example, what other chemicals are added later in the process that could become harmful during recycling processes. Covestro wants to make sure all the components function together as part of a system, Pawlucka said.
At Unilin, part of Mohawk Industries, sustainability engineer Aster Onderbeke said traceability had enormous value for sorting facilities, and detecting complex materials early in the process provides insight for future capabilities.
Corrado Cecchini, global technology food preservation insulations and materials director at Electrolux Italia, said it was not difficult to collect the data to include in the product passport – when it comes from larger suppliers. When it comes to smaller, more local suppliers who are not well structured to provide data, it’s much more challenging but still can be done using technical specifications sheets, or by spending time with the supplier to convince them to provide more raw data on their materials.