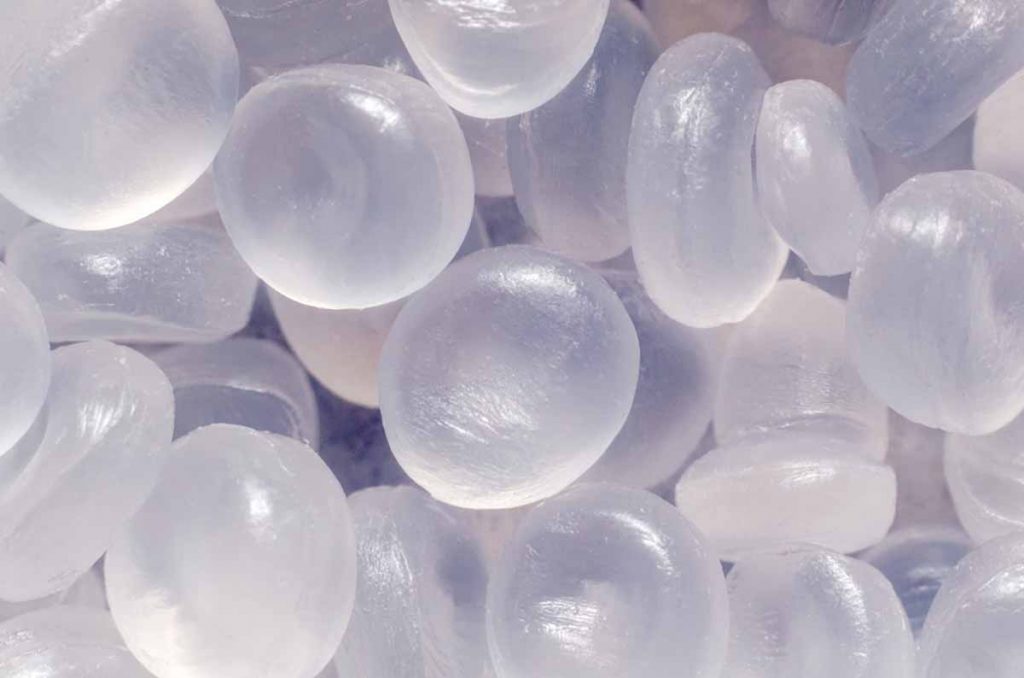
Professors and students developed a process to turn both PE and PP into propylene monomer. | Afanasiev-Andrii/Shutterstock
Researchers at the University of California, Berkeley, have developed a chemical process to vaporize PE and PP into the feedstock monomer propylene.
The catalytic process, developed at the university, works equally well with the two most common post-consumer plastics – PE and PP – as well as mixed resins, the researchers said in a press release.
PE is made using ethylene, which in the U.S. typically results from steam-cracking natural gas liquids including ethane. Ethylene is in abundant supply, and PE is by far the biggest outlet.
In contrast, propylene demand is growing, while refineries – historically the primary source of propylene – are gradually disappearing. Propylene is increasingly produced on purpose using propane dehydrogenation, which removes hydrogen, to exploit regional abundance of natural gas liquids rather than crude oil. It also is a co-product of steam cracking, in different proportions depending on the feedstock used.
A paper detailing the new process was published in the journal Science on Aug. 29. The work was funded by the U.S. Department of Energy.
The researchers included additives and different plastics in the reaction chamber to see the effect of contaminants. Small amounts of some impurities barely affected the process, but even small quantities of PET and PVC significantly reduced the efficiency.
PVC is not as widely recycled due to the chlorine content, which erodes machinery, as well as the presence of plasticizers used to make the resin flexible – for example, vinyl flooring and wire/cable insulation. PET is incompatible with current HDPE recycling processes.
“We have an enormous amount of polyethylene and polypropylene in everyday objects, from lunch bags to laundry soap bottles to milk jugs — so much of what’s around us is made of these polyolefins,” said John Hartwig, a UC Berkeley professor of chemistry who led the research.
“What we can now do, in principle, is take those objects and bring them back to the starting monomer by chemical reactions we’ve devised that cleave the typically stable carbon-carbon bonds. By doing so, we’ve come closer than anyone to give the same kind of circularity to polyethylene and polypropylene that you have for polyesters (PET) in water bottles.”
A video by UC Berkeley graduate student R.J. Conk explains the catalytic process.
In 2022, Hartwig and his team developed a process to break down PE bags into feedstock propylene, which then could be reused to make PP resin. Since then, the team has replaced metal catalysts with ones more common to the chemical industry, lowering costs and increasing reusability of the catalyst.
In the press release, Hartwig said that while many researchers are hoping to redesign plastics from the ground up to be easily reused, today’s hard-to-recycle plastics will be a problem for decades.
“One can argue that we should do away with all polyethylene and polypropylene and use only new circular materials. But the world’s not going to do that for decades and decades. Polyolefins are cheap, and they have good properties, so everybody uses them,” Hartwig said.
Co-authors include graduate students Jules Stahler, Jake Shi, Natalie Lefton and John Brunn of UC Berkeley and Ji Yang of Lawrence Berkeley National Laboratory. Shi, Hartwig and Alexis Bell are also affiliated with Berkeley Lab.